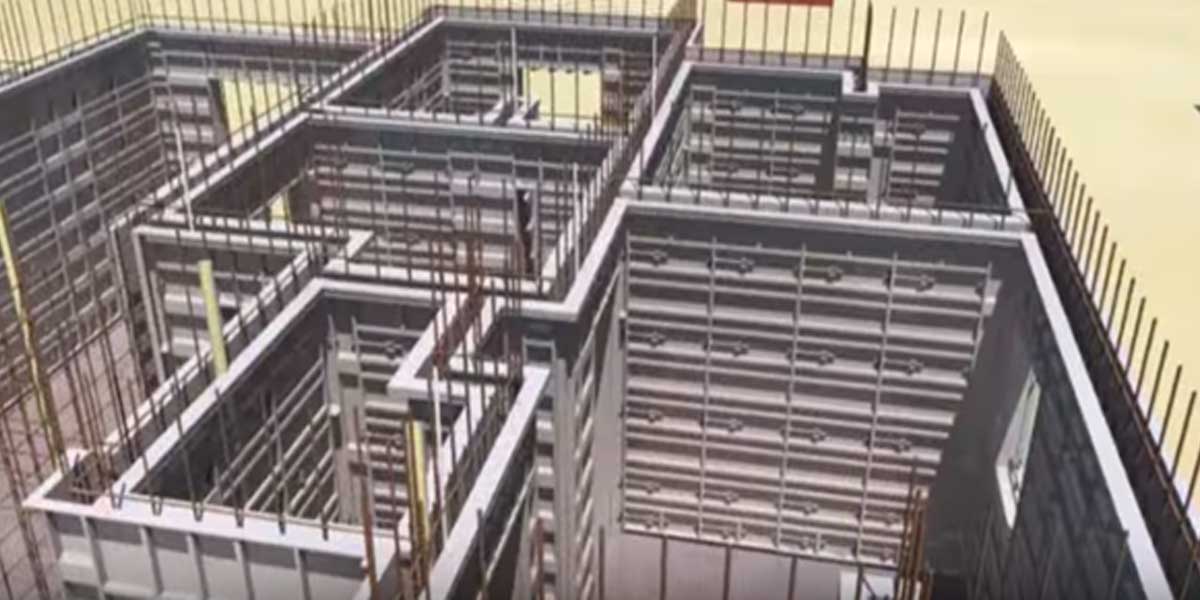
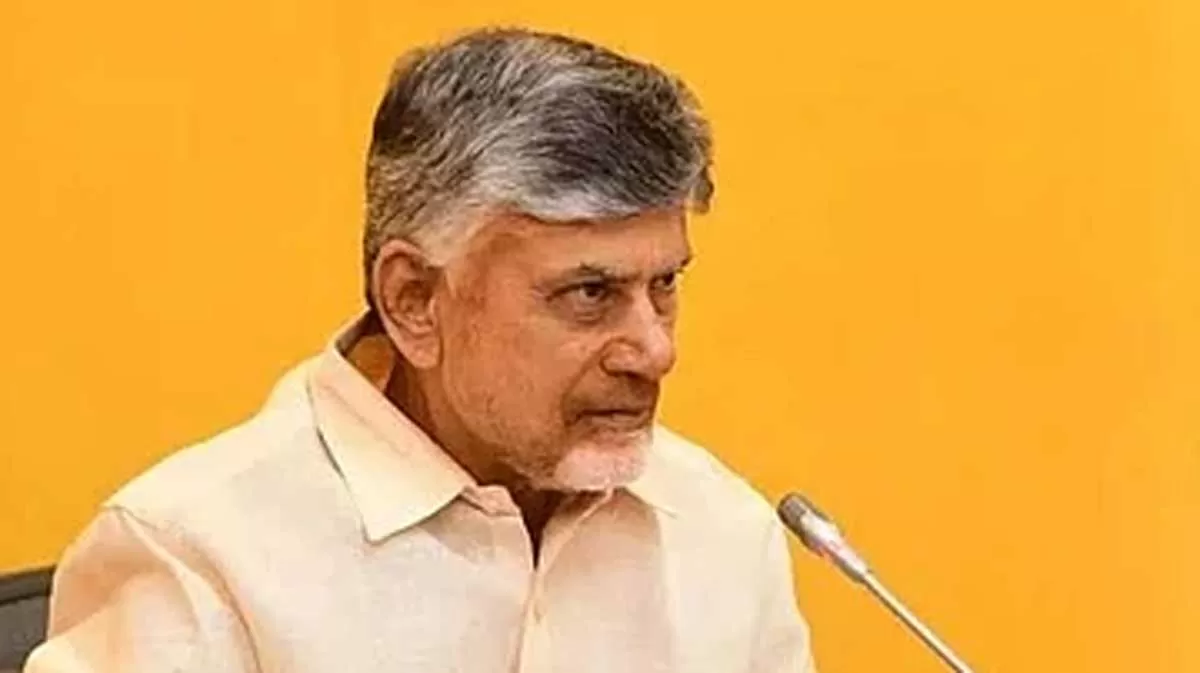
Naidu Seeks Rs 563 Crore For AP Sports Infrastructure
Andhra Pradesh Chief Minister N Chandrababu Naidu has sought Rs 563 crore from the Centre to boost sports infrastructure in the state, including Rs 538 crore for stadium development and Rs 25 crore to host the Khelo India Martial Arts Games 2025. Naidu made the request during a meeting with Union Youth Services and Sports Minister Mansukh Mandaviya in New Delhi on Wednesday.The CM urged early completion of Khelo India infrastructure projects in Tirupati, Rajahmundry, Kakinada, and Narasaraopeta, and called for an international-standard badminton training centre and a national aquatic sports hu..
