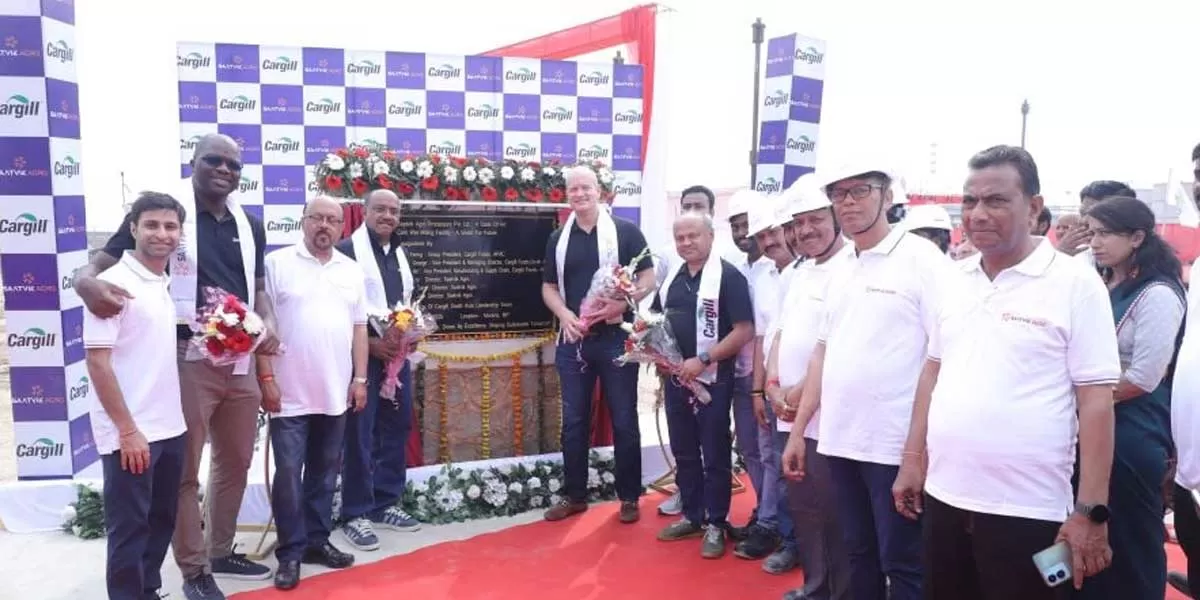
Cargill Inaugurates New Corn Milling Plant to Meet Growing Demand
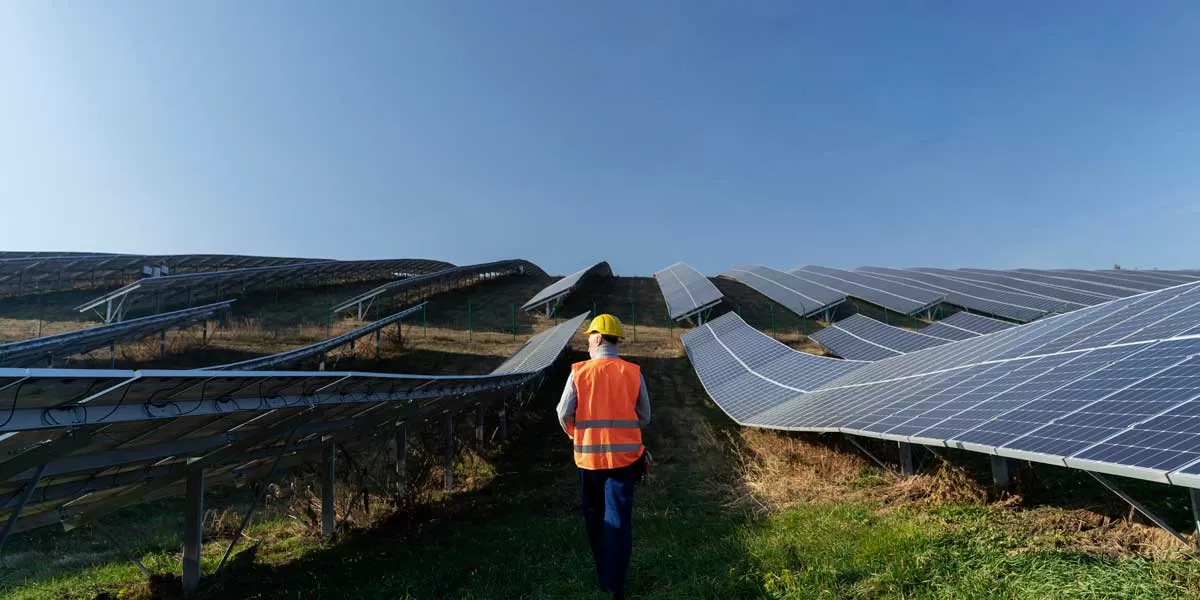
SWELECT Secures 150 MW Solar Orders
SWELECT Energy Systems, a leading player in India’s renewable energy sector, has secured orders exceeding 150 MW for its high-efficiency TOPCon Bi-facial solar PV modules. These orders highlight the company’s technological leadership and strong market credibility.SWELECT maintains a 100 per cent success rate in module testing, with every unit passing TÜV and accredited lab evaluations on the first attempt. Additionally, the modules, backed by third-party reinsurance, are undergoing Extended Reliability Testing (ERT) to ensure long-term performance.In a major financial move, SWELECT has ra..
