- Home
- Technology
- Advancing the use of Constructible BIM on different solutions throughout the construction phase will see the biggest impact
Advancing the use of Constructible BIM on different solutions throughout the construction phase will see the biggest impact
Trimble is a California based world's leading technology solutions company catering to industries such as agriculture, building and construction, geospatial, natural resources and utilities, governments, transportation and others. Trimble also does hardware development of Global Navigation Satellite System (GNSS) receivers, laser rangefinders, unmanned aerial vehicles (UAVs), inertial navigation systems and software processing tools. Trimble Buildings, a part of Trimble's Engineering and Construction segment, is focused on solutions that optimize the complete Design-Build-Operate (DBO) lifecycle of buildings. Trimble is dedicated to transforming the industry—increasing productivity, reducing waste and optimizing schedules, budgets and real estate portfolios—with powerful solutions that streamline communication and collaboration.
Paul Wallett is the Regional Director of Trimble Solutions India and Middle East. He took charge of the India business in late-2016, after a few years as the company’s Area Director for Middle East, based in Dubai. Wallett brings over 30 years of in-depth international and regional experience to his post, having worked in the software industry in the UK, the US and the Middle East. In his role of Regional Director for India and Middle East, Wallett is responsible for business operations and management of overall strategy for India and the UAE.
In an exclusive video interview hosted by CONSTRUCTION WORLD, Wallett discusses the digital transformation in the construction industry, the construction software market post COVID, and more...
Excerpts:
What are your thoughts on the digital transformation and how soon do we expect the construction industry to adapt to it?
The current trends show that construction market is on a steady road to growth. The ongoing COVID-19 pandemic has become a powerful catalyst for accelerated digitalization and automation inside most organizations. Businesses are now displaying a great agility and dynamism in responding to the ‘new normal’ of the lockdown economy, with the accompanying rise in remote working and restrictions on travel, by embracing digitalised processes and workflows. In the past few months, we have seen a marked increase in demand for different technologies and cloud-based solutions. There has been an increased adoption of modern construction technology and cloud based tools, which greatly aid in remote working and meet its deadlines while reducing cost and wastage, once projects resume. Our offerings, like SketchUp, Model Sharing solution along with cloud based platforms such as Trimble Connect, have seen a marked increase in demand, as they allow for greater collaboration across remote working environments. Additionally, there has been a huge increase in people using the data warehouses that we have, storing a lot of information.A recent report by McKinsey looking at similar type of metrics also showed that in the three months of lockdown, the industry has leaped forward in terms of five years in their adoption of technology. We have seen a 40-50% increase in adoption of solutions. The pandemic has created a golden opportunity for the industry to transform itself and embrace automation and digital workflows.
For the last 10 years Trimble has been working tirelessly towards the digital transformation of the industry. While everybody may be aware of what a Building Information Modelling (BIM) system provides, it is mostly the medium to large enterprises that have optimised the use of BIM. Many are yet to leverage BIM to its fullest potential, however with the digital transformation that is underway, the time is ripe for exploration.
Trimble has grown inorganically since 2012 through acquisitions including SketchUp, Tekla, Vico Office, GTeam, Sefaira, Viewpoint more recently. Is there an approach in marketing that identifies the gaps that your range needs to fulfil, which in turn prompts an ongoing inorganic action of this kind or can you share the vision that this spree is alluding to?
For many years, hardware was our primary offering. But we recognized that a change was underway and we could be a part of the digital revolution- a change that is driven by people. People are driving the change, the robots, the process, and managing the data in the best way possible. It has really benefited the organisation to look at key performing technologies in the construction industry and other aspects of the business, It is now evident that software is really the driver for the hardware solution.It is not just about going to site and doing a survey and then taking the data points back, it’s how we get the information in the machine with minimum or no data loss. one needs to offer the digital information in the beginning, and that's why we have things like SketchUp, parametric modelling solutions that sit on other solutions that are commonplace in the market as well as our proprietary software. Tekla structures is our construction solution tool and not an architect's platform. It is about building a highly accurate digital model at the outset and then developing processes where we can transfer that information digitally to the physical device which means you can transport that data right out into the job site.
