
We completed our brownfield expansion of 4.2 mtpa capacity
Read full article
CW Gold Benefits
- Weekly Industry Updates
- Industry Feature Stories
- Premium Newsletter Access
- Building Material Prices (weekly) + trends/analysis
- Best Stories from our sister publications - Indian Cement Review, Equipment India, Infrastructure Today
- Sector focused Research Reports
- Sector Wise Updates (infrastructure, cement, equipment & construction) + trend analysis
- Exclusive text & video interviews
- Digital Delivery
- Financial Data for publically listed companies + Analysis
- Preconceptual Projects in the pipeline PAN India
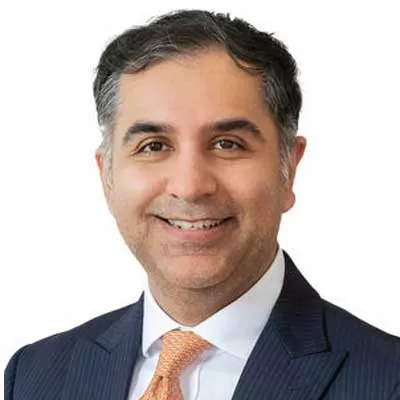
Varun Malik Joins ANAROCK as MD, Head of Capital Markets, APAC
ANAROCK Capital has appointed Varun Malik as Managing Director, Head of Capital Markets (APAC), marking a strategic move to expand its presence across Asia-Pacific. Based in Singapore, Malik will drive ANAROCK’s capital markets initiatives in the region.A real estate finance veteran, Malik brings over 18 years of experience in structuring complex cross-border transactions across South-East Asia and Australia. He has led debt and equity deals for REITs, fund managers, and developers, delivering strong returns and driving investor value.“We will redefine real estate capital solutions across ..
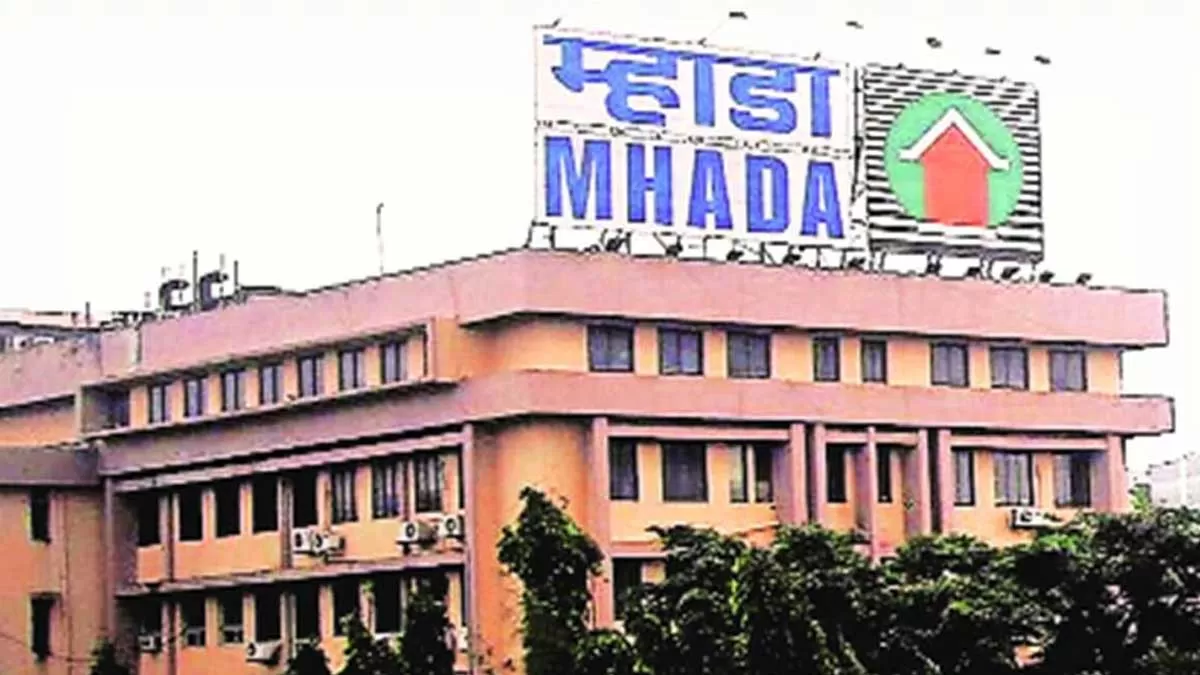
Patra Chawl lottery held, 663 families allotted homes
Mumbai's Siddharth Nagar (Patra Chawl) Co-operative Housing Society members in Goregaon (West) saw their 15-year wait come to a close as MHADA conducted a successful computerised lottery for 663 eligible members under its redevelopment scheme.The Mumbai Housing and Area Development Board conducted the draw using the RAT (Randomised Allotment of Tenement) system at Sardar Vallabhbhai Patel Hall. The lottery, overseen by Mr. Milind Borikar, Chief Officer of Mumbai Board, ensured transparency by digitally allotting each member a building, wing, and floor.The project, located on Plot R-9, received..
