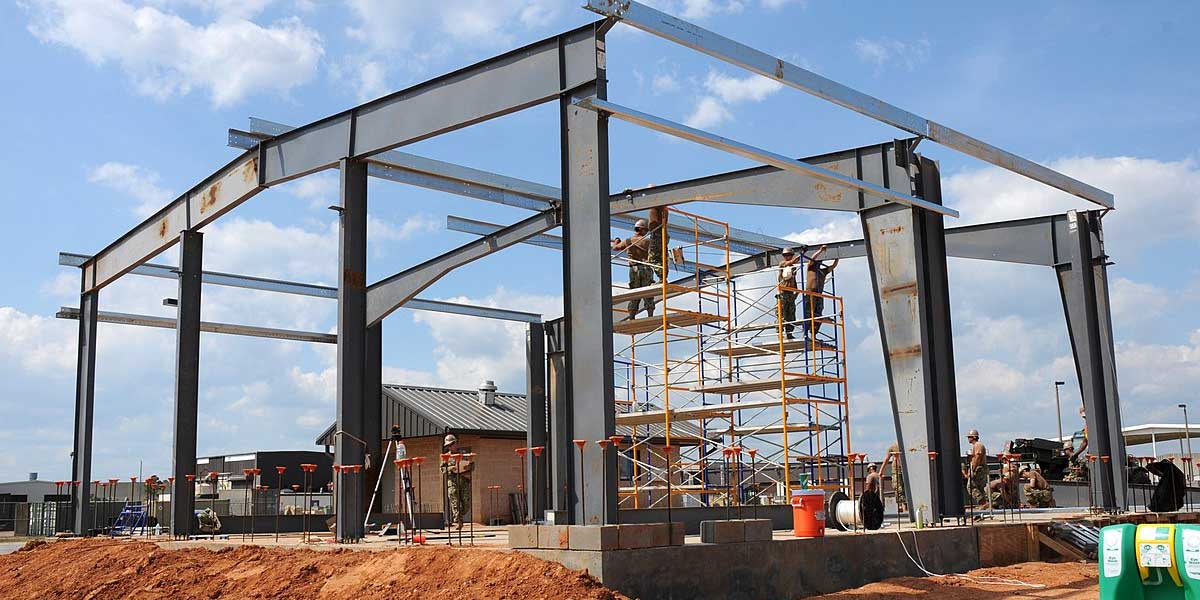
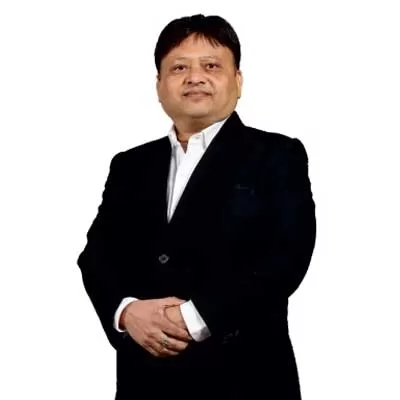
Thermocool Home Appliances Invests Rs 300 million in New Ghaziabad Plant
Thermocool Home Appliances, a leading UP-based home and kitchen appliances brand, has inaugurated a new manufacturing facility in Ghaziabad, reinforcing its growth, innovation, and sustainability commitments.Spanning 25,000 square meters, the plant features advanced automation, energy-efficient systems, and employee welfare facilities. With an initial production capacity of 1,800-2,200 units/day, the company plans to scale up to 3,000-4,000 units/day within six months and expand the facility by 50 percent over the next two years.The Rs 300 million investment will cater to rising demand across ..
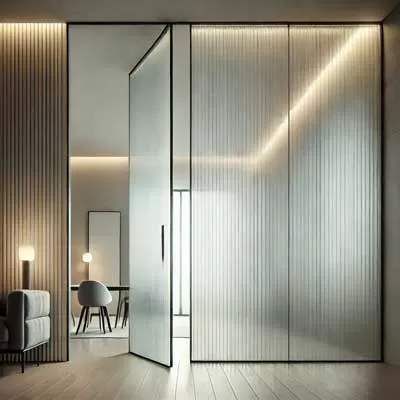
Parallel debuts fluted glass collection, redefining luxury interiors
Parallel has launched an exquisite collection of tinted, extra-clear, and designer fluted glass, introducing a new dimension to contemporary interiors.Fluted glass, known for its vertical striations, diffuses light while sculpting silhouettes with a refined aesthetic. Parallel’s range includes smoky tinted variants, pristine extra-clear options, and metallic-infused designs, ideal for partitions, doors, and wall treatments that balance exclusivity with openness.Emphasising sensory design, the collection enhances spaces by creating dynamic light interactions. Crafted for luxury residences, ho..
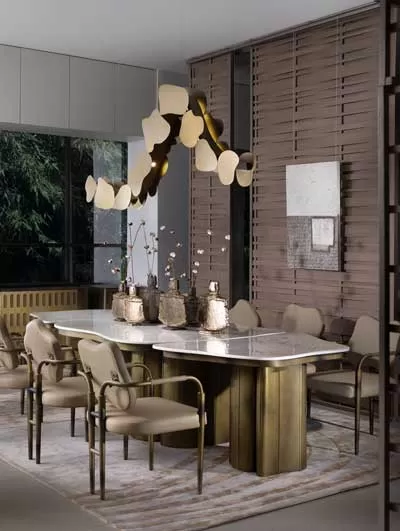
Nivasa unveils luxury lighting collection blending artistry and innovation
Nivasa, a leader in luxury furniture design, has launched an exquisite lighting collection inspired by nature, combining sculptural aesthetics with masterful craftsmanship.Crafted from premium 304-grade stainless steel, each piece showcases a refined interplay of organic and sleek forms, offering a range of finishes for bespoke customization. Designed for grand foyers, intimate spaces, and sophisticated interiors, the collection merges contemporary finesse with global design standards.Collection highlights include:Circular Drummer’s Chandelier – A geometric yet fluid design in a light gold..