The design-build model is best suited for the affordable housing programme
Redefine the future of urban mobility! Join us at the Metro Rail Conference 2025 to explore groundbreaking ideas and insights. 👉 Register today!
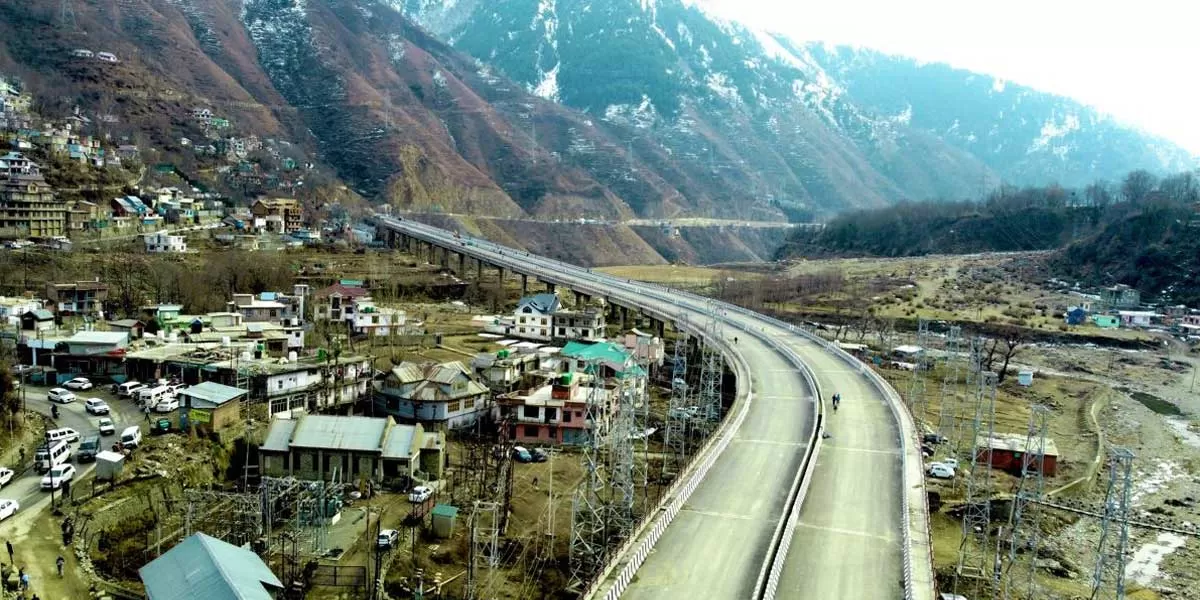
Banihal Bypass Started, Milestone Achieved By NHAI On NH44
The National Highways Authority of India (NHAI) has achieved another milestone on the Jammu-Srinagar four-lane highway after nearly four years of construction. The NHAI has completed the Banihal Bypass, and one side of the bypass was opened for traffic following a post by Union Minister for Road Transport and highways Nitin Gadkari on his official X handle. Traffic has been allowed from Jammu to Srinagar on one tube of the much awaited Banihal bypass.Project head of Banihal bypass from NHAI Kumar Jainendra told Greater Kashmir that the full public cooperation and support from locals was u..

Hyderabad: Rs 70 Bn Sanctioned For Road Infra Works
As part of the Hyderabad City Innovative and Transformative Infrastructure (H-CITI) program the state government sanctioned Rs 70 billion for 38 works, including the construction of flyovers, underpasses, and road-over-bridges (ROB) to ease the traffic in various parts of Hyderabad and its nearby municipalities. As part of the Strategic Road Development Programme (SRDP) initiated by the previous BRS government, several flyovers and road infrastructure projects were taken up mostly under the limits of the Greater Hyderabad Municipal Corporation (GHMC). Out of the 42 works under SRDP, 36 projec..
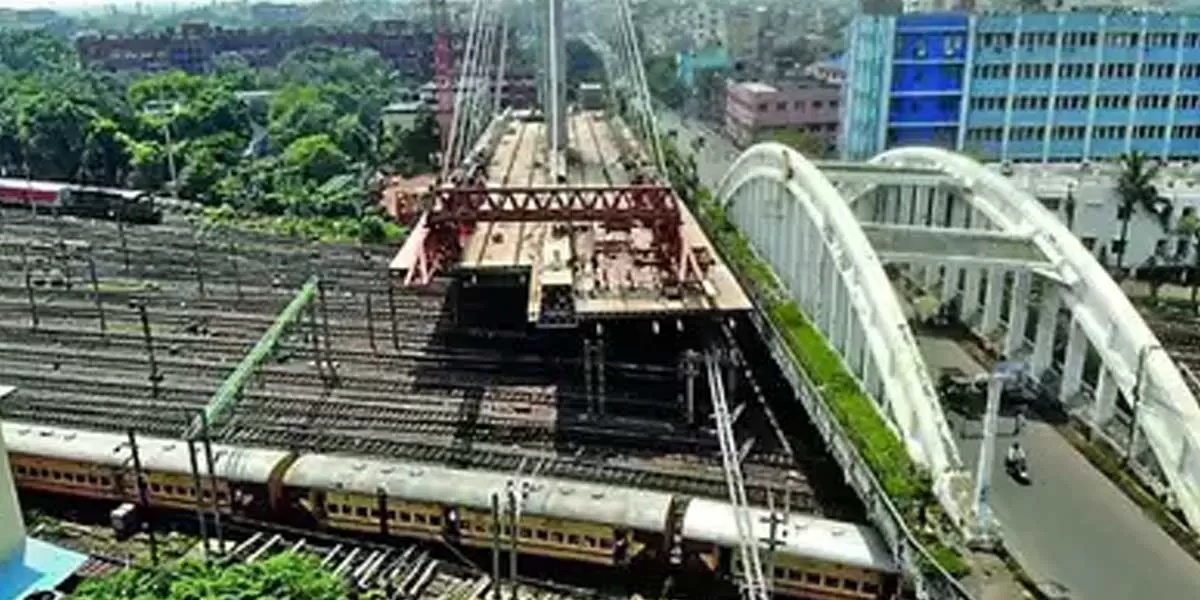
India's Second Cable-Stayed Bridge to Be Built In Howrah
Eastern Railways is set to construct India’s second cable-stayed steel deck bridge in Howrah, aimed at easing traffic congestion on the Howrah Bridge. The new bridge will span the existing GT Road route, linking Howrah Station with the Howrah Bridge. The new structure is a response to the rising volume of vehicular traffic, which has been placing significant strain on the 75-year-old Howrah Bridge, leading to regular traffic jams and delays.The new cable-stayed bridge will feature a four-lane design and will measure 134 m in length, an expansion from the existing 60 meters of the Chandmari B..