
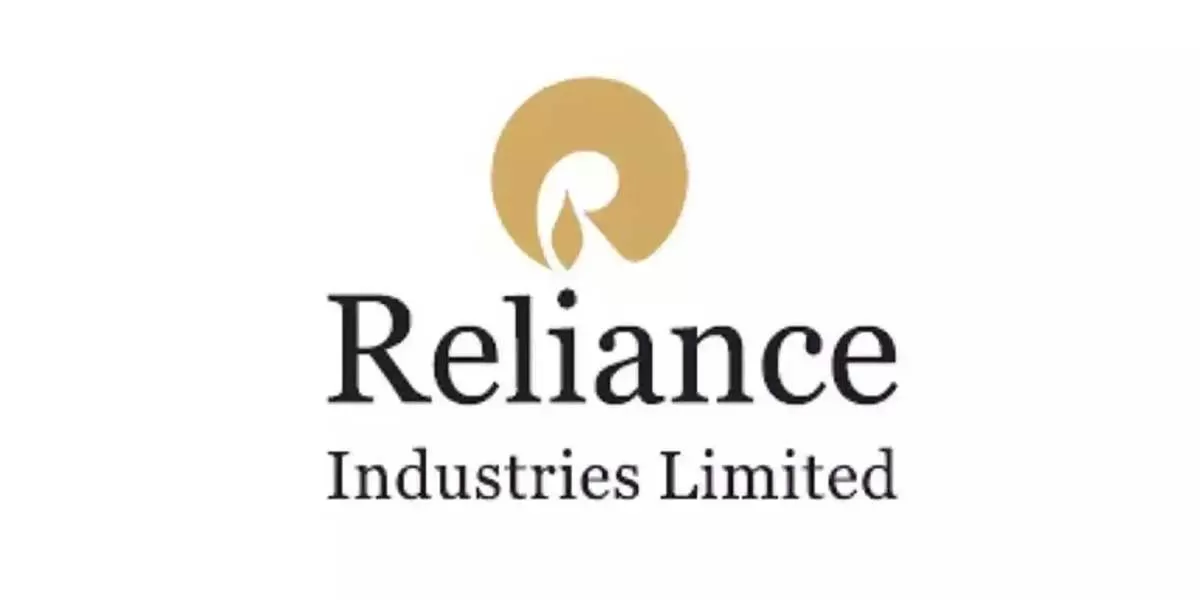
Andhra Pradesh to Develop 30,000 Women-Led Enterprises by 2025
The Municipal Administration and Urban Development (MAUD) Department is accelerating efforts to create sustainable livelihoods for women in urban areas, in line with Chief Minister Nara Chandrababu Naidu’s goal of fostering one lakh women entrepreneurs by 2025. Under this initiative, the MAUD Department has set a target to establish 30,000 women-led enterprises across towns and cities in Andhra Pradesh. To support this vision, the department plans to establish Micro, Small & Medium Enterprises (MSMEs) for women in TIDCO housing complexes. Vacant plots across 163 colonies have been earmarked ..
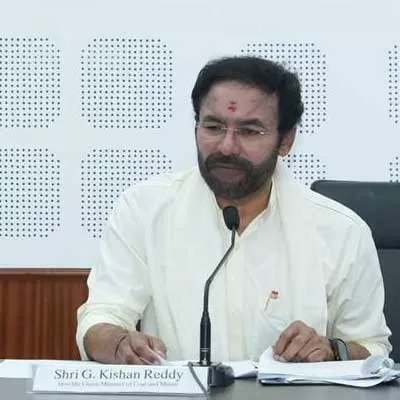
G Kishan Reddy discusses mining expansion, clearances with Chhattisgarh CM
Coal and Mines Minister G Kishan Reddy met Chhattisgarh CM Vishnu Deo Sai on Friday to expedite land acquisition and environmental clearances for mining projects. Reddy, who was on a two-day visit to review operations at South Eastern Coalfields Ltd (SECL), discussed measures to boost mining-led economic growth in the state. Key topics included speeding up land acquisition for mine expansions, obtaining quicker environmental approvals, and setting up integrated rehabilitation and resettlement sites. The minister also highlighted the importance of developing critical minerals in the region, alo..
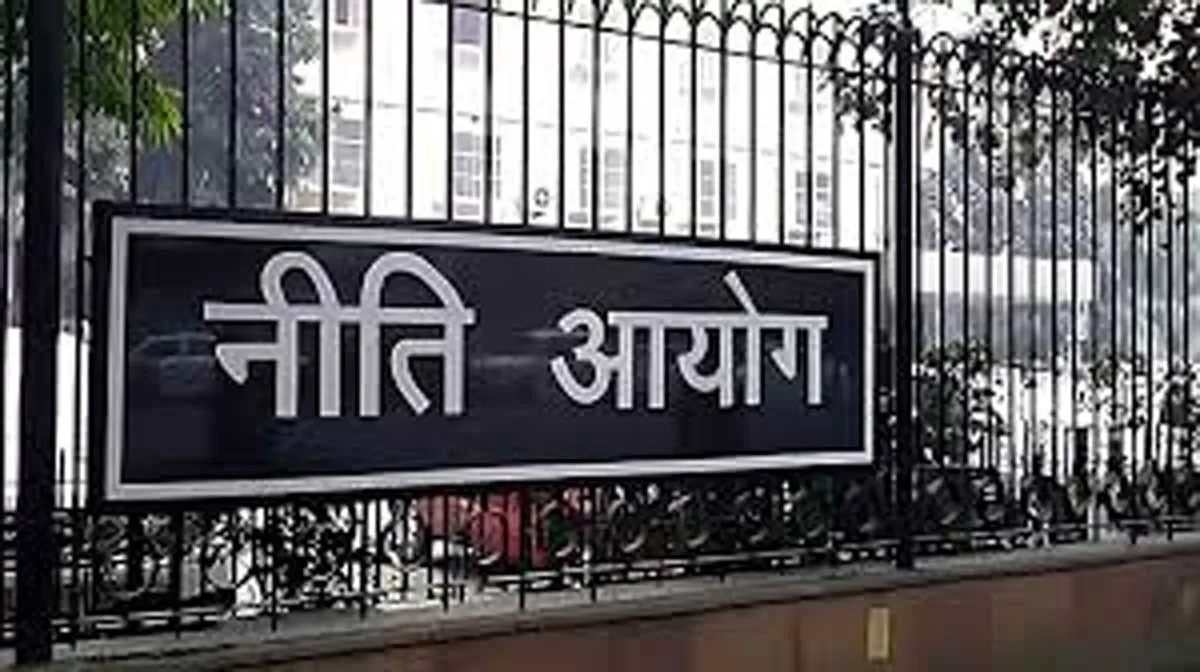
NITI Aayog's Vision for India's Auto Industry
NITI Aayog has launched the report titled "Automotive Industry: Powering India’s Participation in Global Value Chains," offering a roadmap for the country’s automotive future. Released by Shri Suman Bery, Vice Chairman, the report outlines key strategies to grow India’s automotive sector to $145 bn in component production by 2030. India is currently the fourth-largest automobile producer globally, but with only a modest three per cent share in the global automotive component market. The report emphasises the need to strengthen India’s position through competitive manufacturing, skill d..