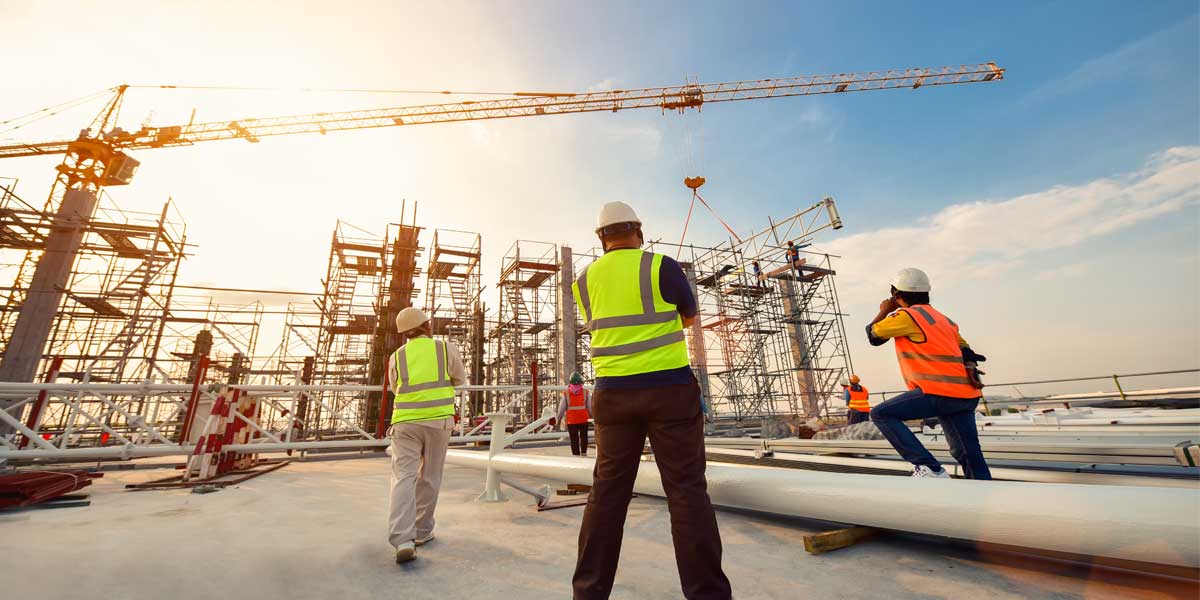
A Silent Revolution
Read full article
CW Gold Benefits
- Weekly Industry Updates
- Industry Feature Stories
- Premium Newsletter Access
- Building Material Prices (weekly) + trends/analysis
- Best Stories from our sister publications - Indian Cement Review, Equipment India, Infrastructure Today
- Sector focused Research Reports
- Sector Wise Updates (infrastructure, cement, equipment & construction) + trend analysis
- Exclusive text & video interviews
- Digital Delivery
- Financial Data for publically listed companies + Analysis
- Preconceptual Projects in the pipeline PAN India
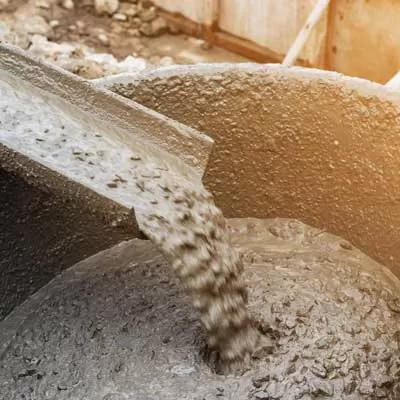
JK Cement emerges successful bidder for Mahan coal mine in Madhya Pradesh
This marks the company’s second commercial coal block win, following its acquisition of the West of Shahdol (South) coal block. "The company is committed to becoming self-reliant for its existing cement plants and upcoming projects," JKC stated. The surplus coal from the mine will be sold commercially. The vesting order was handed over to JK Cement during a ceremony at Shastri Bhawan, New Delhi, a critical milestone for commencing mining operations within the stipulated timeline...
