Inaugurates its first fully-integrated off-site manufacturing plant in Hyderabad
Redefine the future of urban mobility! Join us at the Metro Rail Conference 2025 to explore groundbreaking ideas and insights. 👉 Register today!
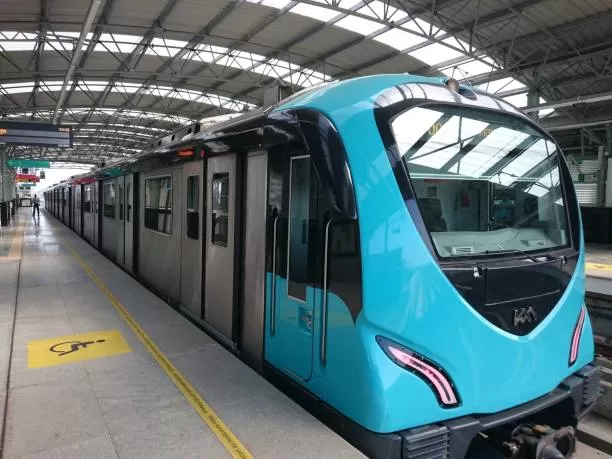
Telangana Eyes Rail Boost for $1 Trillion Goal
Telangana Chief Minister A Revanth Reddy emphasized the state's commitment to contributing $1 trillion to India's $5 trillion economic vision, contingent on robust railway infrastructure development. Speaking virtually at the inauguration of the modernized Cherlapally terminal, the CM called for central government support for key rail projects, including the second phase of Hyderabad Metro and the early execution of the Vikarabad-Krishna rail line via Kodangal. Highlighting Telangana's land-locked nature, Reddy proposed a dedicated rail line between Secunderabad and Machilipatnam port in Andhr..
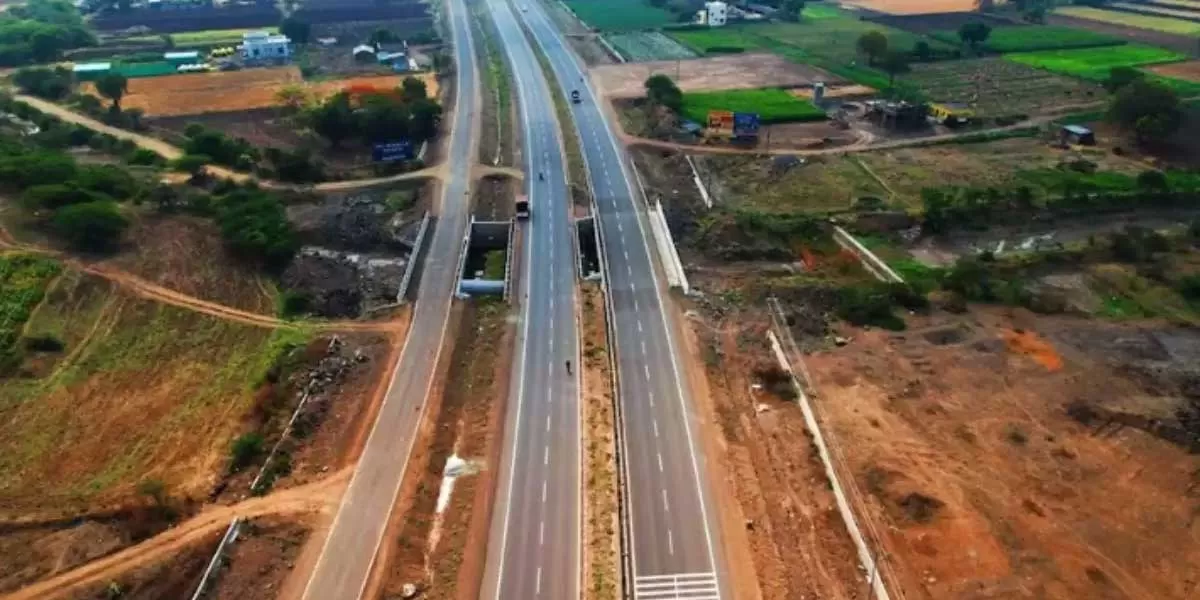
Thane Reviews Road Projects Amid Key Challenges
The city of Thane has recently undertaken a comprehensive review of its ongoing road infrastructure projects, focusing on overcoming key challenges that have hindered their timely completion. The review meeting, led by senior municipal officials, was aimed at assessing the current progress of multiple roadworks and addressing obstacles such as land acquisition issues, delayed approvals, and lack of coordination between departments. Among the most pressing concerns raised during the review were the frequent disruptions caused by local traffic, difficulties in obtaining necessary permissions for..
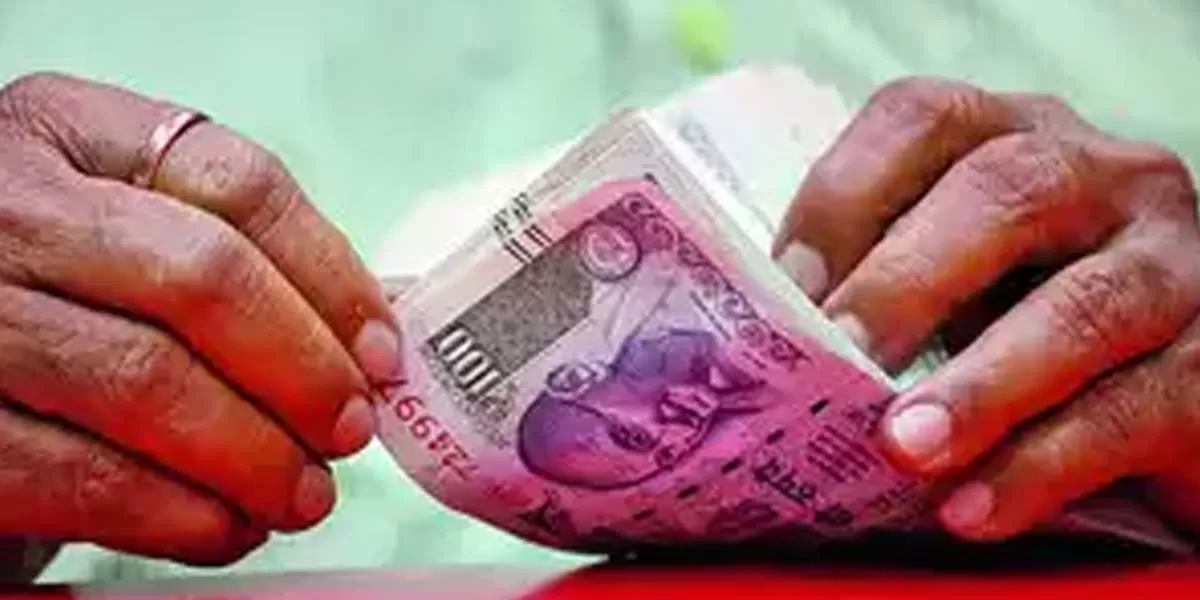
MP Expands Vikram Udyogpuri for Investments
The Madhya Pradesh Industrial Development Corporation (MPIDC) has acquired over 400 hectares of private land to develop Phase 2 of the Vikram Udyogpuri industrial area. This expansion aims to attract significant industrial investments and address the rising demand for space in the region. Vikram Udyogpuri currently spans 458 hectares and is nearing full capacity. The MPIDC has initiated the process of land acquisition and is preparing a detailed project report for the second phase. This strategic project will be a highlight at the upcoming Investors' Summit 2025 in Bhopal this February. "We ..