RHEWUM has developed a solution to process sand mobile and therefore directly on site.
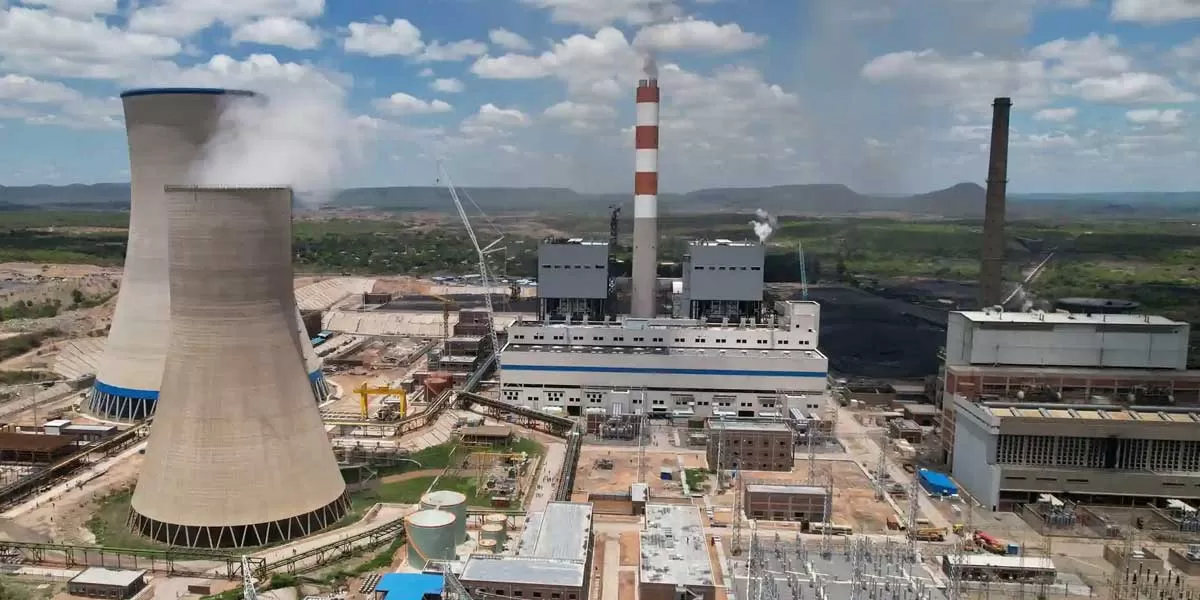
Centre suggests states to list power firms
Power Minister Manohar Lal urged states and union territories to consider listing their power generation, transmission, and distribution companies on stock exchanges to attract investment and improve operational efficiency. Addressing the media, after a conference of power ministers, Lal highlighted the need for increased capital inflows to meet India’s rising power demand, which has placed added strain on the sector. “With the growing power demand, there is a growing need for investment in the sector and improving operational efficiencies. States may identify and take up utilities for lis..
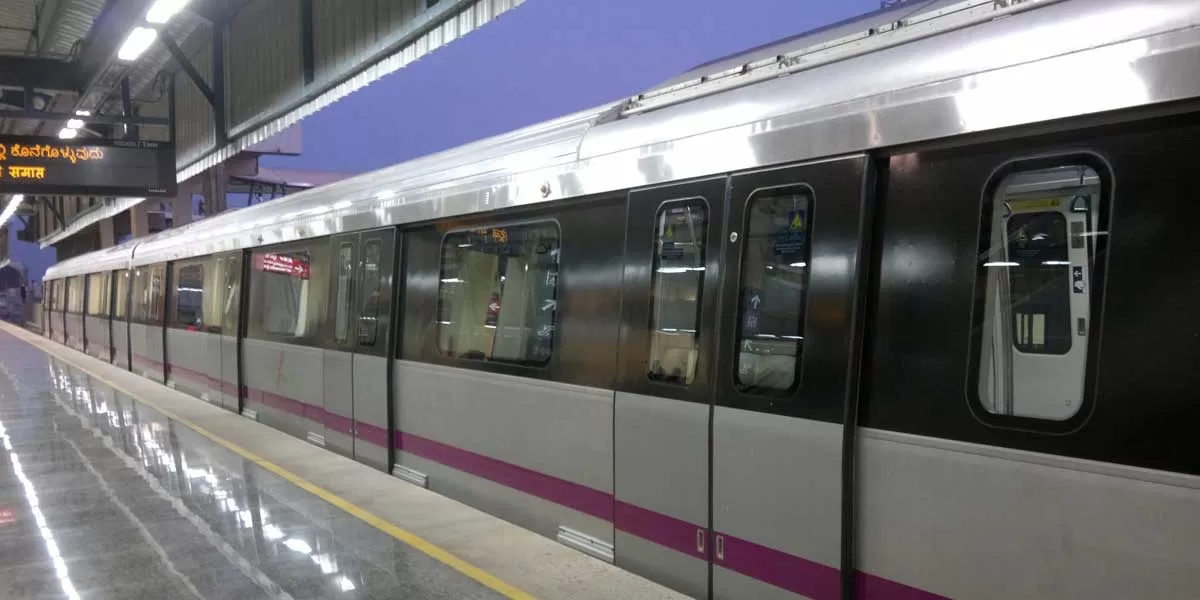
Metro on backburner as Tricity set to get new e-buses circuit
To boost connectivity for the commuters of the Tricity, a new circuit-cum-network of electric buses (e-buses) is all set to come up that will cover Chandigarh, Panchkula, and Mohali. The move comes days after Union Minister for Housing and Urban Affairs Manohar Lal Khattar said that in Chandigarh the ridership is not according to the criteria set for operating a Metro. He had also said that the option of a pod taxi can also be explored as it will not impact the heritage of the Union Territory (UT).Officials stated that the e-buses decision intends to provide an eco-friendly public transportati..

Rajasthan government plans to develop hi-tech city near Jaipur
On the lines of Gujarat International Finance Tech (GIFT) City and Hyderabad Information Technology and Engineering Consultancy (HITEC) City, Raj govt is gearing up to develop a "hi-tech city" close to Jaipur. Recently, Boston Consulting Group – a multinational consulting firm – gave a presentation on the concept of hi-tech cities, follwing which the state govt has started looking for suitable land on outskirts of Jaipur. "We are going to construct a hi-tech city on the outskirts of Jaipur. We are trying to ascertain the amount of land required for core areas of the city and for areas wh..