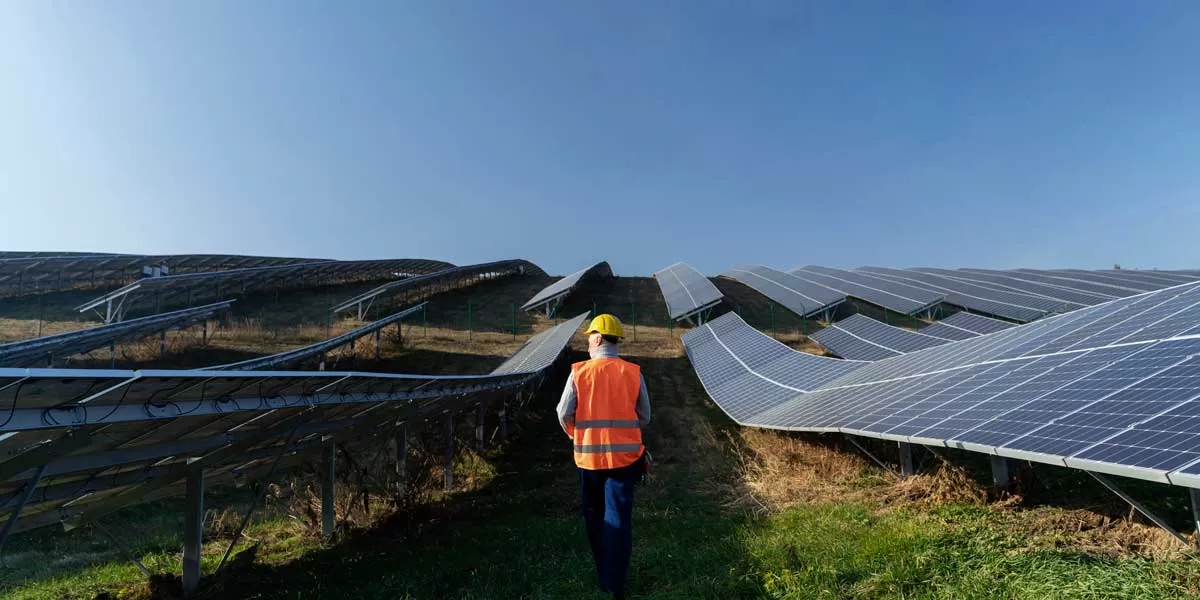
SWELECT Secures 150 MW Solar Orders
SWELECT Energy Systems, a leading player in India’s renewable energy sector, has secured orders exceeding 150 MW for its high-efficiency TOPCon Bi-facial solar PV modules. These orders highlight the company’s technological leadership and strong market credibility.SWELECT maintains a 100 per cent success rate in module testing, with every unit passing TÜV and accredited lab evaluations on the first attempt. Additionally, the modules, backed by third-party reinsurance, are undergoing Extended Reliability Testing (ERT) to ensure long-term performance.In a major financial move, SWELECT has ra..
