"Effective Tips for Outdoor Fitness Exercising"
Read full article
CW Gold Benefits
- Weekly Industry Updates
- Industry Feature Stories
- Premium Newsletter Access
- Building Material Prices (weekly) + trends/analysis
- Best Stories from our sister publications - Indian Cement Review, Equipment India, Infrastructure Today
- Sector focused Research Reports
- Sector Wise Updates (infrastructure, cement, equipment & construction) + trend analysis
- Exclusive text & video interviews
- Digital Delivery
- Financial Data for publically listed companies + Analysis
- Preconceptual Projects in the pipeline PAN India
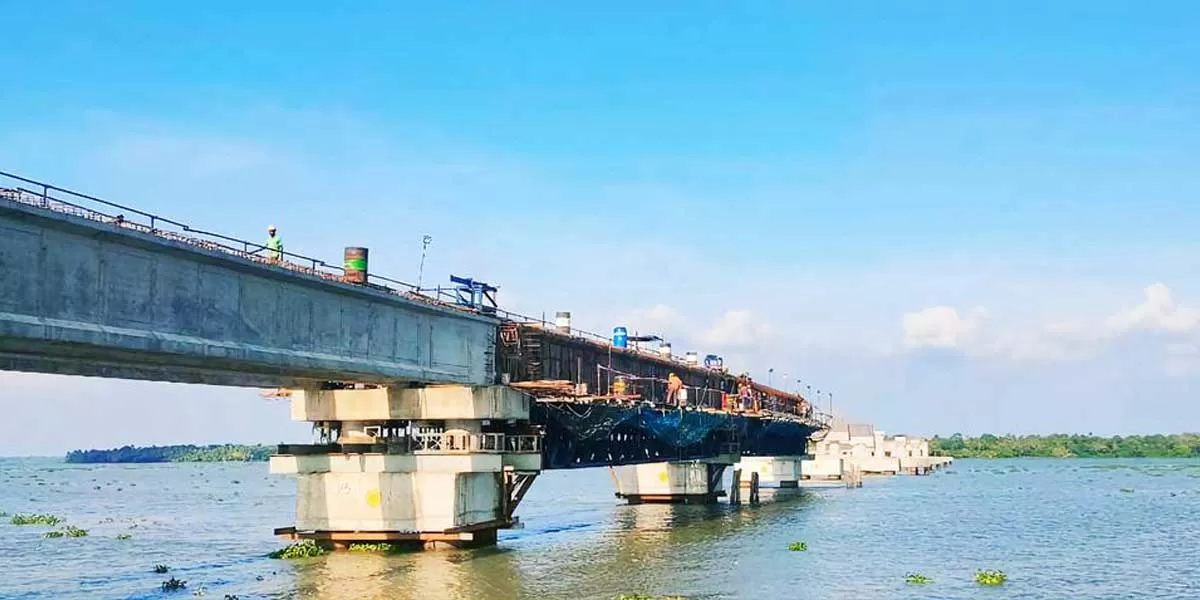
Vaduthala-Perandoor Bridge Project: Funds Allotted for CRZ Study
In a step towards constructing the long-awaited Vaduthala-Perandoor bridge, the Kerala state government has allocated Rs 1.5 million to conduct a Coastal Regulation Zone (CRZ) study for the project. This allocation is part of the Rs 325 million administrative approval granted earlier. Ernakulam MLA T.J. Vinod stated that the National Centre for Earth Science Studies (NCESS) in Thiruvananthapuram is tasked with preparing the CRZ study and report. The report will be submitted to the Kerala Coastal Zone Management Authority (KCZMA) for approval, which is essential before initiating the tendering..
