
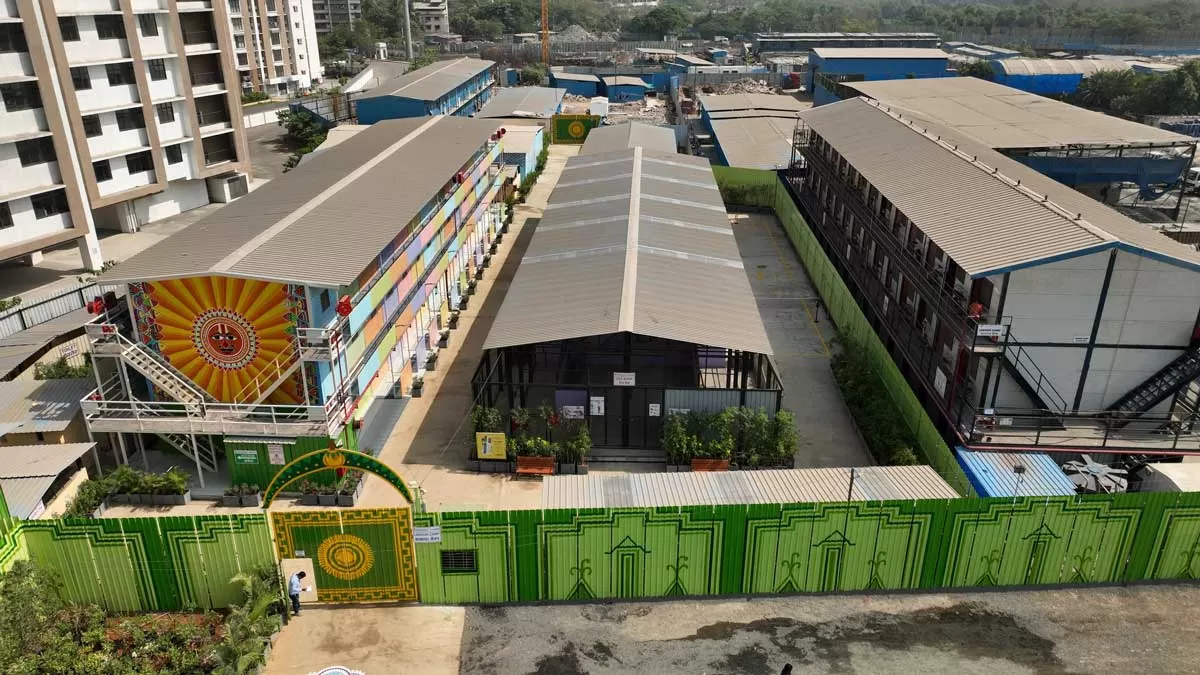
Rustomjee Builds Model Labour Housing in Thane
In a pioneering move that redefines worker welfare in Indian real estate, Rustomjee Group has unveiled a state-of-the-art 35,000 sq. ft. labour housing facility at the construction site of Rustomjee Urbania in Thane. The project sets a new industry benchmark by integrating comfort, safety, sustainability, and dignity into housing for 500 construction workers. Spread across 84 well-ventilated rooms, each 10x10 feet and accommodating up to six individuals, the facility offers far more than basic shelter. It represents a deeper cultural shift in how the construction workforce is valued—creatin..
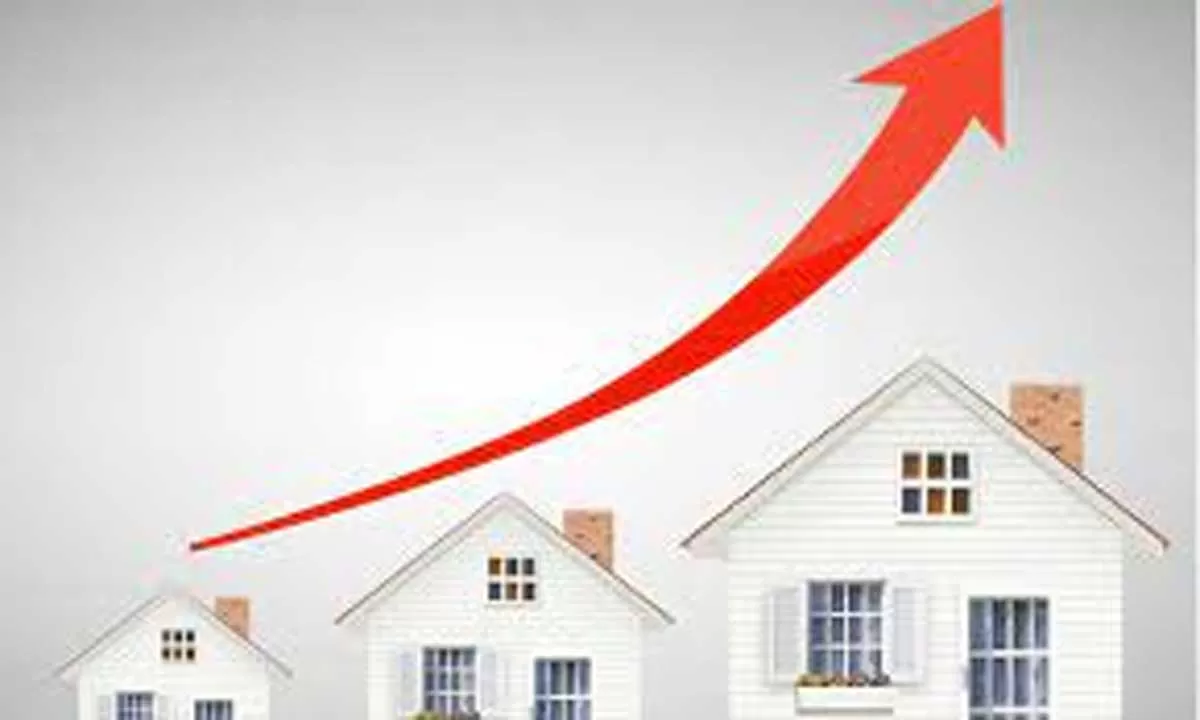
Young and Old Fuel India’s Housing Boom
India’s housing market is witnessing a surprising surge in interest from two distinct age groups—young professionals and senior citizens. A recent consumer sentiment survey of 1,950 prospective homebuyers reveals that both 18–24-year-olds and those aged 75 and above are showing strong intent to invest in real estate, highlighting a shift in how different generations are approaching property ownership. Young professionals, driven by rising incomes and a long-term view on wealth creation, recorded a Housing Sentiment Index (HSI) score of 164. Respondents from this group indicated they are..
