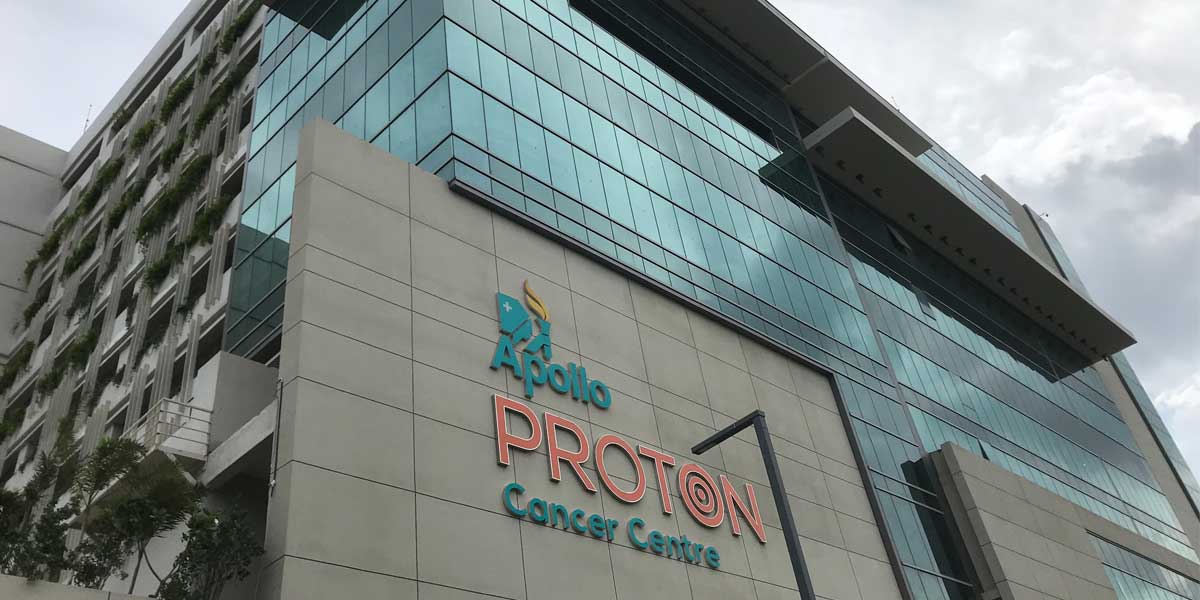
Apollo Proton Cancer Centre, Chennai certified Platinum by IGBC
Read full article
CW Gold Benefits
- Weekly Industry Updates
- Industry Feature Stories
- Premium Newsletter Access
- Building Material Prices (weekly) + trends/analysis
- Best Stories from our sister publications - Indian Cement Review, Equipment India, Infrastructure Today
- Sector focused Research Reports
- Sector Wise Updates (infrastructure, cement, equipment & construction) + trend analysis
- Exclusive text & video interviews
- Digital Delivery
- Financial Data for publically listed companies + Analysis
- Preconceptual Projects in the pipeline PAN India