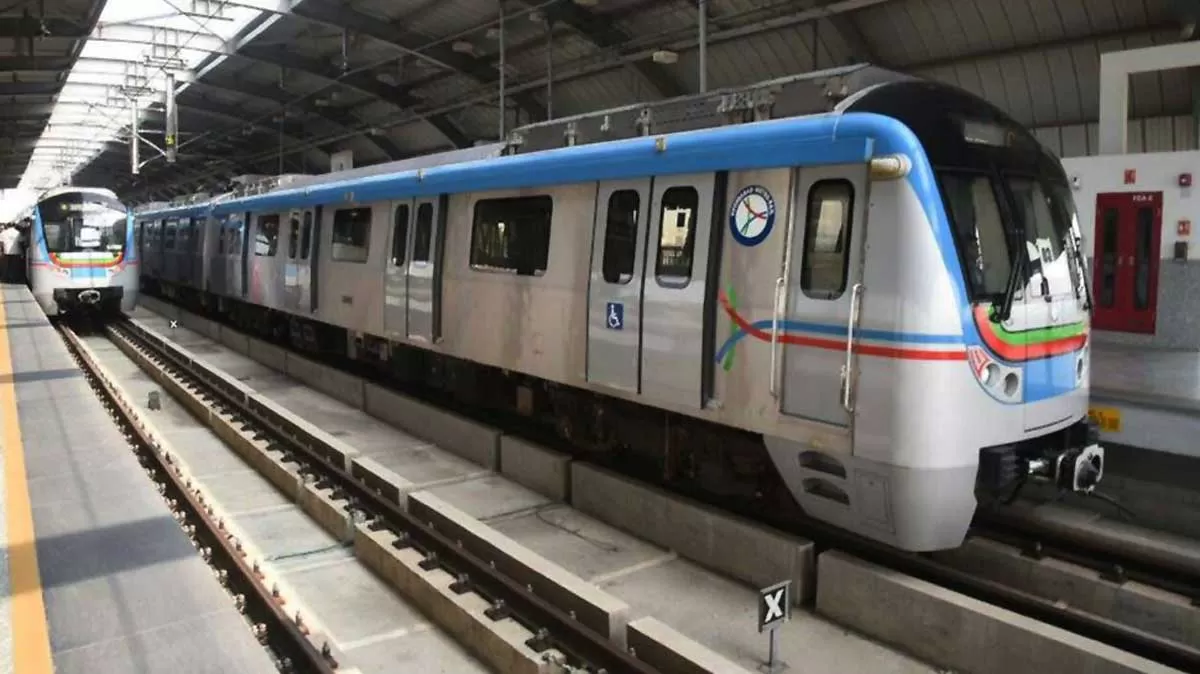
Hyderabad Metro Phase-II to Add 76.4 km, 54 Stations
The Phase-II expansion of the Hyderabad Metro will add 76.4 kilometers across 54 stations at a cost of Rs 242.69 billion, according to NVS Reddy, Managing Director of HAML and HMR. Announced on Monday, this expansion responds to increasing demand for enhanced urban transit infrastructure. Part A of the project includes five new corridors: Shamshabad to RGIA Airport, Raidurg to Kokapet Neopolis, MGBS to Chandrayangutta (Old City), Miyapur to Patancheru, and LB Nagar. Part B involves extending the RGIA line to the proposed Fourth City (Skill University), creating a sixth corridor. “These cor..
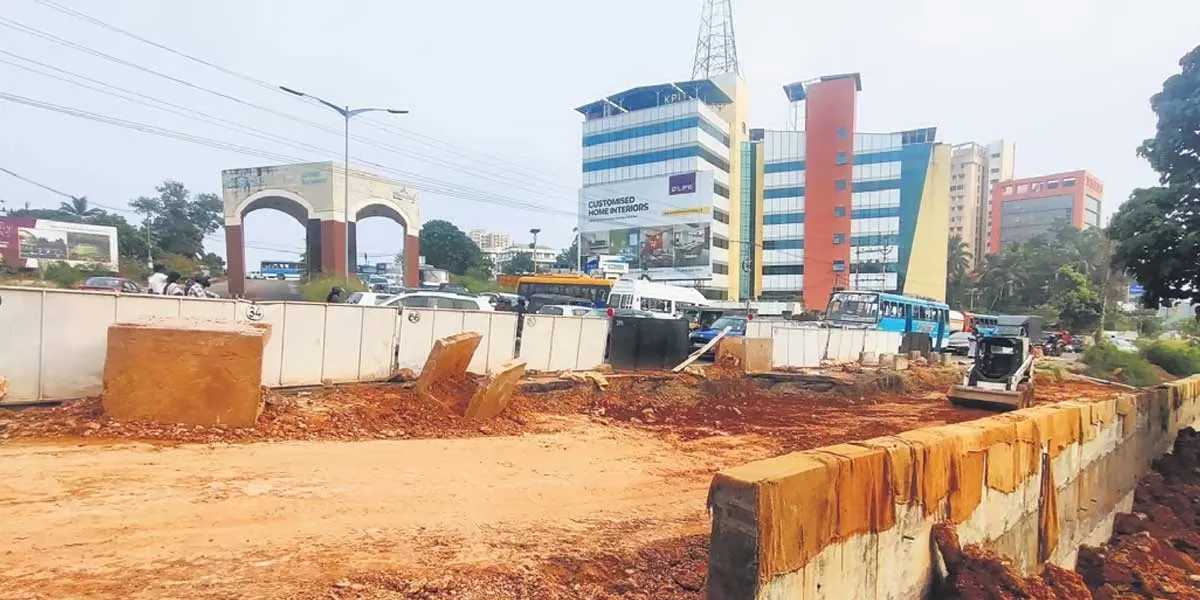
Kochi's Infopark Connectivity Set for Major Boost
Connectivity to Infopark is set to improve significantly with enhanced transport services and progress on key infrastructure projects. Tech professionals at the campus, which employs nearly 75,000 people and over 1 lakh when including Smart City and Kinfra Park, eagerly anticipate the introduction of e-feeder bus services. "Feeder buses have been a long-standing demand. Their deployment will encourage many employees to switch to water transport. However, last-mile connectivity remains a challenge," said Anish Pandalani, state president of Progressive Techies. He also urged for improved KSRTC ..