
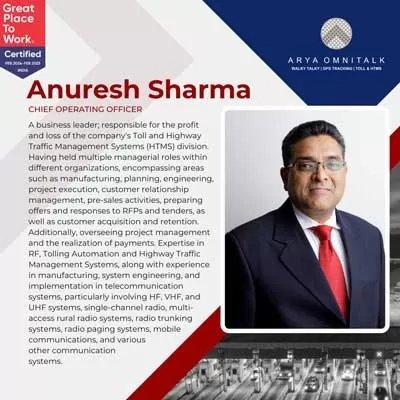
Arya Omnitalk Powers India’s Toll Revolution with AI-Driven Solutions
Arya Omnitalk, a leader in intelligent transportation systems, is revolutionising toll collection across India’s national highways with its advanced AI-powered Toll Management Solutions. Designed for rugged remote toll locations, the company’s cutting-edge technology ensures seamless, reliable, and secure tolling—especially during high-capacity operations exceeding 200%. By integrating real-time analytics, cyber protection, and FASTag-based cashless tolling, Arya Omnitalk’s systems are significantly reducing congestion, improving transparency, and enhancing revenue assurance. Its full..
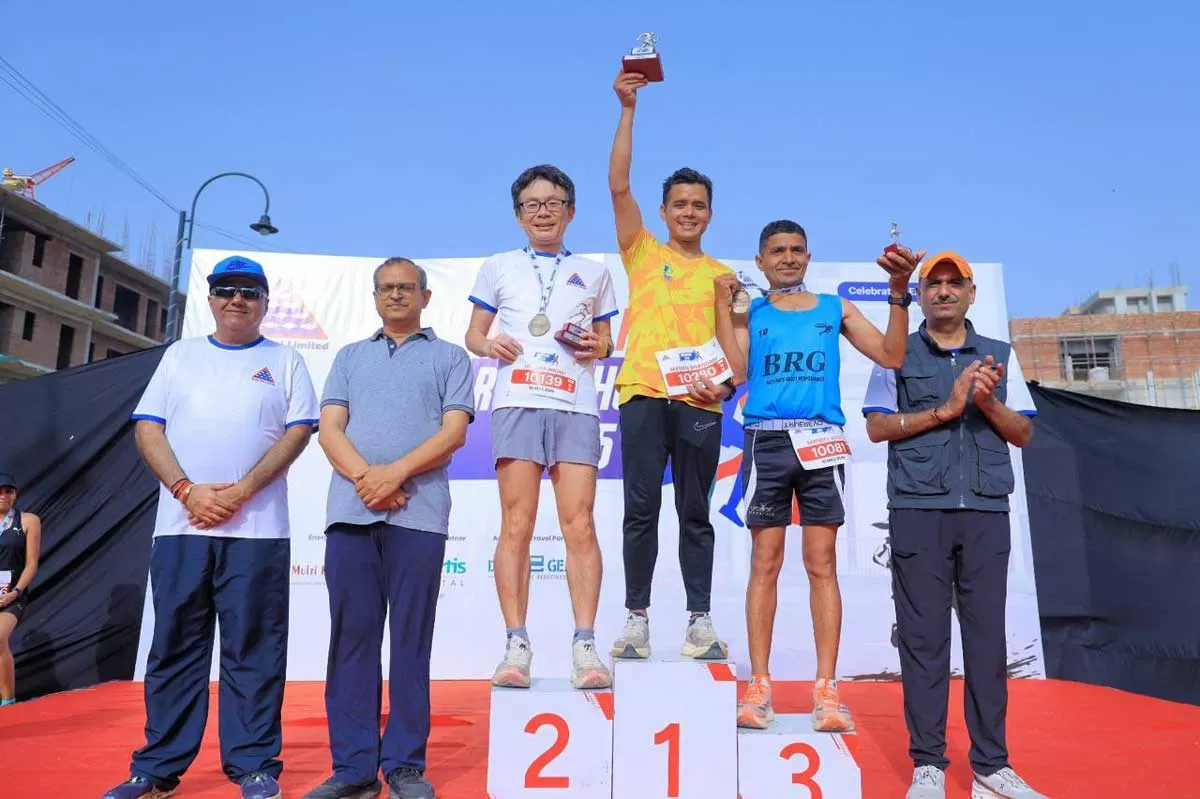
Over 800 Join Anant Raj Runathon to Mark Earth Day
Over 800 participants came together at Anant Raj Estate, Sector 63A, Gurugram, for the Anant Raj Runathon 2025—a vibrant celebration of Earth Day through fitness, community bonding, and sustainability. Curated by renowned running coach Ravinder, the event featured four categories: 10-mile and 5-mile timed runs, a 5-mile walkathon, and a 1-mile kids’ run. Runners of all ages took to the green, scenic roads of the area—some chasing personal bests, others running for a cause. The Runathon was designed to promote healthy living while raising awareness about sustainable practices. Participa..
