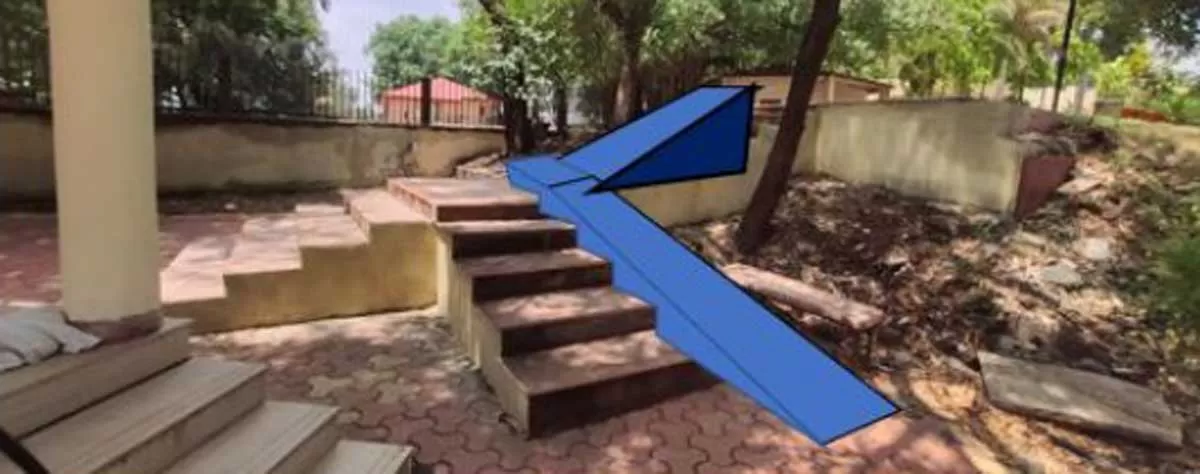
Madhya Pradesh Champions Inclusive Tourism at Heritage Sites
On the occasion of World Heritage Day, Madhya Pradesh is taking a significant step toward inclusive tourism by making its historical sites accessible to all — especially persons with disabilities. The state is rolling out its ‘Accessibility Infrastructure and Development’ project at Maheshwar, Mandu, Dhar, and Orchha, aiming to create a more welcoming experience at these iconic cultural destinations.The initiative, under the leadership of Chief Minister Dr Mohan Yadav and Tourism Minister Shri Dharmendra Bhav Singh Lodhi, includes infrastructure upgrades such as ramps, Braille signage, w..
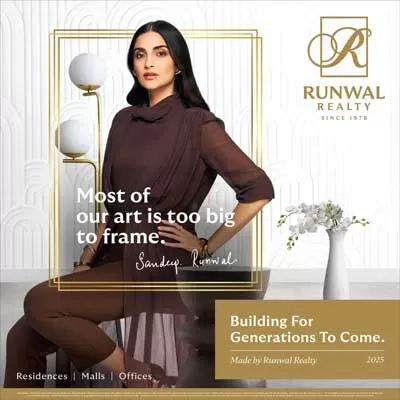
Runwal Realty Onboards Sonam Kapoor as Brand Ambassador
Real estate major Runwal has unveiled a refreshed identity as Runwal Realty, signalling a renewed commitment to crafting spaces that stand the test of time. With this refresh, the brand unveils its new philosophy: “Building for Generations to Come” and welcomes Bollywood star and global fashion icon Sonam Kapoor as its brand ambassador. This evolved identity reflects Runwal Realty’s commitment to creating not just homes, but heirlooms—crafted through visionary design, meticulous planning, global design expertise and an unwavering focus on quality. With the customer at its core, each de..
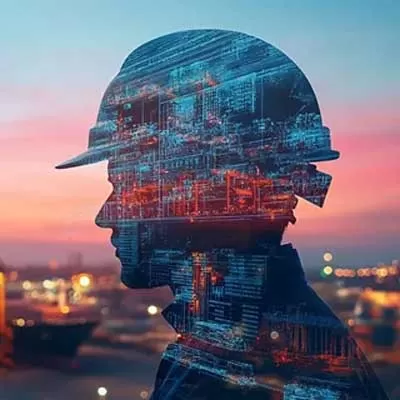
Emerging Trends in Infrastructure and Transport 2025: KPMG
KPMG’s latest report, The Great Reset: Emerging Trends in Infrastructure and Transport 2025 edition, sheds light on the profound changes transforming the global infrastructure landscape. As industries adapt to the challenges posed by climate change, economic pressures, and technological advancements, the report identifies key trends and provides actionable insights for leaders in infrastructure and transport sectors. “In today’s interconnected world, the lack of standardized supply chain practices is not just an operational challenge—it’s an environmental and economic one. We’..