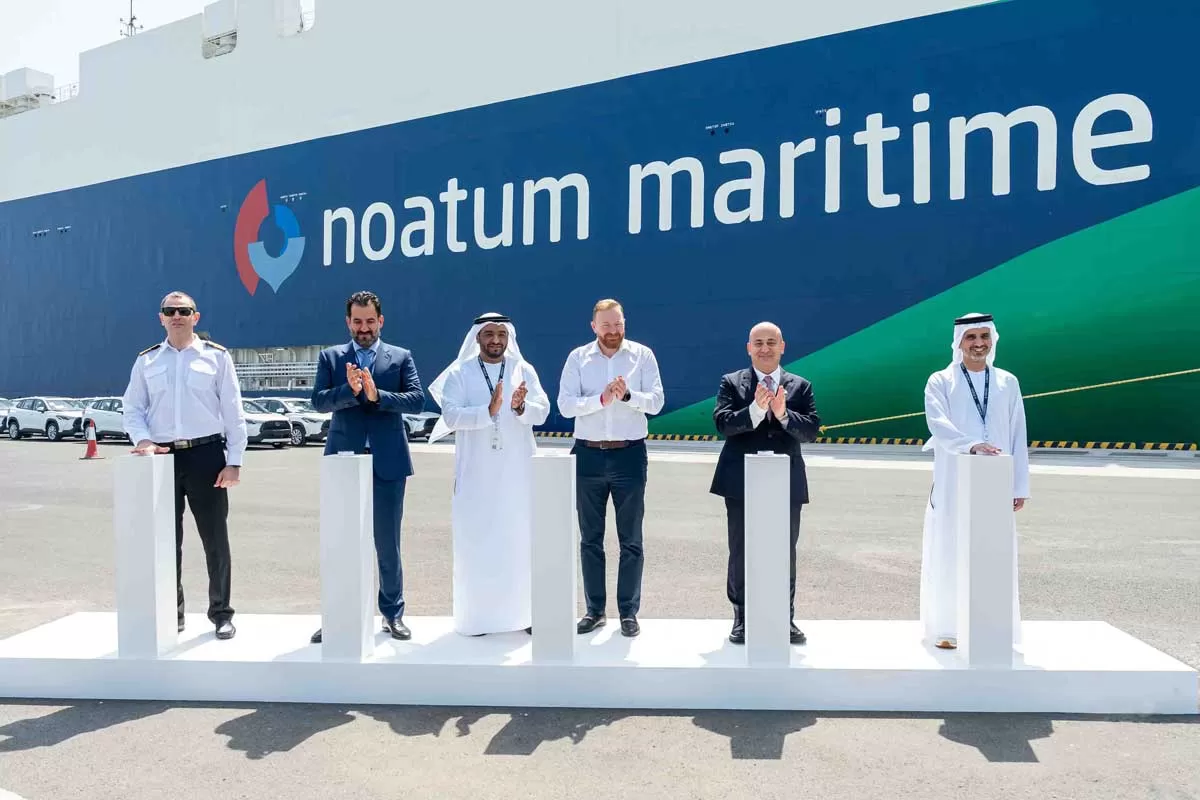
AD Ports’ LNG-Powered Ro-Ro Vessel Sets Sail from Khalifa Port
United Global Ro-Ro, a joint venture between Noatum Maritime (a part of AD Ports Group’s Maritime & Shipping Cluster) and Erkport, has marked a major milestone with the maiden voyage of its first LNG-powered Pure Car and Truck Carrier (PCTC), UGR Al Samha, at Khalifa Port. This event signifies a new chapter in sustainable maritime logistics, as the deep-sea vessel will serve as a green link across trade routes spanning the Middle East, Asia, and the Mediterranean. With a cargo capacity of over 7,000 car equivalent units (CEU) across 12 decks, UGR Al Samha has been designed to optimise the ..