Redefine the future of urban mobility! Join us at the Metro Rail Conference 2025 to explore groundbreaking ideas and insights. 👉 Register today!
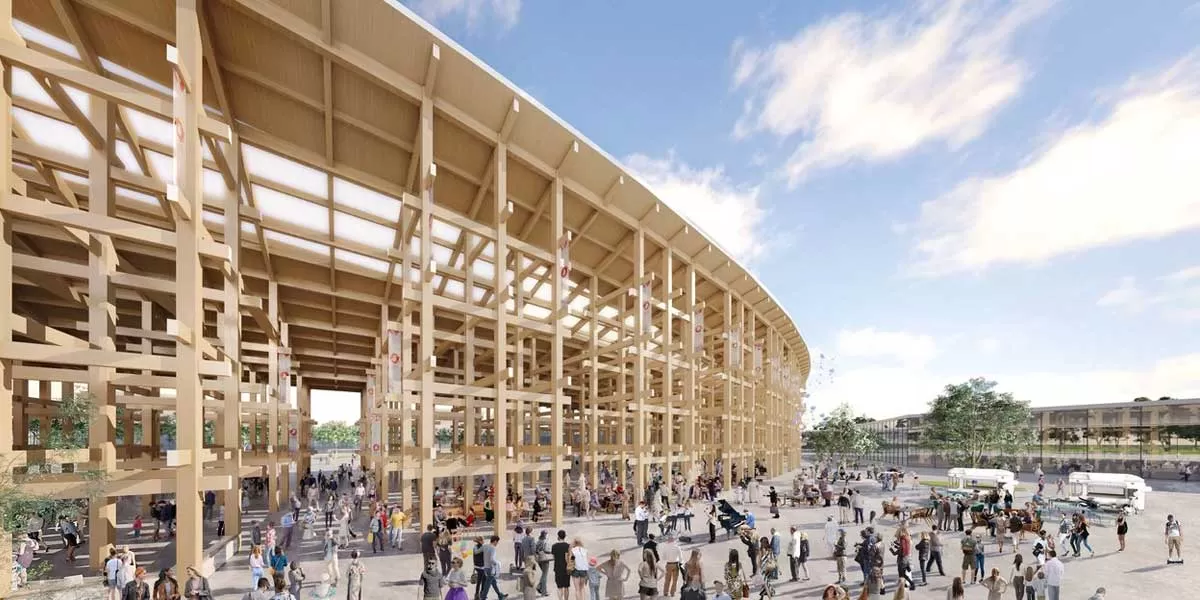
Osaka Expo 2025 to Feature World’s Largest Wooden Structure
Osaka Expo 2025 will showcase the world’s largest wooden structure—a spectacular canopy encircling the 155-hectare exhibition grounds. Designed by architect Sou Fujimoto, the structure combines cutting-edge technology with Japan’s thousand-year tradition of wooden construction to create a futuristic yet sustainable landmark.“This is the biggest wooden construction in the world, so we used the latest technology alongside Japan's ancient craftsmanship to achieve a futuristic design,” Mr Fujimoto said. Rigorous testing ensured the strength of the beams and joints for the immense structu..
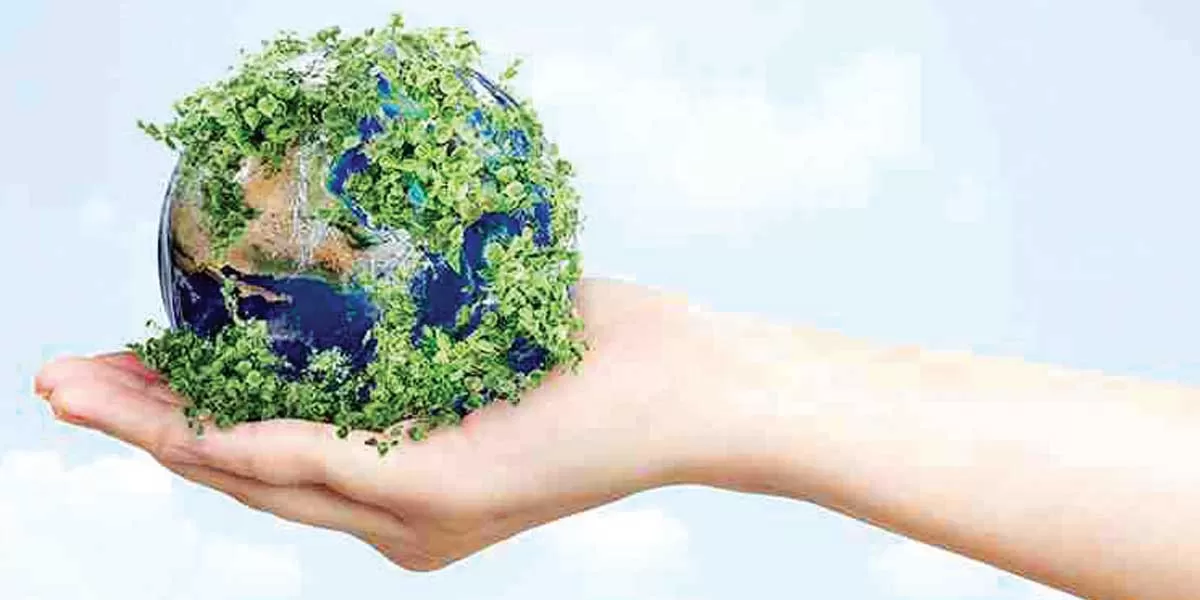
India ranks 6th globally with 127 Net-zero firms
India has secured the sixth position globally in corporate climate action, with 127 companies committing to net-zero targets under the Science- Based Targets initiative (SBTi), according to the latest report from ICRA ESG Ratings.Although India contributes approximately 7 per cent of global emissions, its corporate commitments reflect a growing awareness of climate concerns. However, high-emission sectors such as power, energy, and cement are lagging in adopting these goals.The report reveals that fewer than 10 per cent of firms in these high-emission sectors, which contribute to 55 per cent o..
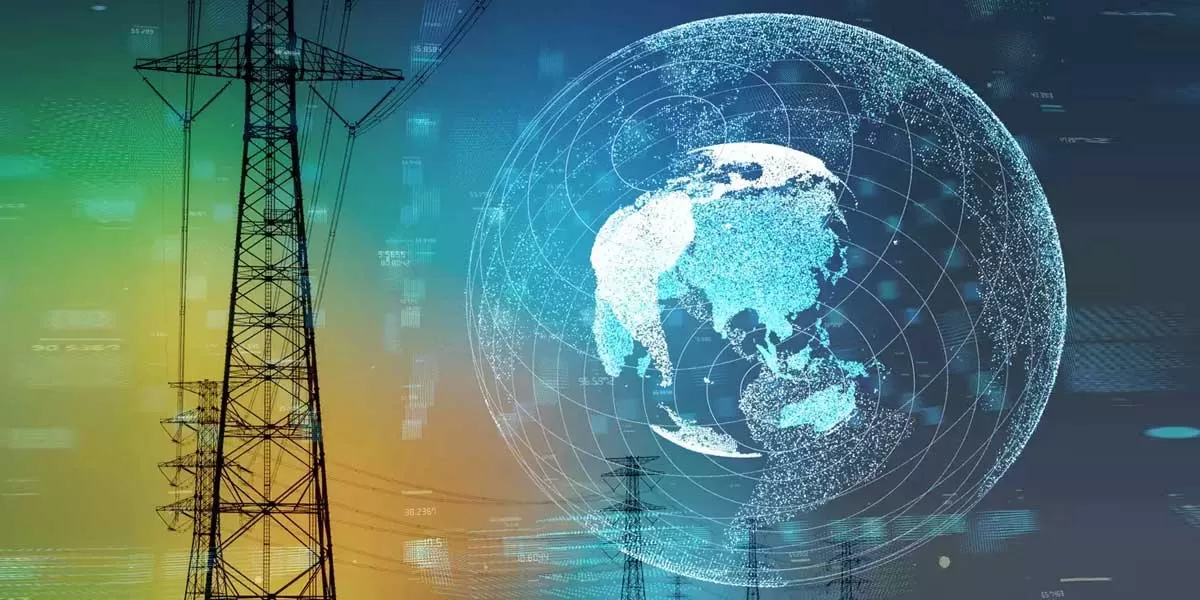
Power prices fall 31% amid renewable push
The average price of electricity traded on India’s power exchanges during October-November 2024 fell by 31 per cent year-on-year (YoY) to Rs.3.61 per unit in the Day-Ahead Market (DAM), down from Rs.5.23 per unit in the same period last year. Similarly, Real-Time Market (RTM) prices dropped by 29 per cent to Rs.3.59 per unit, compared to Rs.5.04 per unit a year ago, as per industry data. The price drop was driven by a surge in renewable energy generation, particularly hydro and wind power, supported by favourable monsoon conditions. Improved fuel availability and government-led ini..