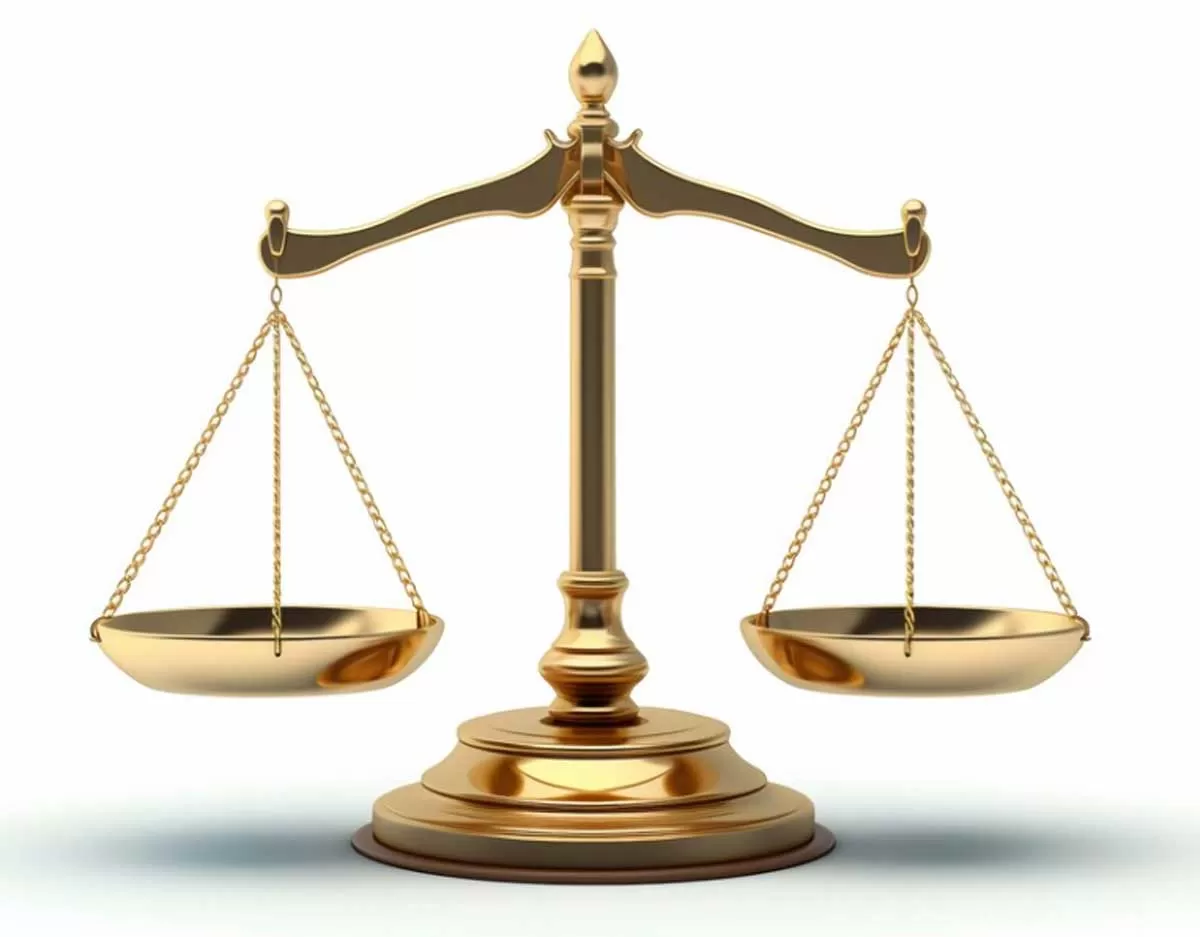
Development of ICT in Indian Judiciary through e-Courts Phases
The eCourts project, launched under the National eGovernance Plan in 2007, is a Mission Mode Project aimed at modernisng the Indian judiciary through the adoption of Information and Communication Technology (ICT). The initiative is grounded in the "National Policy and Action Plan for Implementation of ICT in the Indian Judiciary" and has been implemented in multiple phases. Phase I (2011–2015) focused on the computerization of judicial infrastructure and ensuring connectivity across courts. During this phase, 14,249 district and subordinate courts were computerised, and Local Area Networks ..
