Sustainability in focus for tiles, ceramics, sanitaryware
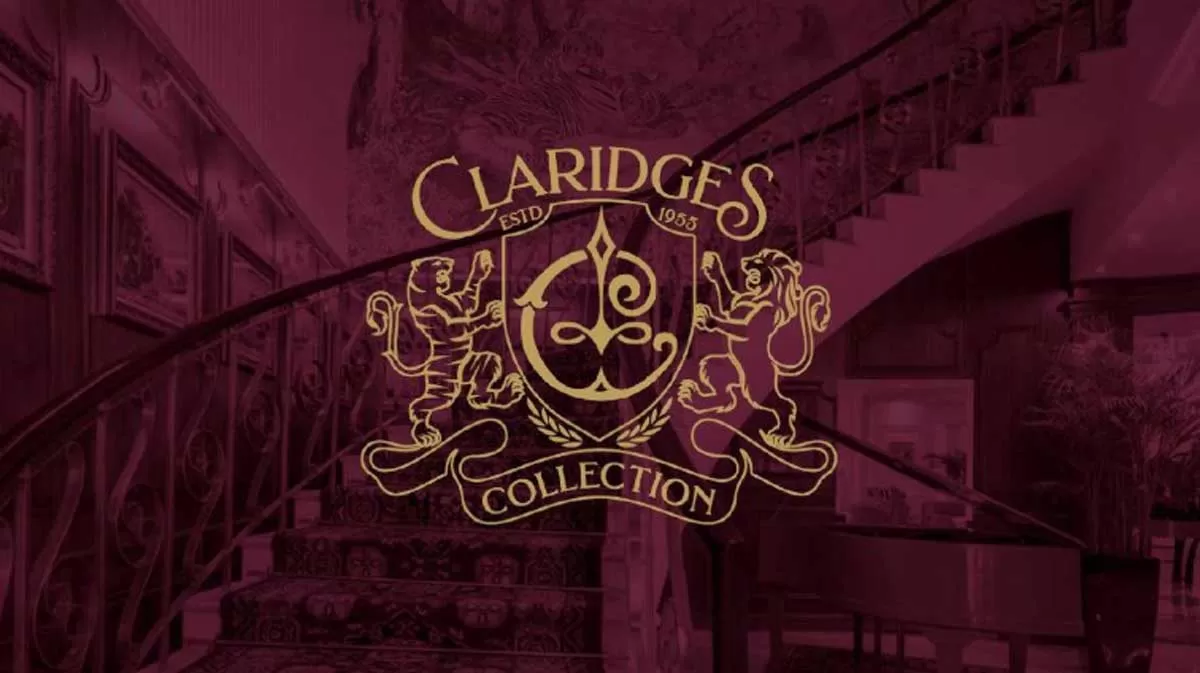
IHCL to bring Taj Palitana Palace to Gujarat
The Indian Hotels Company (IHCL) has signed the Palitana Palace in Gujarat under the Taj brand.Puneet Chhatwal, MD & CEO, IHCL, stated that Taj’s legacy in luxury hospitality aligns with this project, in partnership with His Highness Thakore Saheb Mandhatasinhji Jadeja of Rajkot. He highlighted Palitana’s potential for spiritual tourism and social events.The 65-key Taj Palitana will be extensively restored, featuring a blend of heritage and modern luxury. It will offer fine dining, a spa, a pool, and a 3,000 sq. ft. ballroom for events. The property will also showcase royal art and..