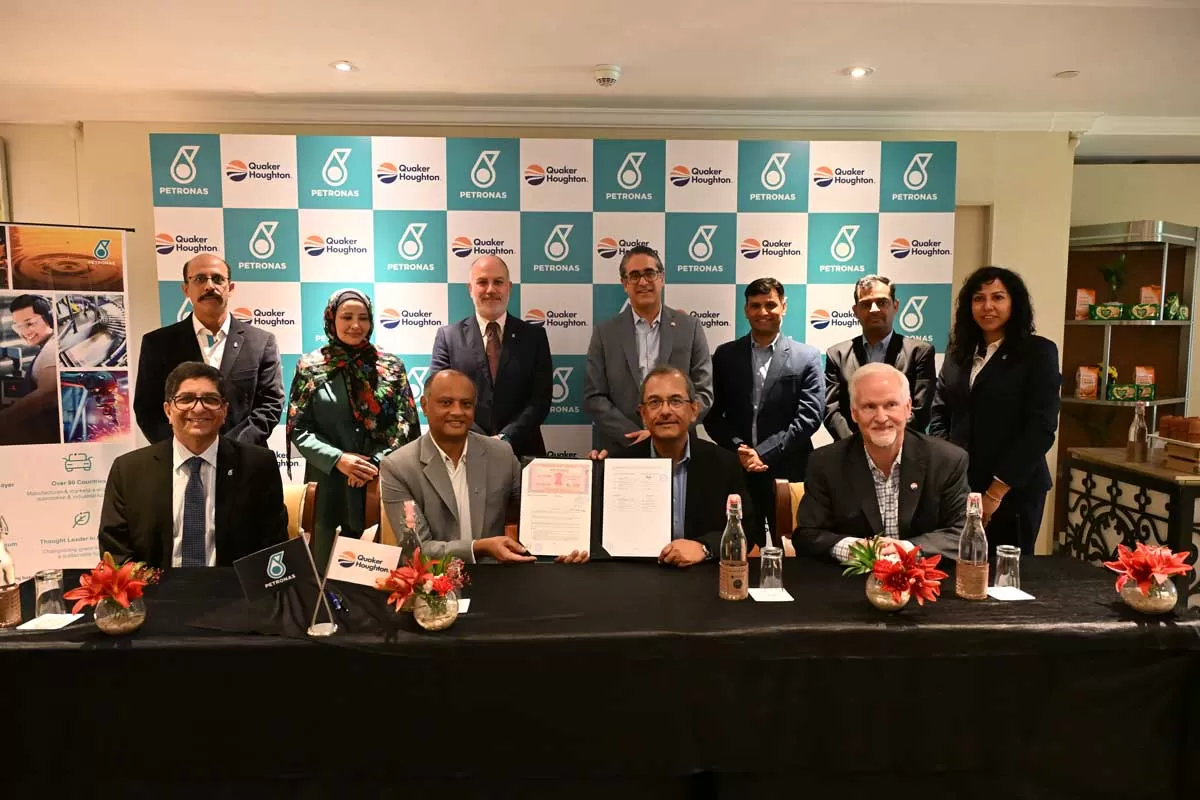
PETRONAS Lubricants, Quaker Houghton Ink Strategic Deal
In a significant step towards strengthening industrial operations in India and Malaysia, PETRONAS Lubricants India Pvt. Ltd (PLIPL) and Quaker Houghton have announced a strategic partnership aimed at delivering high-performance industrial fluid solutions to key manufacturing sectors, including steel production. The collaboration combines the strengths of both companies—leveraging PETRONAS Lubricants India’s maintenance lubricant technologies and Quaker Houghton’s deep expertise in metalworking fluids. Starting from the second quarter of 2025, Quaker Houghton will begin offering PETRONAS..