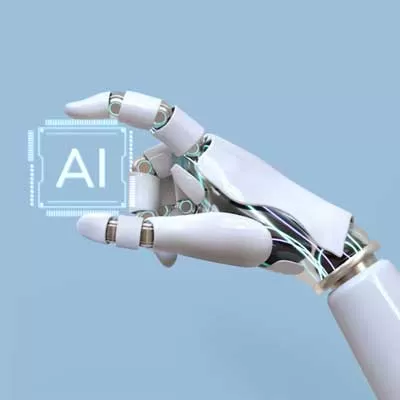
Minority Affairs Minister to Launch PM VIKAS Project via DGSMC
On 29th March 2025, the Ministry of Minority Affairs will launch a new program under the Pradhan Mantri Virasat Ka Samvardhan (PM VIKAS) scheme, aimed at enhancing skill development and educational support for minority communities. The initiative, which will be implemented by the Delhi Sikh Gurdwara Management Committee (DSGMC), will benefit a total of 31,600 candidates across the country. Out of the total beneficiaries, 29,600 individuals will receive skill training in industry-relevant fields, while 2,000 candidates will receive educational support. The training will focus on job roles ali..
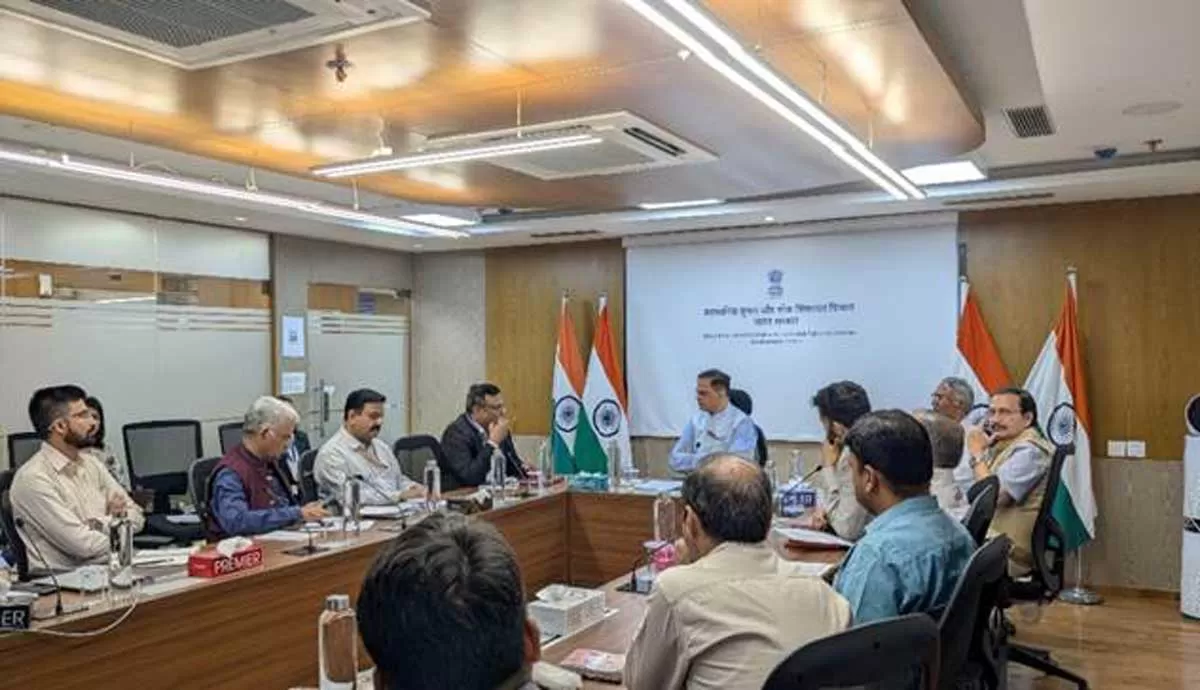
DARPG and Bhashini Launch Multilingual Tool for Citizen Grievances
To enhance the effectiveness, accessibility, and responsiveness of the grievance redressal system, the Department of Administrative Reforms and Public Grievances (DARPG) has signed a Master Service Agreement with Digital India Bhashini on March 28, 2025. This agreement marks the implementation of a multimodal, multilingual e-Governance solution for the Centralised Public Grievance Redress and Monitoring System (CPGRAMS), in line with the directive of the Prime Minister of India to bring qualitative improvements to citizen service delivery. The new solution aims to empower citizens from diver..