ERP is another leading management software for projects, in terms of managing the overall project costs, scheduling and managing entire portfolio. These solutions are key to the whole construction process and lifecycle.
Mixed Reality is the new edge tech that alleviates errors, therefore wastage and promotes safety. Is there a quantification of losses on account of such errors that this technology helps guard against?
Tools like BIM have become limited to the engineering and design group. And hence creating information rich 3D models requires the workers to spend a lot of time and effort to gather the right information, while, making sure things do not clash because preventative measures are the best way forward in terms of alleviating errors on site. Ideally, creating a 3D model we should be able to quantum information the job site. Mixed reality devices that we have created really enable that bridge between the digital world and the physical world, which can greatly aid in streamlining the information gathering process.Trimble offers many solutions, chief among them being, site vision, which is Augmented Reality, that allows you, with a mobile phone and our app, and a connection to one of our positioning devices to position exactly where you are on site, and then, project through your device the designed model, construction, etc, out into the real world. This gives an immediate relationship between the designed model and the physical site and constraints that you are working with, and gets you going much faster in terms of downloading the information.
A great innovation in cutting edge tech that has the potential to help construction tech is the Trimble XR10 with HoloLens 2, which was launched in the Mobile World Congress in Barcelona last year. It is the first device created with the Microsoft HoloLens Customization Program and integrates the latest spatial computing technology into a certified solution for use with a hard hat for worker safety. With a wide field-of-view, improved usability and a unique, flip-up view screen, the Trimble XR10 with HoloLens 2 combines state-of-the-art mixed reality and safe operation in restricted access work areas. The full solution provides even greater accessibility to 3D models by front-line workers. Field-oriented workflows enable broad adoption of mixed-reality for jobsite activities to improve efficiency, productivity and quality of work.
Additionally, Trimble Connect, a cloud-based solution allows you to connect anywhere at any particular time; it enables people to go to site and they can use it in various scenarios, even pre-construction, during construction, or post construction maintenance. We can actually work from the office base itself, and have instructions send or collect information on and from the site.
What we can best do is avoid problems that could occur on site. So these mixed reality devices enable us to actually go to a pre-construction stage before some critical component is being delivered, and we can do a site survey and overlay in the real situation. There are also additional preventative measures that can be gauged that will save cost throughout the project.
Tell us about the partnership between Trimble, Hilti and Boston Dynamics.
What we saw with Boston Dynamics was a great opportunity to couple our robotic technology that we have. The X7, which is the combined total station and laser scanning device does self-registration on the site, it sells self-levelling as well. The trend we saw coming in is that a lot of people were doing bill validation laser scans. They would do a certain portion or phase of work and then do a laser scan to make sure what is as designed is as built. This allows the team to overlay that point cloud back into the house design model. This would be a repeated process over and over. And you can imagine that for a large project that could last two to three years you continually have to do laser scans or monitoring on site, it takes up a lot of time and also increases the risk of a person on that particular job. So, this relationship with Boston Dynamics enabled us to bring out our laser scanning X7, which is a robot in itself. It automates the process of doing laser scans. So the robots run around on-site and do laser scans and then stream the point cloud back into the field tablets that we have. So the people having to spend several hours on laser scanning are freed up to do other important tasks. It also lowers the risk level on site.
How do you view the BIM penetration in India as per evolution elsewhere in the world? Is the strengthening of specialty services like MEP, HVAC, fire safety, likely to accelerate this penetration?
We have seen a lot of local BIM service providers in India. What they typically are doing is working on behalf of big clients and on international projects; so for them, it is like a service industry. Speaking about what's happening domestically in India – that's the area that needs to be improved upon in terms of more local projects using the BIM technology. Obviously, when you are working on an international project, the rates they are getting paid is going to be much higher than the local. But what they need to see is that there is still a huge value in terms of cost saving on that project that you are doing domestically as well.There are quite a number of projects now that have adopted BIM in India, such as the Delhi Metro, Bangalore Airport, Statue of Unity, etc. And we are seeing more of it picking up in India, but not at the level we would hope for. With 35 million people working in the construction industry in India, I think there is a long way to go yet.
