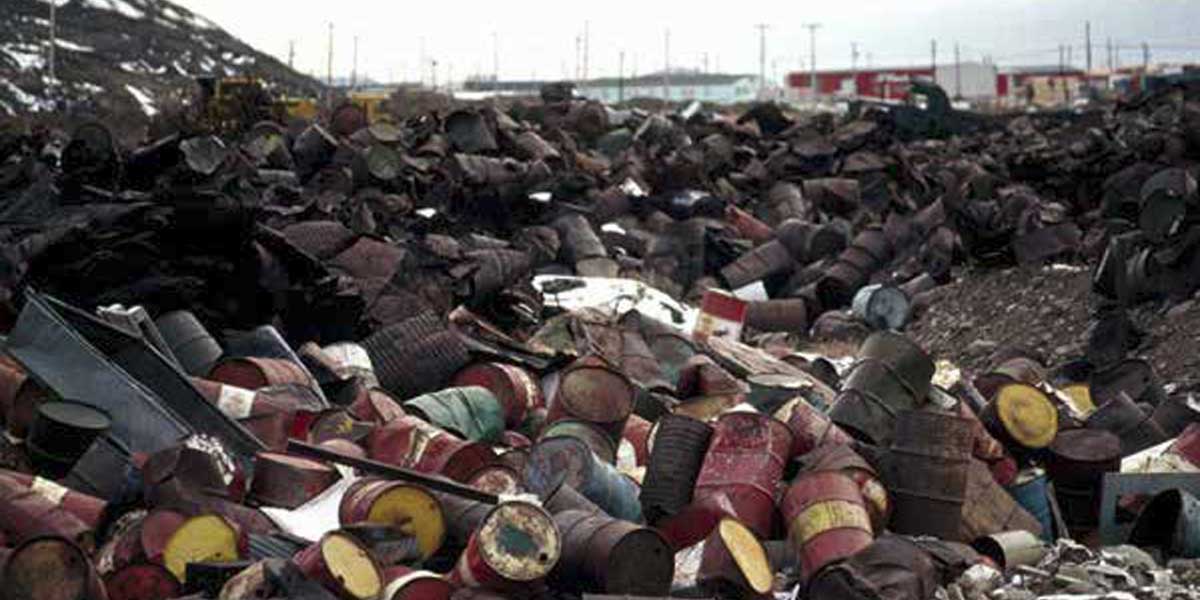
Challenges while utilizing hazardous industrial waste.
Read full article
CW Gold Benefits
- Weekly Industry Updates
- Industry Feature Stories
- Premium Newsletter Access
- Building Material Prices (weekly) + trends/analysis
- Best Stories from our sister publications - Indian Cement Review, Equipment India, Infrastructure Today
- Sector focused Research Reports
- Sector Wise Updates (infrastructure, cement, equipment & construction) + trend analysis
- Exclusive text & video interviews
- Digital Delivery
- Financial Data for publically listed companies + Analysis
- Preconceptual Projects in the pipeline PAN India
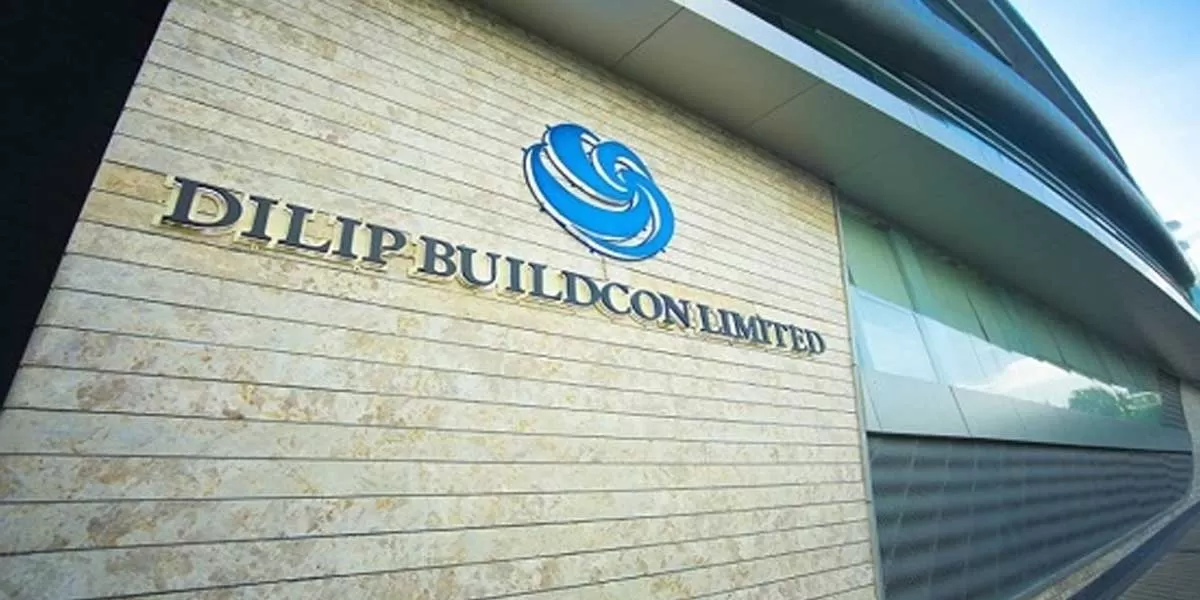
Dilip Buildcon wins bid for BharatNet Phase III broadband project
Dilip Buildcon announced on Tuesday, November 12, that its STL-DBL consortium had submitted the lowest bid for BSNL's BharatNet Phase III broadband connectivity project. The USOF-funded project, which aims to provide middle and last-mile connectivity