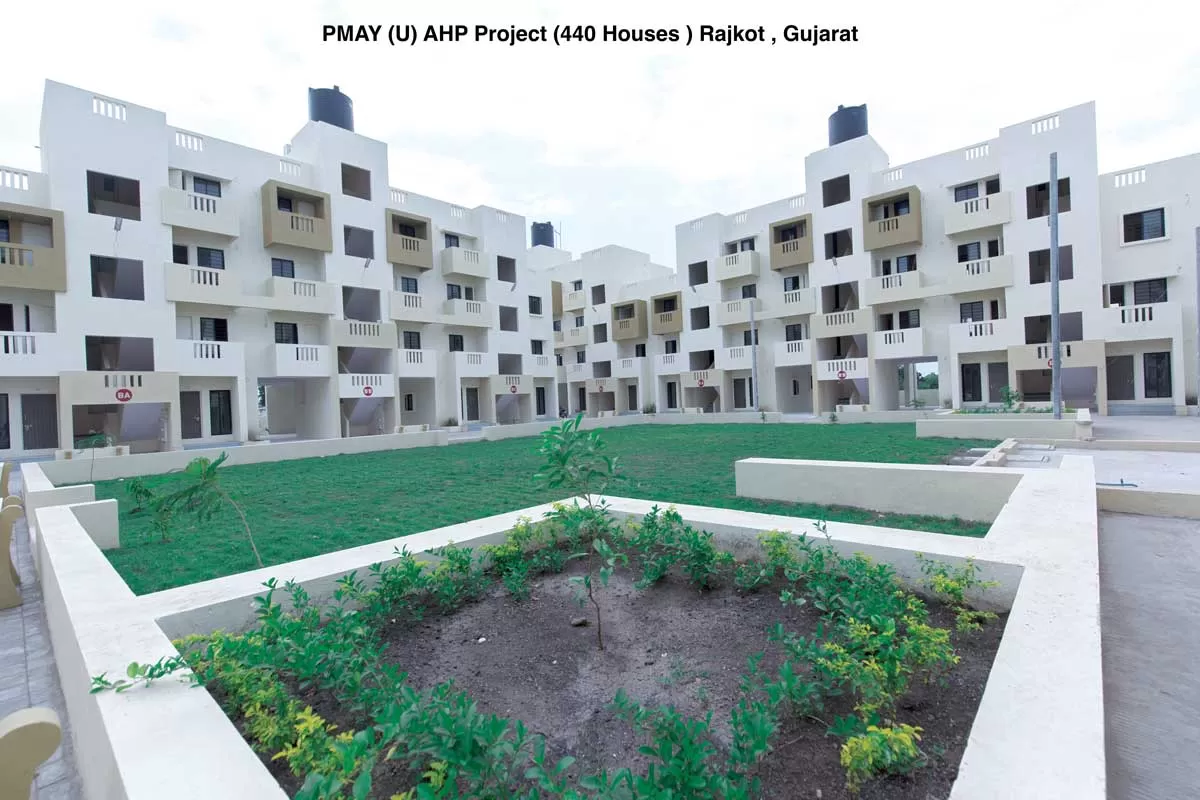
Rethinking Slum Development
In July 2024, the Supreme Court directed the Bombay High Court to initiate suo motu proceedings to evaluate the implementation of the Maharashtra Slum Area (Improvement, Clearance and Redevelopment) Act.During the ensuing proceedings, the Division Bench of Justices expressed concern about the plight of slum dwellers, saying, “Merely because you are a slum dweller doesn’t mean that you are left to the discretion of developers. They end up with a pittance.” The Bench also noted that the buildings allocated to slum dwellers were akin to “vertical slums”. “The buildings are congested. ..