Another aspect is that we are used to utilizing BIM in the engineering and design phase. But when you then penetrate that out through the whole work process, and execute a job that was initiated in BIM, delivered and constructed in BIM, that's a big portion. So really, advancing the usage of BIM on these different solutions throughout the construction phase is where the biggest impact is going to come in terms of saving money and bringing value to the construction industry.
Post-COVID, what is your outlook for the construction and the construction software market in India? Also, what will adopting the new normal mean for the industry?
When we look at post-COVID, we are looking at risk factors. We now have to work in terms of social distancing on site and pre-emptive medical health checks for labors before they even get into the on-site situation. We have to focus on how we can utilise data to help improve that. Generally what’s going to happen is when you implement a new process, you will obviously have an impact on the schedule of the project in itself, there will be knock-on effects that are going to come. What we are seeing is that people are starting to really think about how we can manage our job sites a lot better. And, how we can put processes in place to enable our labor force to get onsite and manage social distancing as well. You need to deploy technologies that are going to actually do the work for you in terms of AI, machine learning, AI camera visuals, facial recognition cameras, etc.Beyond that, when we look at safety scenarios, using recognition technology and AI to ensure safety and manage where people are at any particular point in time on site. I think we will start to see a lot more interest in those types of solutions coming up.
In addition to this, we need to plan better, schedule better, and build schedules that detail the to-be downtime on the site. It is now possible to alleviate this at the pre-construction stage as well. We can also pre-construct and then assemble on site, so we need less people to put those structures together. It is all about the process of how you are designing buildings and putting them together. 3D printing is also a type of technology that people are starting to really become interested in. Then we have got type of materials whether it is precast or structural buildings, because they all are prefabricated prior to getting to the site and then the rapid erection takes place.
Assembling everything together after having done a detailed planning and analysis beforehand, will accelerate the processes. But we now have more variables of social distancing, health and hygiene that need to be incorporated in the planning and Trimble helps in the site management much better in terms of planning.
Hence, there are many different paths to that, like constructible BIM, which is transforming the industry and is efficiently helping in building a project. So having more information built in the model at the beginning to a higher level of development and details, whatever you designed digitally, you should be able to construct on site, so that is one aspect. And those errors are removed, it becomes easier to streamline and compress schedule. Technology needs to come out of the design engineering office to the entire construction phase. And you need to be carrying a 3D model on the job site as well and then integrating that with your positioning and hardware and mixed reality devices. And then you can start to really have a bigger impact on the schedule. And, the market is keen to be in a position where if they want to continue projects in the future, they need to really start thinking about digital investment.
Stay tuned for Construction World’s FREE webinars. View our complete webinar calendar and previous webinars here.