in Jammu Kashmir and Ladakh, is valued at Rs.1,625.36 Crore. Dilip Buildcon holds a 70.23% stake in the implementation of the project. The project is expected to be completed in three years, and the corporation will secure a 10-year maintenance contract. In recent days, BSNL has awarded several contracts for the BharatNet project. On Monday, No..
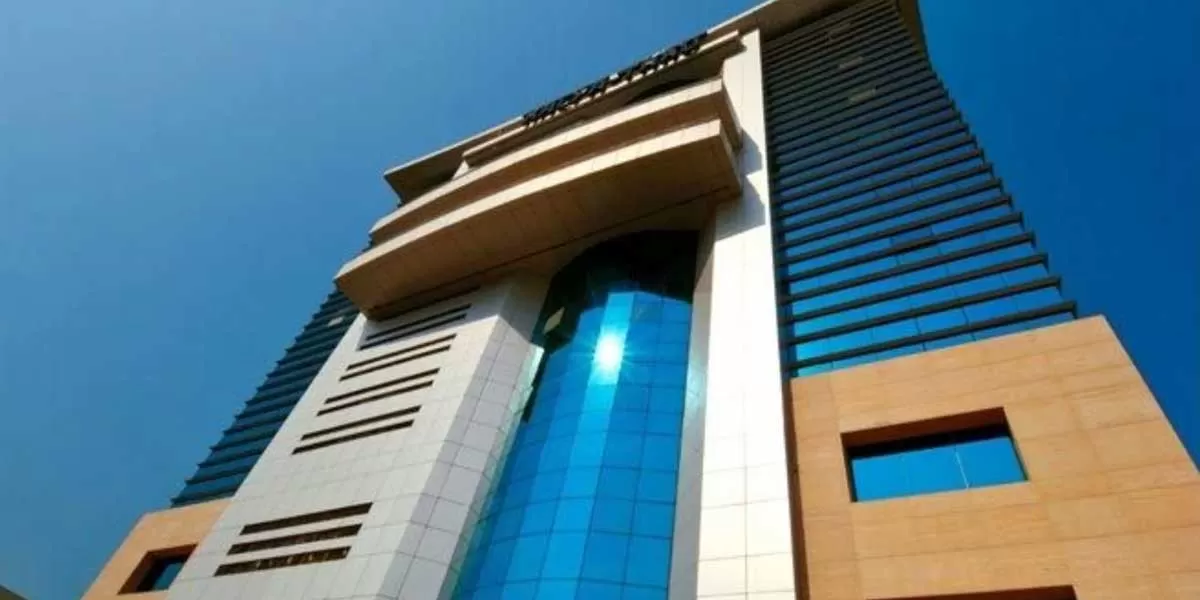
KPIL secures new orders worth Rs 22.73 billion
Kalpataru Projects International Limited (KPIL), along with its Joint Ventures (JVs) and international subsidiaries, secured new orders and notifications of awards amounting to Rs.2,273 Crores. The details of these new orders include: - Orders in the Transmission & Distribution (T&D) business in India and overseas markets. - Residential building projects in India. Manish Mohnot, the Managing Director & CEO of KPIL, expressed delight over the continuous inflow of orders, noting that their order book continues to grow, with significant traction in the T&D business, especially..
