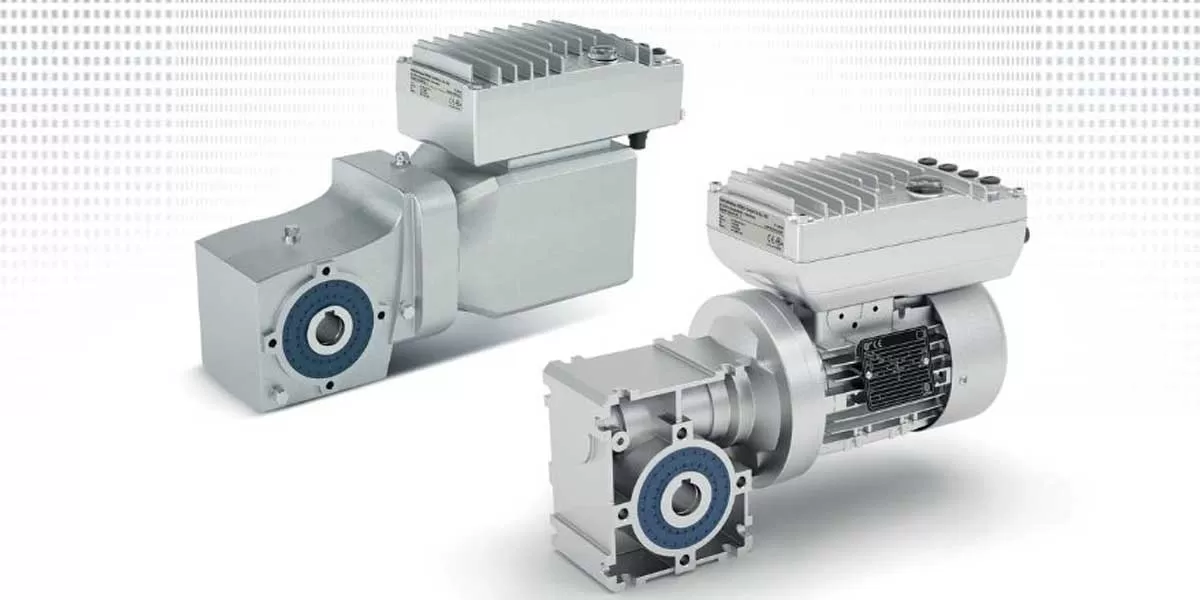
NORD DRIVESYSTEMS equips its drive components with QR codes
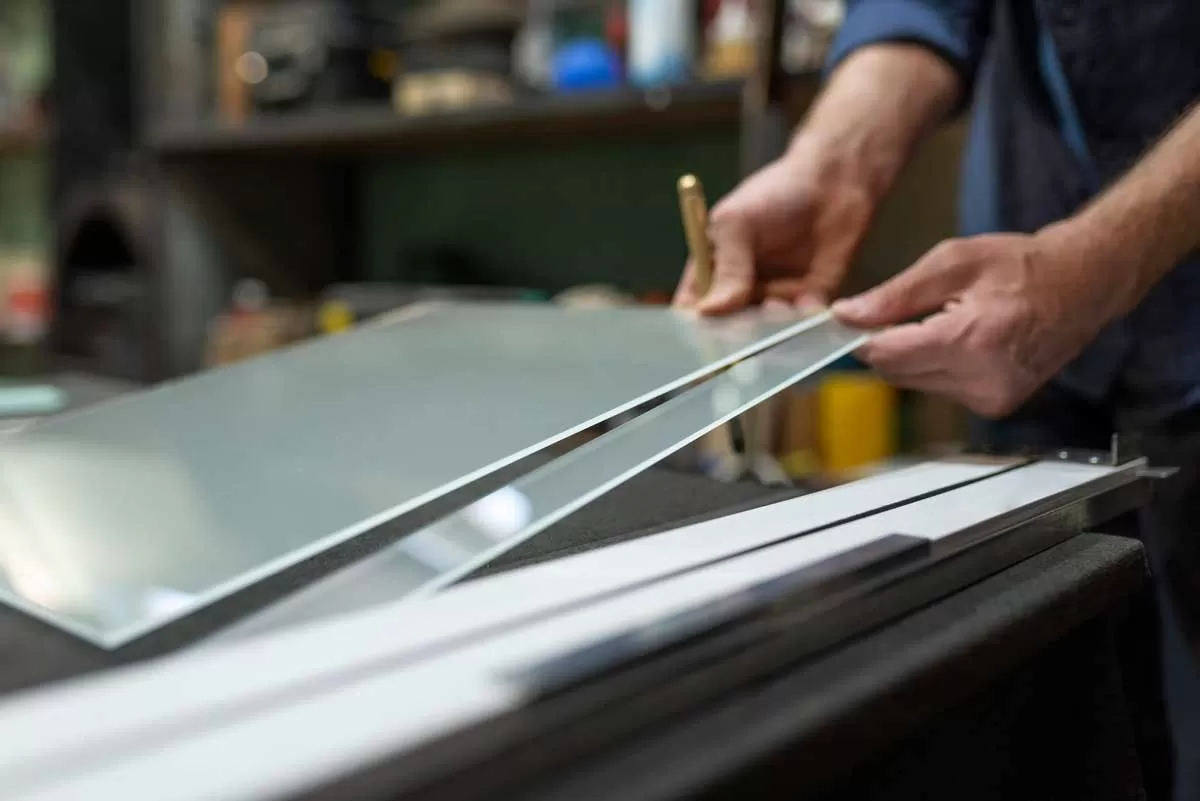
FIMI seeks urgent RoDTEP extension for aluminium exporters
"The Federation of Indian Mineral Industries (FIMI) has urged the Ministry of Commerce and Industry to extend the Remission of Duties or Taxes on Export Products (RoDTEP) Scheme for aluminium-producing units operating under Advance Authorisation (AA), Export Oriented Units (EOUs), and Special Economic Zones (SEZs).This appeal follows a similar request made by the Aluminium Association of India (AAI) to the Ministry of Finance, citing the need to safeguard the competitiveness of nearly 45 per cent of India’s aluminium exports originating from AA/EOU/SEZ units.In a letter to Commerce Secretary..