- BIM
- Video Interview
- Paul Wallett
- Trimble
- Trimble Solutions India and Middle East
- digital transformation
- COVID era
- COVID
- global construction software market
- construction software
- construction
- digital transformation
- COVID-19
- COVID-19 impact
- Global Navigation Satellite System
- GNSS
- cloud-based
- technologies
- cloud-based solutions
- Trimble Connect
- SketchUp
- McKinsey
- Building Information Modelling
- BIM
- SketchUp
- Tekla
- Vico Office
- GTeam
- Sefaira
- Constructible BIM
- Viewpoint
- Tekla structure
- construction solution
- management software
- project management
- construction sites
- Augmented Reality
- cloud-based solution
- post construction
- Trimble
- Hilti
- Boston Dynamics
- design model
- laser scanning
- BIM service providers
- BIM technology
- BIM in India
- Delhi Metro
- Bangalore Airport
- Statue of Unity
- engineering
- design phase
- Video Interview
- construction phase
- construction industry
- post-COVID
- AI
- machine learning
- 3D printing
- 3D model
- precast
According to a recent report, the global construction software market is expected to grow from US$ 1,601.57 million in 2019 to US$ 2,801.82 million by the end of 2025 at a CAGR of 9.76 per cent, despite economic slowdown that has overtaken the global economy. With the socio-economic impacts of this novel pandemic, the post COVID-19 era, will be defined by digitalization and automation. Trimble is a California based world's leading technology solutions company catering to industries such as agriculture, building and construction, geospatial, natural resources and utilities, governments, transportation and others. Trimble also does hardware development of Global Navigation Satellite System (GNSS) receivers, laser rangefinders, unmanned aerial vehicles (UAVs), inertial navigation systems and software processing tools. Trimble Buildings, a part of Trimble's Engineering and Construction segment, is focused on solutions that optimize the complete Design-Build-Operate (DBO) lifecycle of buildings. Trimble is dedicated to transforming the industry—increasing productivity, reducing waste and optimizing schedules, budgets and real estate portfolios—with powerful solutions that streamline communication and collaboration. Paul Wallett is the Regional Director of Trimble Solutions India and Middle East. He took charge of the India business in late-2016, after a few years as the company’s Area Director for Middle East, based in Dubai. Wallett brings over 30 years of in-depth international and regional experience to his post, having worked in the software industry in the UK, the US and the Middle East. In his role of Regional Director for India and Middle East, Wallett is responsible for business operations and management of overall strategy for India and the UAE. In an exclusive video interview hosted by CONSTRUCTION WORLD, Wallett discusses the digital transformation in the construction industry, the construction software market post COVID, and more... Excerpts: What are your thoughts on the digital transformation and how soon do we expect the construction industry to adapt to it? The current trends show that construction market is on a steady road to growth. The ongoing COVID-19 pandemic has become a powerful catalyst for accelerated digitalization and automation inside most organizations. Businesses are now displaying a great agility and dynamism in responding to the ‘new normal’ of the lockdown economy, with the accompanying rise in remote working and restrictions on travel, by embracing digitalised processes and workflows. In the past few months, we have seen a marked increase in demand for different technologies and cloud-based solutions. There has been an increased adoption of modern construction technology and cloud based tools, which greatly aid in remote working and meet its deadlines while reducing cost and wastage, once projects resume. Our offerings, like SketchUp, Model Sharing solution along with cloud based platforms such as Trimble Connect, have seen a marked increase in demand, as they allow for greater collaboration across remote working environments. Additionally, there has been a huge increase in people using the data warehouses that we have, storing a lot of information. A recent report by McKinsey looking at similar type of metrics also showed that in the three months of lockdown, the industry has leaped forward in terms of five years in their adoption of technology. We have seen a 40-50% increase in adoption of solutions. The pandemic has created a golden opportunity for the industry to transform itself and embrace automation and digital workflows. For the last 10 years Trimble has been working tirelessly towards the digital transformation of the industry. While everybody may be aware of what a Building Information Modelling (BIM) system provides, it is mostly the medium to large enterprises that have optimised the use of BIM. Many are yet to leverage BIM to its fullest potential, however with the digital transformation that is underway, the time is ripe for exploration. Trimble has grown inorganically since 2012 through acquisitions including SketchUp, Tekla, Vico Office, GTeam, Sefaira, Viewpoint more recently. Is there an approach in marketing that identifies the gaps that your range needs to fulfil, which in turn prompts an ongoing inorganic action of this kind or can you share the vision that this spree