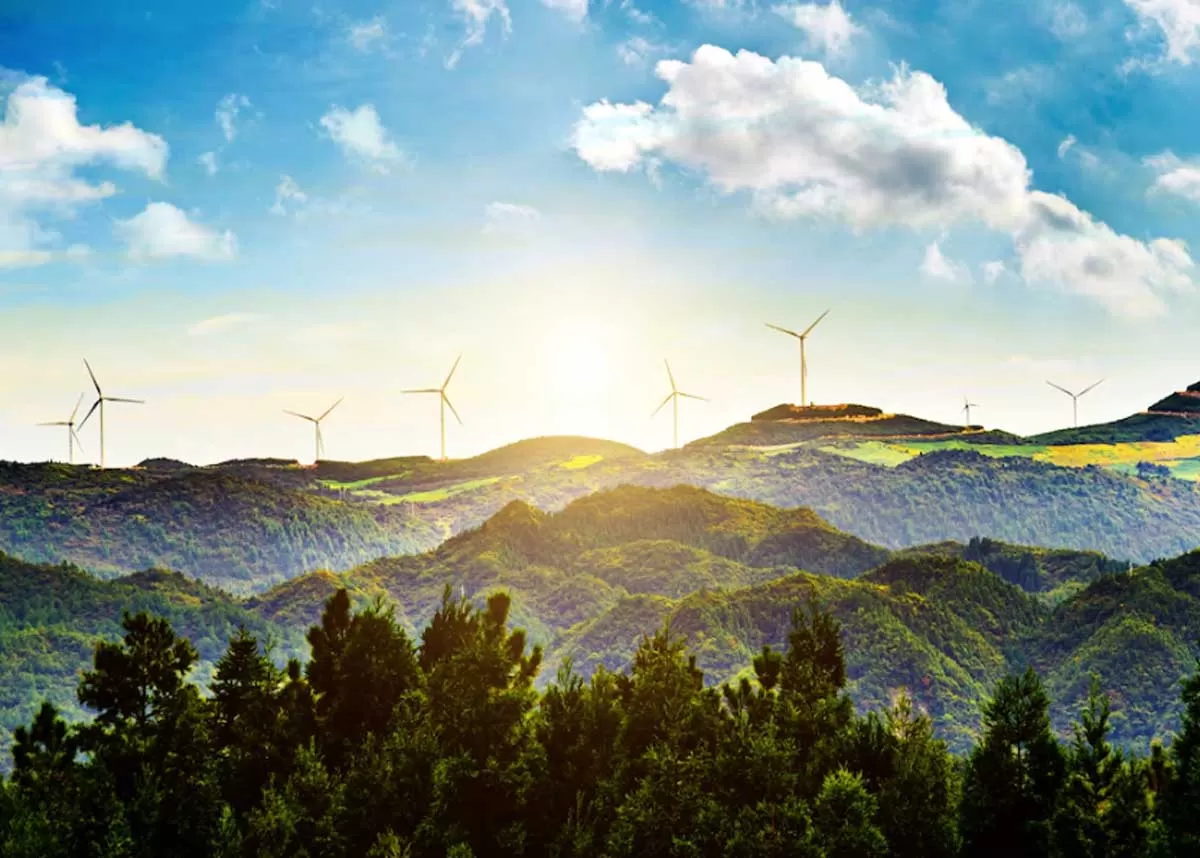
NTPC Green, NTPC Rise on Rs 960 Bn Clean Energy Plan in Chhattisgarh
NTPC and its subsidiary, NTPC Green Energy (NGEL), saw an upward trend in their share prices on Tuesday following the announcement of a substantial investment plan in Chhattisgarh’s clean energy sector. NTPC shares recovered from initial losses to gain nearly 0.2 per cent, while NGEL surged by approximately 1.5 per cent during intraday trading. The company formalised its commitment to renewable energy expansion by signing multiple agreements with the Chhattisgarh government at the Chhattisgarh Energy Investors Summit-2025, held in Raipur. The total investment is estimated at Rs 960 billion..