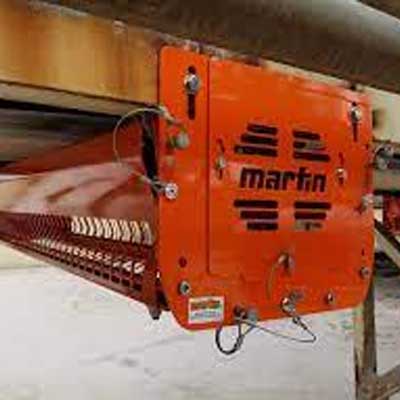
Martin Engineering: Challenging Conveyor Safety Myths
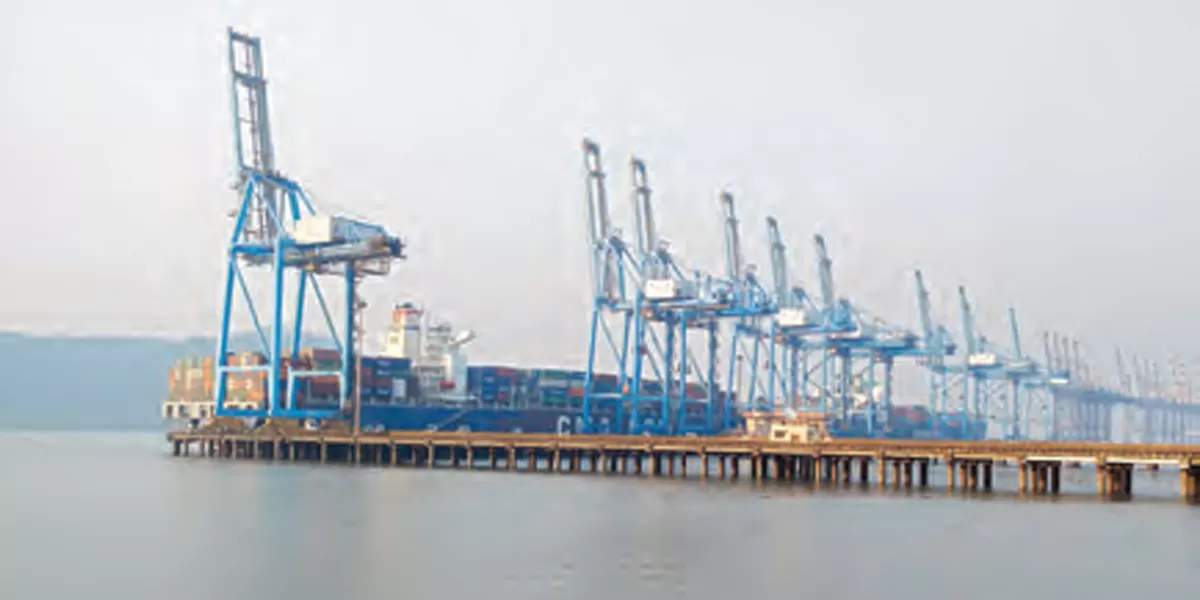
JNPA Becomes First Indian Port to Cross 10 Million TEU Capacity
The Jawaharlal Nehru Port Authority (JNPA), located at Uran in Navi Mumbai, has become the first port in India to achieve over 10 million TEUs (twenty-foot equivalent units) in container handling capacity.With the recent expansion, the port now operates five container terminals with a combined capacity of 10.4 million TEUs, alongside two liquid and two general cargo terminals.Handling more than half of India’s container traffic, JNPA processed 7.05 million TEUs in 2024 and has moved 15.39 million tonnes of containers and 16.64 million tonnes of total cargo in the first two months of FY 2025â..

Nod for Rs. 36.26 billion Expansion of Pune Metro Line 2
The Union Cabinet has approved the Rs.36.26 billion expansion of Pune Metro Line 2, adding 12.75 km of track and 13 new stations to improve east–west connectivity across the city.The project aims to link Pune’s urban core with rapidly growing suburbs, supporting the city’s rising demand for efficient and sustainable transport solutions. This expansion is part of Corridor 2 of the Pune Metro and includes two key routes: Vanaz to Chandani Chowk (Corridor 2A) and Ramwadi to Wagholi/Vitthalwadi (Corridor 2B).It will connect residential, IT, and educational hubs in areas such as Bavdhan, Koth..
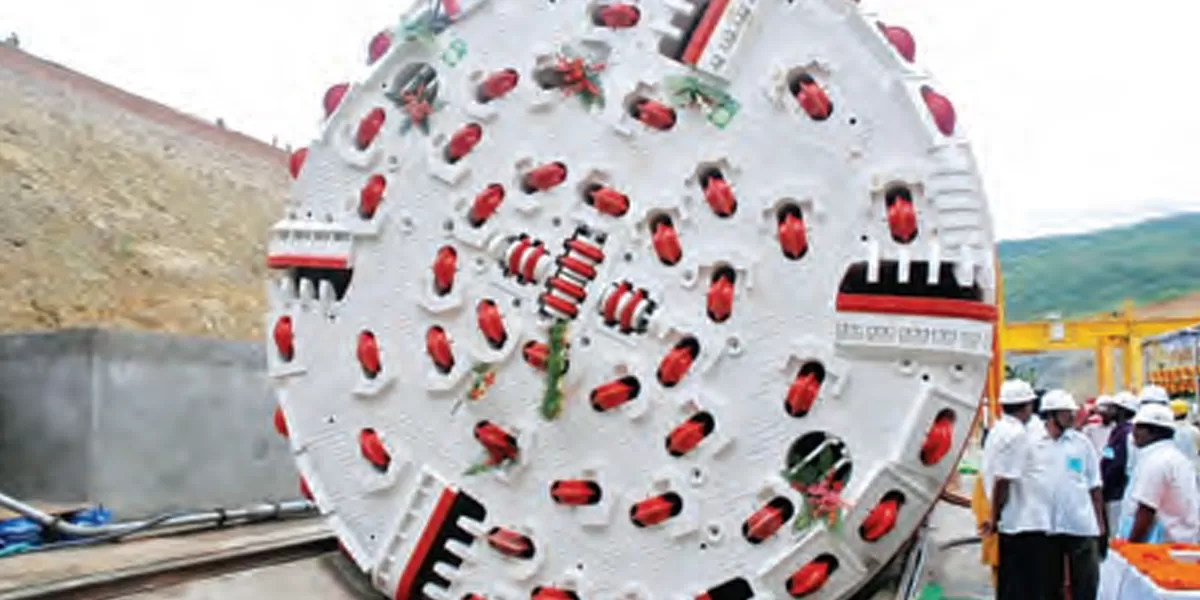
Assembly begins for ‘Nayak’ TBM on Thane– Borivali Twin Tunnel Project
The assembly of ‘Nayak’, the first of four Tunnel Boring Machines (TBMs) for the Thane–Borivali Twin Tube Tunnel Project, has commenced at the Thane site. Built by German firm Herrenknecht AG and deployed by Megha Engineering & Infrastructure (MEIL), the TBM marks a key milestone in Mumbai’s ambitious 11.8-km underground road corridor beneath Sanjay Gandhi National Park.The twin tunnels will reduce the Thane–Borivali travel distance by 12 km and decongest Thane Ghodbunder Road. ‘Nayak’, with a 13.2-metre diameter, is designed to bore through challenging geological conditions ..