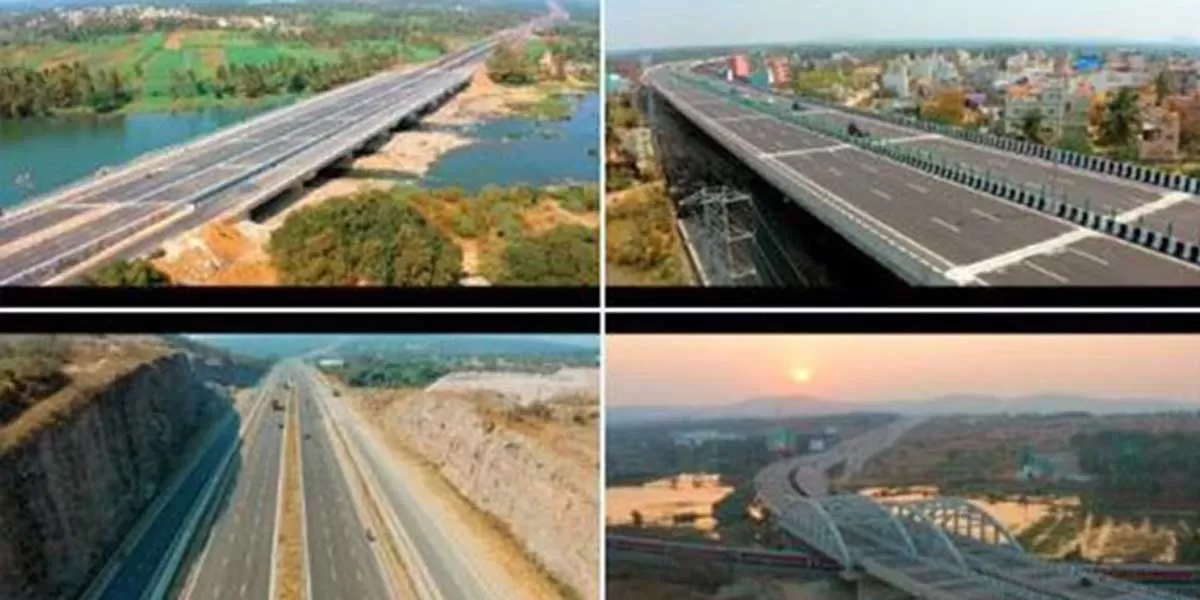
Tough Bidding Norms Slow NHAI Road Project Awards
Stringent bidding rules imposed by the Ministry of Road Transport & Highways (MoRTH) have led to a slowdown in project awards by the National Highways Authority of India (NHAI), despite a robust Rs 3.5 trillion pipeline. According to an HDFC Securities report, the shift to more cautious developer models now favours firms with strong balance sheets, as tighter qualification norms limit aggressive bidders.The revised norms mandate additional performance security, targeting the exclusion of players that previously submitted low bids—often 25 to 40 per cent below NHAI cost estimates—raisin..