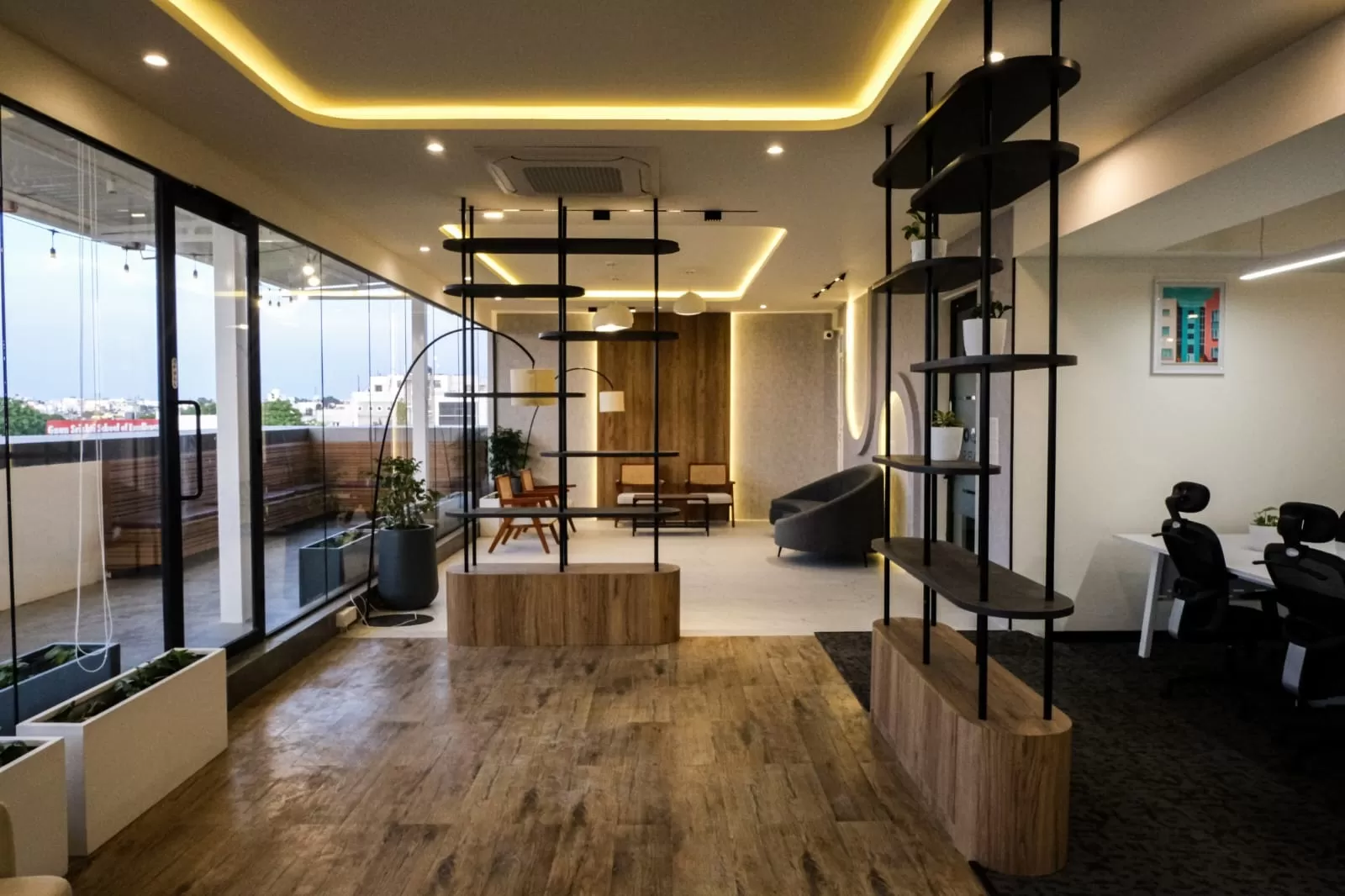
Urban Vault enters Pune with 35,000 sq. ft. flex space in Baner
Urban Vault has launched its first Pune workspace at Ambrosia Galaxy, Baner High Street, marking its expansion into the city’s growing flex space market.The 35,000 sq. ft. facility offers 700 seats with per-seat pricing between Rs 6,500 and Rs 8,000. Designed for enterprises, startups, and SMEs, the space aims to provide flexible, scalable, and cost-effective office solutions.Co-founder and CEO Amal Mishra highlighted Pune’s rising demand for managed workspaces and Urban Vault’s focus on delivering high-quality, adaptable environments.The company plans further expansion in Pune, targetin..