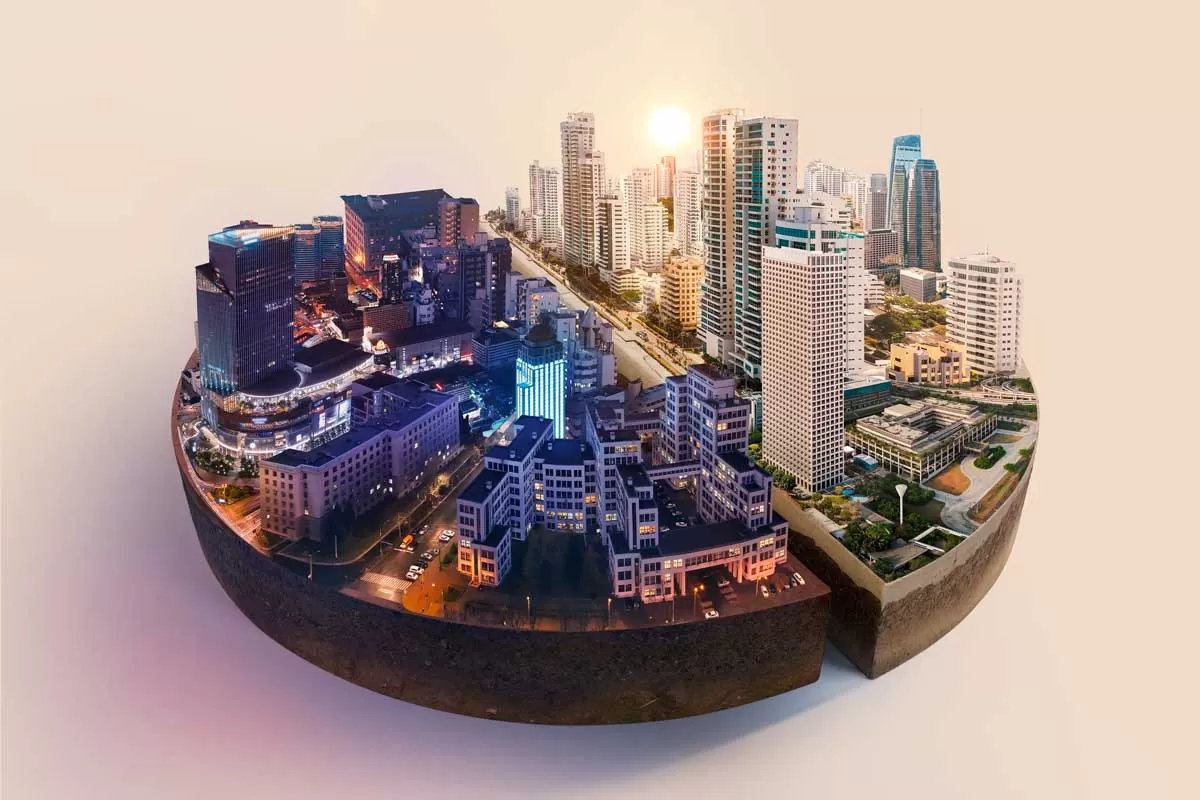
Mumbai logs over 12,000 property deals in April; revenue nears Rs 9.9 bn
Mumbai (BMC limits) is set to clock over 12,142 property registrations in April 2025, contributing more than Rs 9.9 billion in state revenue, according to Knight Frank India. This marks the city’s strongest April performance in 13 years, registering a 4 per cent year-on-year rise in volumes. However, stamp duty revenue dipped by 6 per cent during the same period.Residential transactions continue to dominate, accounting for 80 per cent of total registrations. Notably, premium housing gained momentum, with the share of properties priced above Rs 2 crore rising from 22 per cent to 25 per cent, ..