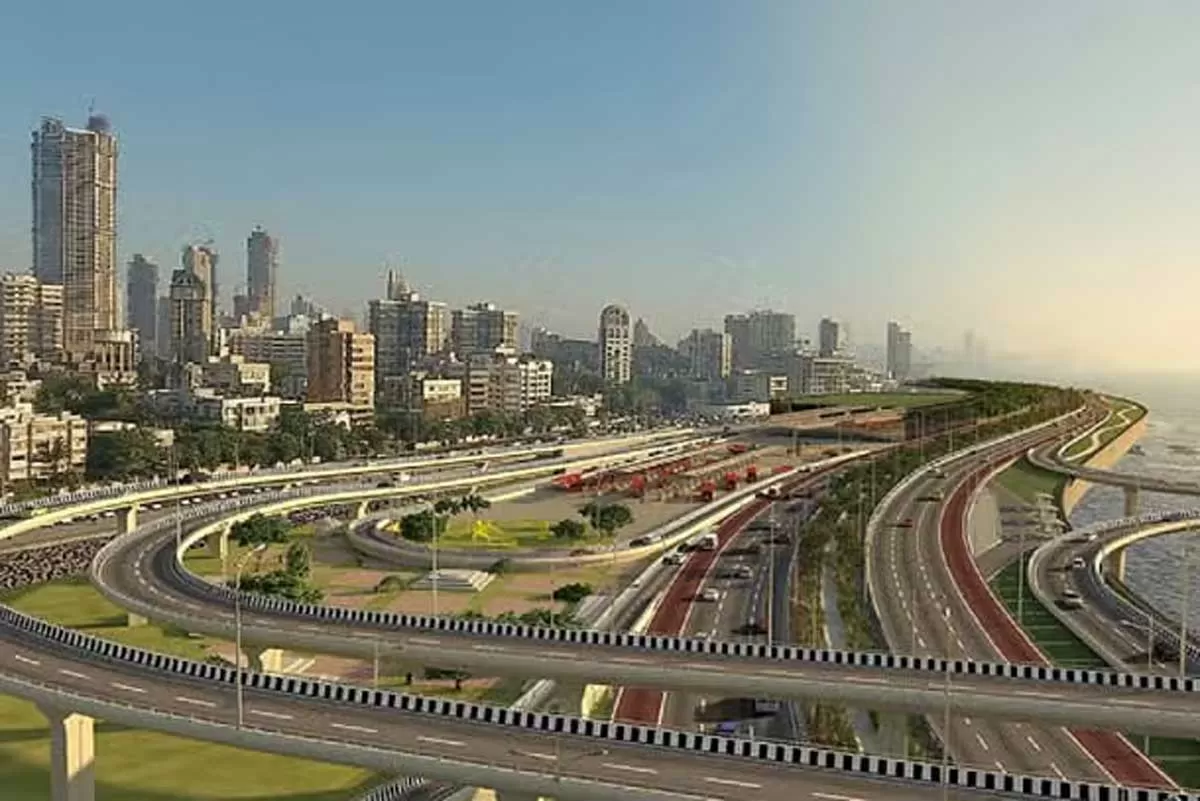
Mumbai Gets Coastal Nod for Next Promenade Phase
As Mumbai prepares to open two major sections of its expansive seafront promenade this week, the city’s civic authority has secured a key coastal clearance to advance further construction. The Maharashtra Coastal Zone Management Authority (MCZMA) has approved the commencement of work on the segment between Haji Ali and Baroda Palace, with tendering expected soon after project cost assessments.The promenade, stretching 7.5 km in length and 20 metres wide, is being designed as a flagship open space for walkers, joggers, and cyclists. Two critical stretches—2.75 km from Tata Garden to Haji Al..