is alluding to? For many years, hardware was our primary offering. But we recognized that a change was underway and we could be a part of the digital revolution- a change that is driven by people. People are driving the change, the robots, the process, and managing the data in the best way possible. It has really benefited the organisation to look at key performing technologies in the construction industry and other aspects of the business, It is now evident that software is really the driver for the hardware solution. It is not just about going to site and doing a survey and then taking the data points back, it’s how we get the information in the machine with minimum or no data loss. one needs to offer the digital information in the beginning, and that's why we have things like SketchUp, parametric modelling solutions that sit on other solutions that are commonplace in the market as well as our proprietary software. Tekla structures is our construction solution tool and not an architect's platform. It is about building a highly accurate digital model at the outset and then developing processes where we can transfer that information digitally to the physical device which means you can transport that data right out into the job site. ERP is another leading management software for projects, in terms of managing the overall project costs, scheduling and managing entire portfolio. These solutions are key to the whole construction process and lifecycle. Mixed Reality is the new edge tech that alleviates errors, therefore wastage and promotes safety. Is there a quantification of losses on account of such errors that this technology helps guard against? Tools like BIM have become limited to the engineering and design group. And hence creating information rich 3D models requires the workers to spend a lot of time and effort to gather the right information, while, making sure things do not clash because preventative measures are the best way forward in terms of alleviating errors on site. Ideally, creating a 3D model we should be able to quantum information the job site. Mixed reality devices that we have created really enable that bridge between the digital world and the physical world, which can greatly aid in streamlining the information gathering process. Trimble offers many solutions, chief among them being, site vision, which is Augmented Reality, that allows you, with a mobile phone and our app, and a connection to one of our positioning devices to position exactly where you are on site, and then, project through your device the designed model, construction, etc, out into the real world. This gives an immediate relationship between the designed model and the physical site and constraints that you are working with, and gets you going much faster in terms of downloading the information. A great innovation in cutting edge tech that has the potential to help construction tech is the Trimble XR10 with HoloLens 2, which was launched in the Mobile World Congress in Barcelona last year. It is the first device created with the Microsoft HoloLens Customization Program and integrates the latest spatial computing technology into a certified solution for use with a hard hat for worker safety. With a wide field-of-view, improved usability and a unique, flip-up view screen, the Trimble XR10 with HoloLens 2 combines state-of-the-art mixed reality and safe operation in restricted access work areas. The full solution provides even greater accessibility to 3D models by front-line workers. Field-oriented workflows enable broad adoption of mixed-reality for jobsite activities to improve efficiency, productivity and quality of work. Additionally, Trimble Connect, a cloud-based solution allows you to connect anywhere at any particular time; it enables people to go to site and they can use it in various scenarios, even pre-construction, during construction, or post construction maintenance. We can actually work from the office base itself, and have instructions send or collect information on and from the site. What we can best do is avoid problems that could occur on site. So these mixed reality devices enable us to actually go to a pre-construction stage before some critical component is being delivered, and we can do a site survey and overlay in the real situation. There are also additional preventative measures that can be gauged that will save cost throughout the project. Tell us about the partnership between Trimble, Hilti and Boston Dynamics. What we saw with Boston Dynamics was a great opportunity to couple our robotic technology that we have. The X7, which is the combined total station and laser scanning device does self-registration on the site, it sells self-levelling as well. The trend we saw coming in is that a lot of people were doing bill validation laser scans. They would do a certain portion or phase of work and then do a laser scan to make sure what is as designed is as built. This allows the team to overlay that point cloud back into the house design model. This would be a repeated process over and over. And you can imagine that for a large project that could last two to three years you continually have to do laser scans or monitoring on site, it takes up a lot of time and also increases the risk of a person on that particular job. So, this relationship with Boston Dynamics enabled us to bring out our laser scanning X7, which is a robot