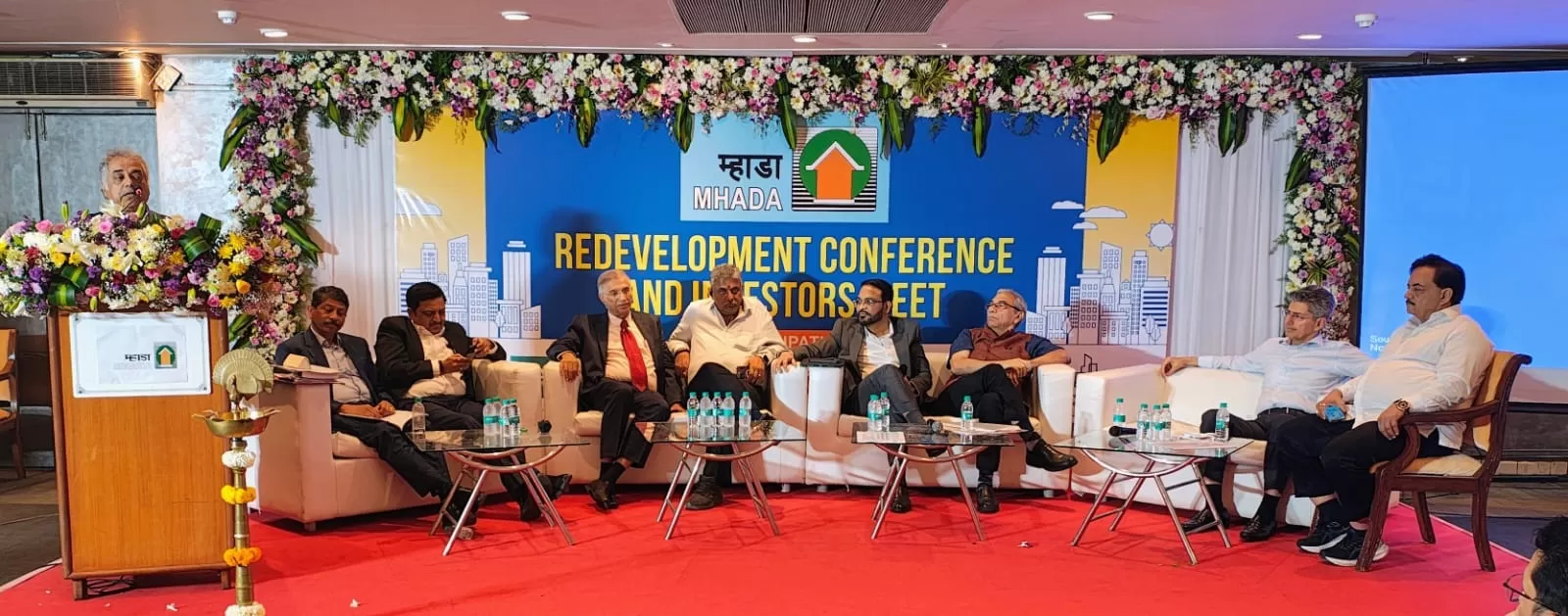
MHADA to issue redevelopment NOCs within 6 weeks: Jaiswal
In a major boost to Mumbai’s redevelopment momentum, Mr. Sanjeev Jaiswal, IAS, Vice President and CEO of MHADA, announced that No Objection Certificates (NOCs) for the redevelopment of old cessed buildings submitted under Section 79A(1a) or 79A(1b), along with 51 per cent resident consent, will be issued within six weeks. The directive, declared at MHADA’s 2nd Redevelopment Conference and Investors Summit, brings these approvals under the Right to Service Act. If delayed beyond the stipulated timeframe, the NOC will be deemed approved.The event, held at MIG Club, Bandra (East), brought tog..