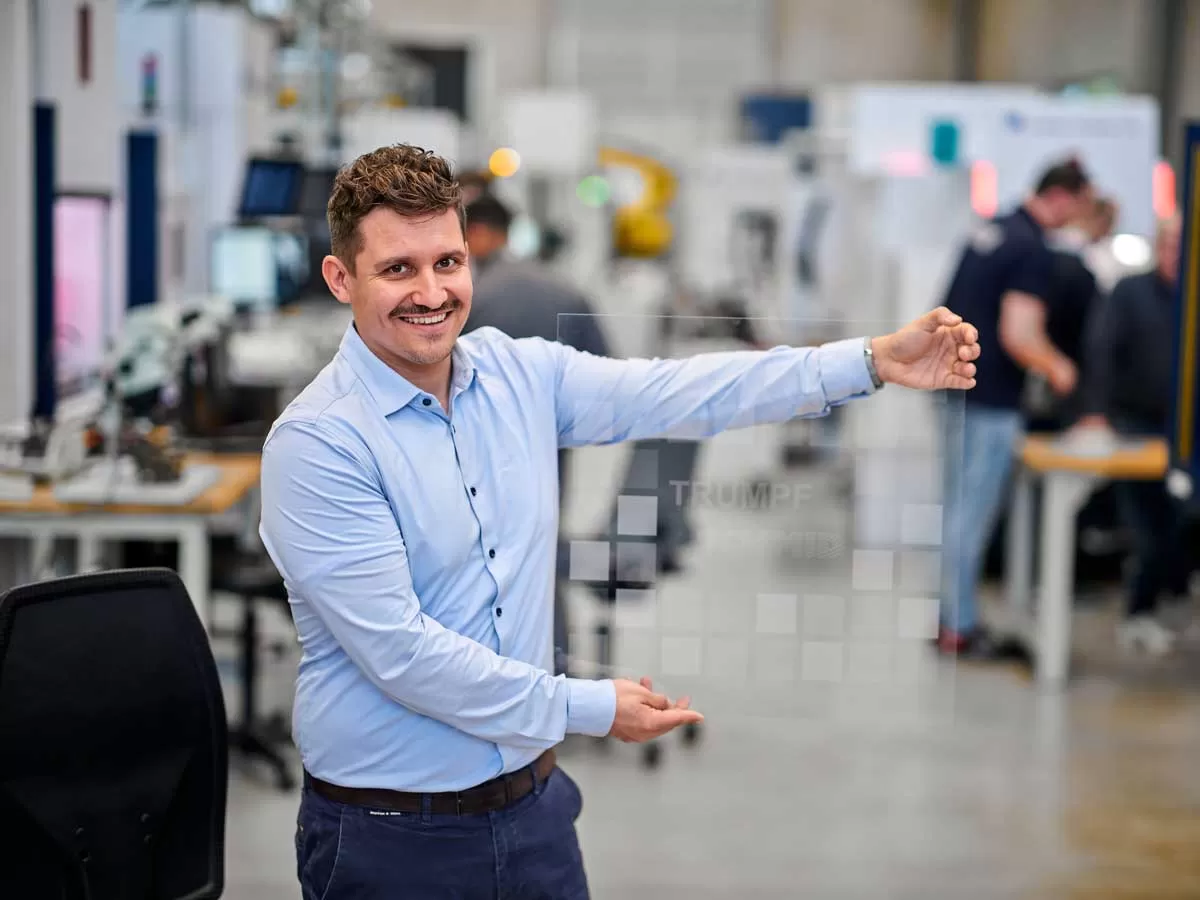
TRUMPF, SCHMID enable cost-effective microchip production
TRUMPF and SCHMID Group have developed an innovative manufacturing process that replaces silicon with glass in advanced microchip packaging, reducing costs and boosting efficiency.This breakthrough process, aimed at high-end chips for AI, smartphones, and smartwatches, enables manufacturers to use glass interposers instead of silicon, significantly lowering production costs.TRUMPF’s laser technology, combined with SCHMID’s etching expertise, ensures precise through-glass vias (TGVs), a key requirement in chip production. Their approach accelerates process times tenfold, allowing millions o..