in itself. It automates the process of doing laser scans. So the robots run around on-site and do laser scans and then stream the point cloud back into the field tablets that we have. So the people having to spend several hours on laser scanning are freed up to do other important tasks. It also lowers the risk level on site. How do you view the BIM penetration in India as per evolution elsewhere in the world? Is the strengthening of specialty services like MEP, HVAC, fire safety, likely to accelerate this penetration? We have seen a lot of local BIM service providers in India. What they typically are doing is working on behalf of big clients and on international projects; so for them, it is like a service industry. Speaking about what's happening domestically in India – that's the area that needs to be improved upon in terms of more local projects using the BIM technology. Obviously, when you are working on an international project, the rates they are getting paid is going to be much higher than the local. But what they need to see is that there is still a huge value in terms of cost saving on that project that you are doing domestically as well. There are quite a number of projects now that have adopted BIM in India, such as the Delhi Metro, Bangalore Airport, Statue of Unity, etc. And we are seeing more of it picking up in India, but not at the level we would hope for. With 35 million people working in the construction industry in India, I think there is a long way to go yet. Another aspect is that we are used to utilizing BIM in the engineering and design phase. But when you then penetrate that out through the whole work process, and execute a job that was initiated in BIM, delivered and constructed in BIM, that's a big portion. So really, advancing the usage of BIM on these different solutions throughout the construction phase is where the biggest impact is going to come in terms of saving money and bringing value to the construction industry. Post-COVID, what is your outlook for the construction and the construction software market in India? Also, what will adopting the new normal mean for the industry? When we look at post-COVID, we are looking at risk factors. We now have to work in terms of social distancing on site and pre-emptive medical health checks for labors before they even get into the on-site situation. We have to focus on how we can utilise data to help improve that. Generally what’s going to happen is when you implement a new process, you will obviously have an impact on the schedule of the project in itself, there will be knock-on effects that are going to come. What we are seeing is that people are starting to really think about how we can manage our job sites a lot better. And, how we can put processes in place to enable our labor force to get onsite and manage social distancing as well. You need to deploy technologies that are going to actually do the work for you in terms of AI, machine learning, AI camera visuals, facial recognition cameras, etc. Beyond that, when we look at safety scenarios, using recognition technology and AI to ensure safety and manage where people are at any particular point in time on site. I think we will start to see a lot more interest in those types of solutions coming up. In addition to this, we need to plan better, schedule better, and build schedules that detail the to-be downtime on the site. It is now possible to alleviate this at the pre-construction stage as well. We can also pre-construct and then assemble on site, so we need less people to put those structures together. It is all about the process of how you are designing buildings and putting them together. 3D printing is also a type of technology that people are starting to really become interested in. Then we have got type of materials whether it is precast or structural buildings, because they all are prefabricated prior to getting to the site and then the rapid erection takes place. Assembling everything together after having done a detailed planning and analysis beforehand, will accelerate the processes. But we now have more variables of social distancing, health and hygiene that need to be incorporated in the planning and Trimble helps in the site management much better in terms of planning. Hence, there are many different paths to that, like constructible BIM, which is transforming the industry and is efficiently helping in building a project. So having more information built in the model at the beginning to a higher level of development and details, whatever you designed digitally, you should be able to construct on site, so that is one aspect. And those errors are removed, it becomes easier to streamline and compress schedule. Technology needs to come out of the design engineering office to the entire construction phase. And you need to be carrying a 3D model on the job site as well and then integrating that with your positioning and hardware and mixed reality devices. And then you can start to really have a bigger impact on the schedule. And, the market is keen to be in a position where if they want to continue projects in the future, they need to really start thinking about digital investment. Watch the full video on what Paul Wallett has to say on digital transformation in construction and more... Stay tuned for Construction World’s FREE webinars. View our complete webinar calendar and previous webinars here.