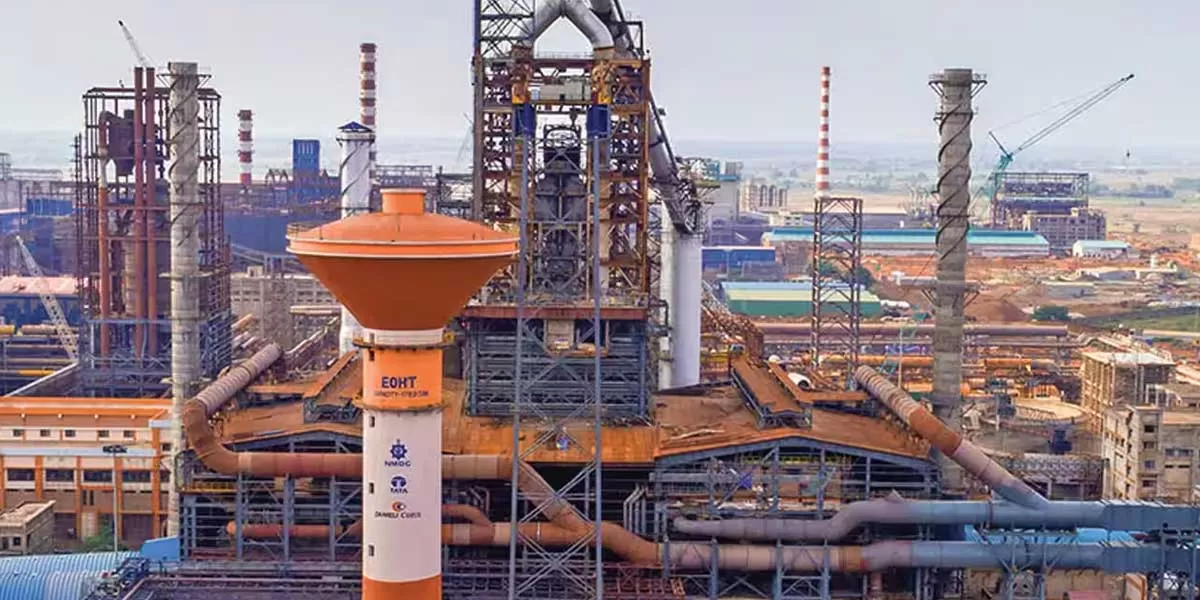
NMDC Steel Q2 loss expands to Rs 5.95 bn, income at Rs 15.35 bn
NMDC Steel announced on Tuesday that its loss had widened to Rs 595.37 crore in the September quarter, primarily due to a surge in expenses. The company had reported a loss of Rs 131.10 crore during the same period last year, according to an exchange filing. The company’s total income increased to Rs 1,535.46 crore, up from Rs 290.27 crore a year earlier. However, NMDC Steel's expenses escalated to Rs 2,364.39 crore in the second quarter of the current fiscal year, compared to Rs 464.93 crore in the corresponding period of the previous year. NMDC Steel Ltd, which was demerged from the mi..