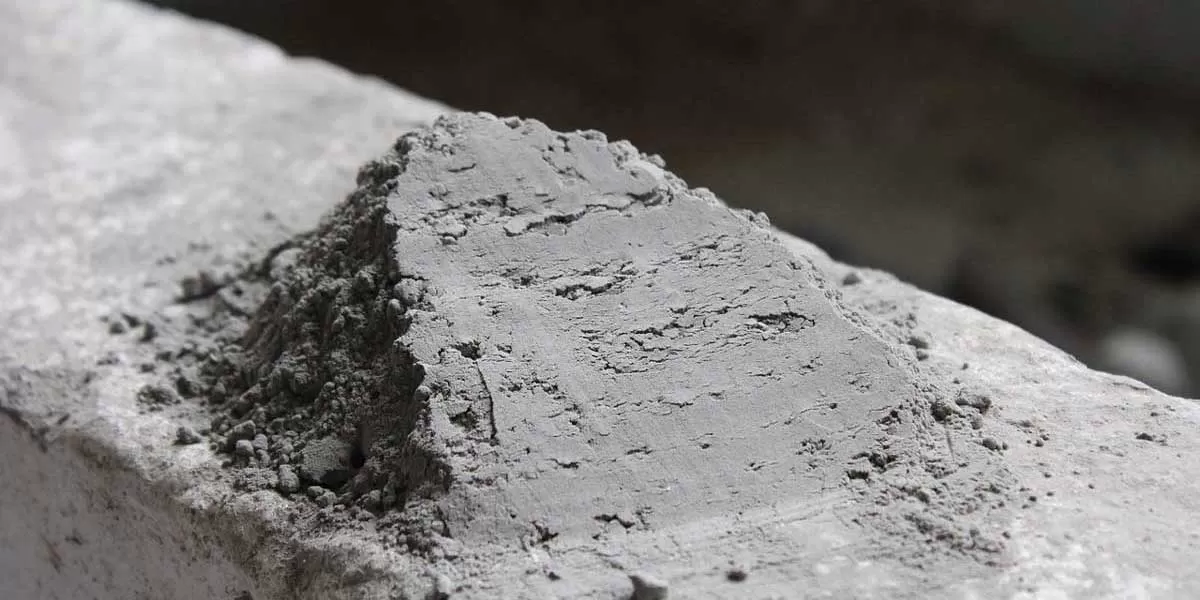
Prism Johnson's cement division goes live with Ramco ERP Suite
Prism Johnson has successfully gone live with the Ramco ERP Suite for its Cement Division. This milestone marks a significant step in Prism Johnson's digital transformation journey, leveraging Ramco Systems' advanced enterprise solutions and process control systems to streamline business processes, manufacturing operations and drive efficiency. The implementation includes cutting-edge modules for Maintenance, Sales, Distribution, Finance, Procurement, Manufacturing, Quality, and HR Management (HRM). These solutions enable Prism Johnson to achieve seamless integration across its business and wo..
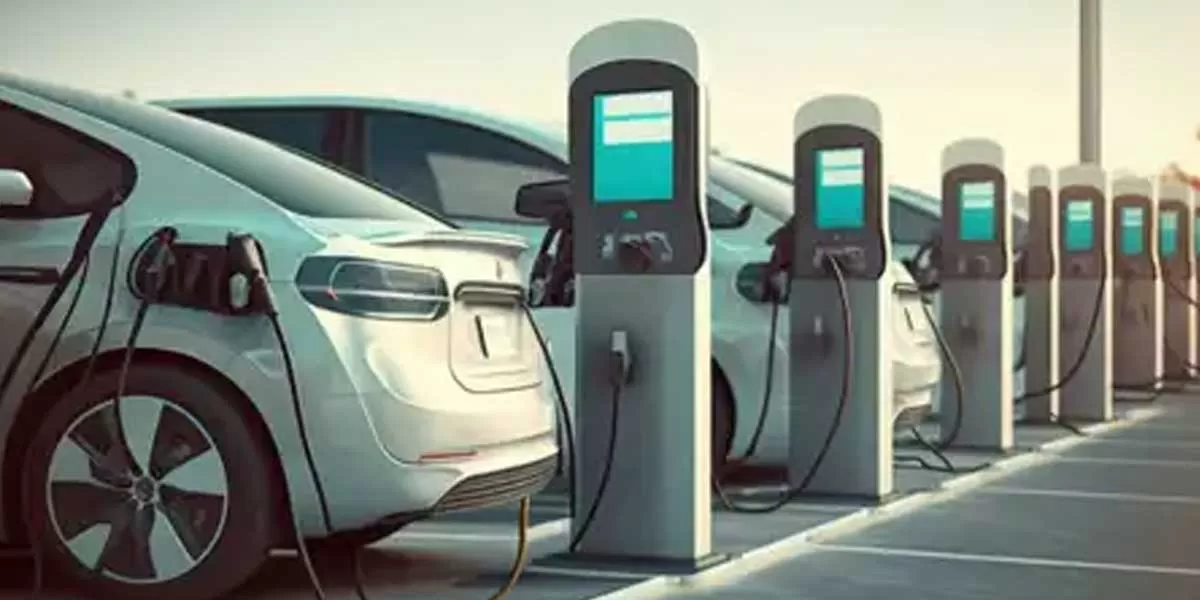
Indian shadow bank Shriram Finance gets record $1.28 billion loan
Shriram Finance Ltd. is reported to have borrowed $1.28 billion in a multi-currency social loan, marking the largest offshore facility ever undertaken by an Indian shadow lender. According to a press release issued by Shriram, the deal is divided across the dollar, euro, and dirham. Sources familiar with the transaction, who wished to remain anonymous, indicated that the tenors in the multi-tranche deal range from three to five years. This loan adds to the surge of offshore debt sales by Indian shadow lenders this year, a trend prompted by the Reserve Bank of India's tightening of rules in Nov..