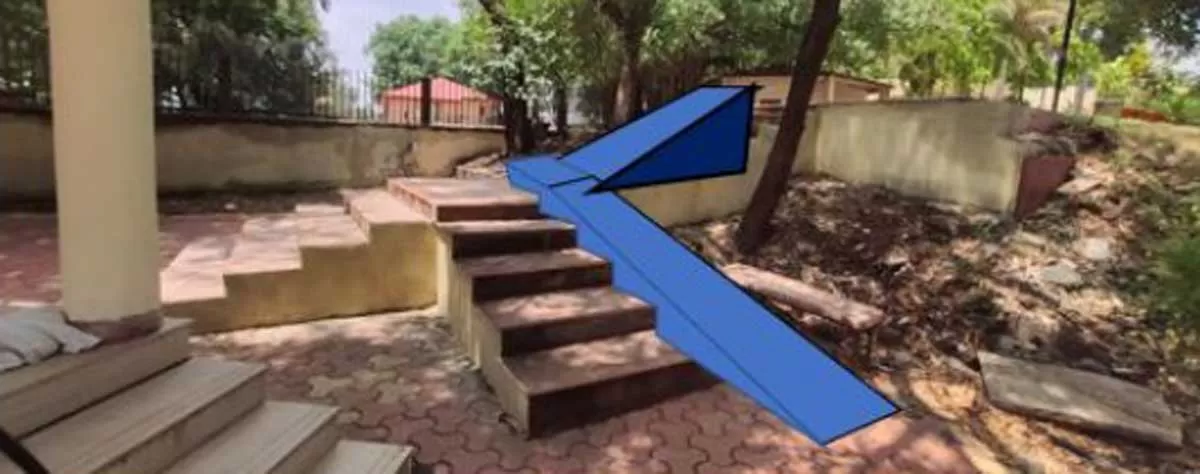
Madhya Pradesh Champions Inclusive Tourism at Heritage Sites
On the occasion of World Heritage Day, Madhya Pradesh is taking a significant step toward inclusive tourism by making its historical sites accessible to all — especially persons with disabilities. The state is rolling out its ‘Accessibility Infrastructure and Development’ project at Maheshwar, Mandu, Dhar, and Orchha, aiming to create a more welcoming experience at these iconic cultural destinations.The initiative, under the leadership of Chief Minister Dr Mohan Yadav and Tourism Minister Shri Dharmendra Bhav Singh Lodhi, includes infrastructure upgrades such as ramps, Braille signage, w..
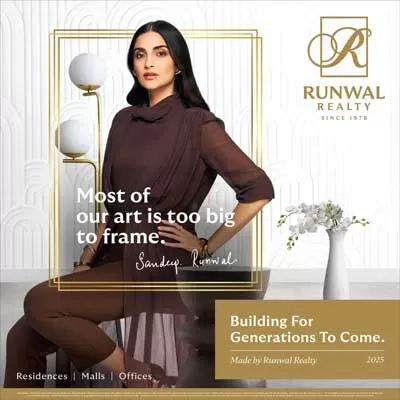
Runwal Realty Onboards Sonam Kapoor as Brand Ambassador
Real estate major Runwal has unveiled a refreshed identity as Runwal Realty, signalling a renewed commitment to crafting spaces that stand the test of time. With this refresh, the brand unveils its new philosophy: “Building for Generations to Come” and welcomes Bollywood star and global fashion icon Sonam Kapoor as its brand ambassador. This evolved identity reflects Runwal Realty’s commitment to creating not just homes, but heirlooms—crafted through visionary design, meticulous planning, global design expertise and an unwavering focus on quality. With the customer at its core, each de..
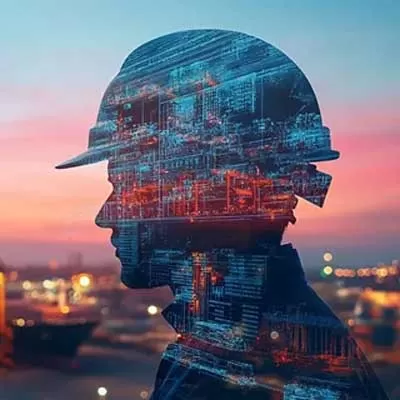
Emerging Trends in Infrastructure and Transport 2025: KPMG
KPMG’s latest report, The Great Reset: Emerging Trends in Infrastructure and Transport 2025 edition, sheds light on the profound changes transforming the global infrastructure landscape. As industries adapt to the challenges posed by climate change, economic pressures, and technological advancements, the report identifies key trends and provides actionable insights for leaders in infrastructure and transport sectors. “In today’s interconnected world, the lack of standardized supply chain practices is not just an operational challenge—it’s an environmental and economic one. We’..
Latest Updates
Recommended for you
Subscribe to Our Newsletter
Get daily newsletters around different themes from Construction world.
Advertisement
Advertisement
subscribe to the newsletter
Don't miss out on valuable insights and opportunities
to connect with like minded professionals