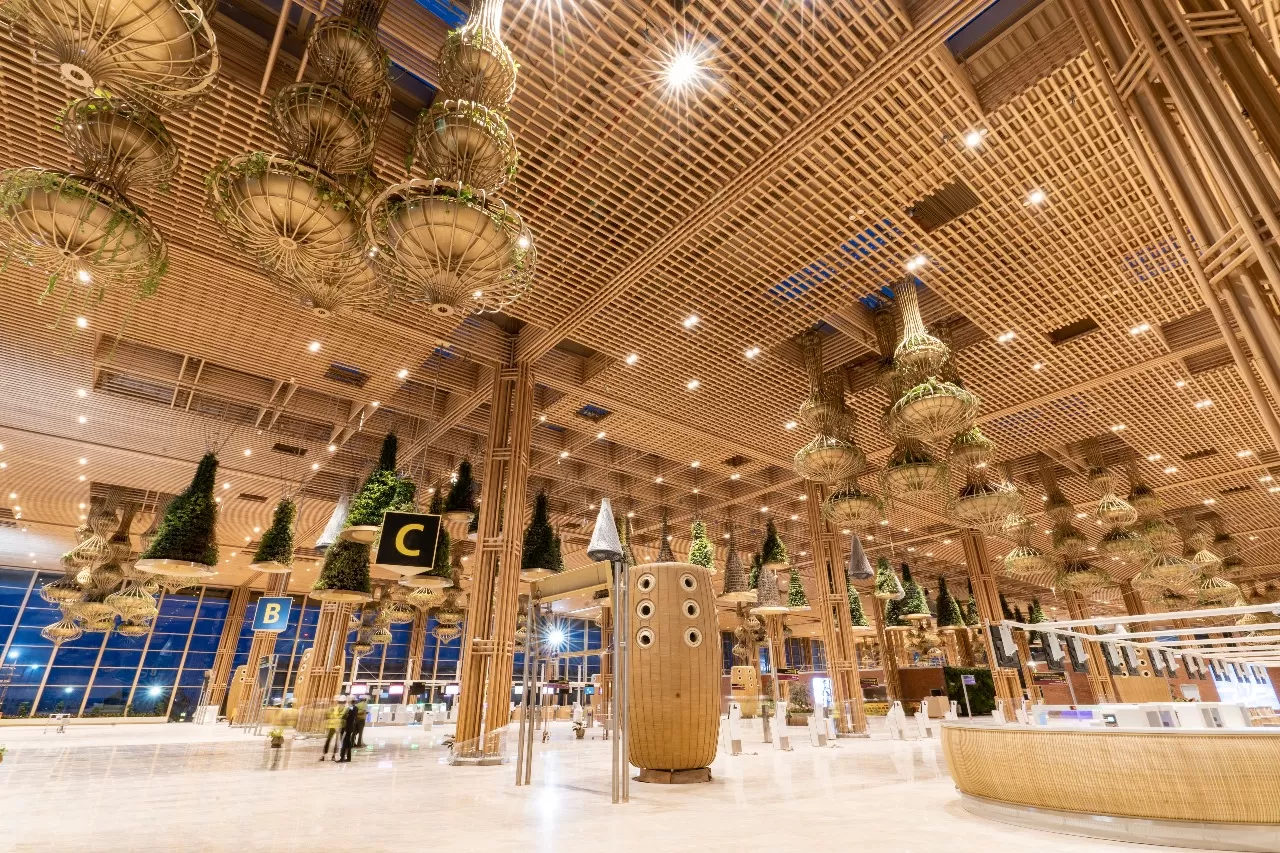
BLR Airport crosses 41 million passengers, 500,000 MT cargo
Kempegowda International Airport, Bengaluru (BLR Airport), has recorded key operational milestones in FY 2024-25, crossing 41.88 million passengers and handling 502,480 metric tonnes of cargo. This marks a year-on-year passenger growth of 11.6 per cent and a 14 per cent rise in cargo volumes.Domestic footfall reached 36.05 million, up 10 per cent, while international traffic saw a robust 25 per cent jump to 5.83 million, aided by Indigo’s global expansion and added frequencies by international carriers. BLR Airport now connects to 76 domestic and 33 international destinations, with Hanoi set..