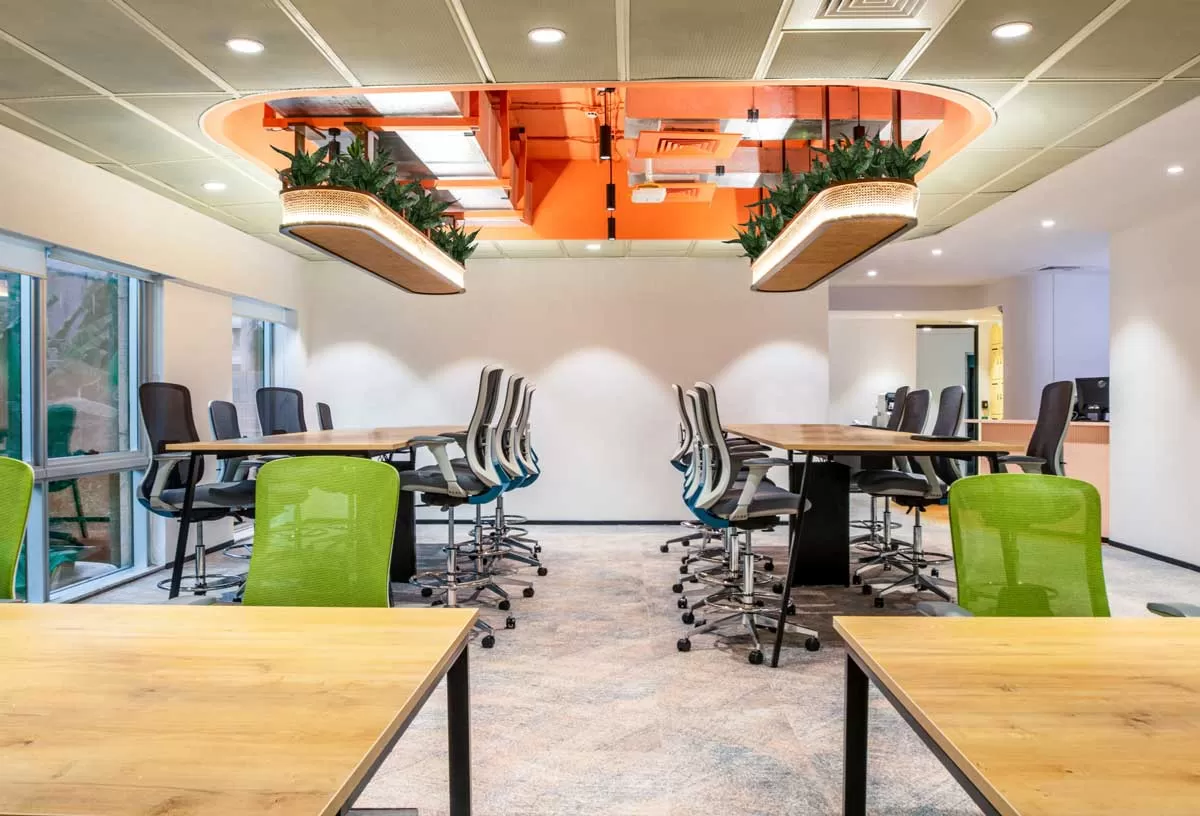
Ring in the New!
Lighting:OLED (organic light emitting diode) panels such as those by Philips are the latest option in soft lighting fixtures that can be embedded into walls, ceilings or furniture, says Nilesh Sawant, Principal Architect, Nilesh Sawant Architect. “Being thin and flexible, they lend themselves well to different applications while delivering the energy-efficiency associated with LED technology.”And Sapna Aggarwal, Founder, ANSA Architecture & Interiors, says “Embedded light-emitting diodes can create a dreamy illumination, while dimmable LEDs are useful for allowing..
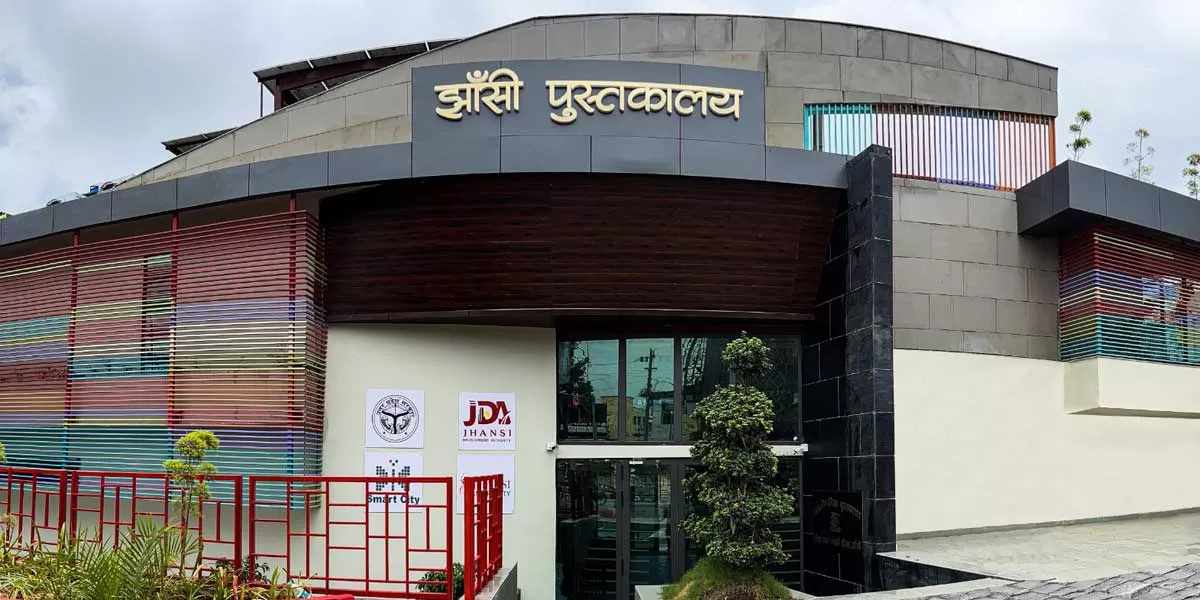
Jhansi Library
The Jhansi Library, commissioned by the Jhansi Development Authority (JDA) under the Jhansi Smart City initiative and built by Bootes Impex, a net-zero construction-tech company. It is the first library in Asia to achieve EDGE (Excellence in Design for Greater Efficiencies) certification from the International Finance Corporation (IFC), a member of the World Bank Group. This milestone marks the library as India’s first and only net-zero library, aligning with India’s Net-Zero Vision 2070.Sustainable designDeepak Rai, Managing Director, Bootes Impex, explains, “The project's vision ..