
Sanjay Joshi, Chief Manufacturing Officer: All plants at Nuvoco are using fly ash
Read full article
CW Gold Benefits
- Weekly Industry Updates
- Industry Feature Stories
- Premium Newsletter Access
- Building Material Prices (weekly) + trends/analysis
- Best Stories from our sister publications - Indian Cement Review, Equipment India, Infrastructure Today
- Sector focused Research Reports
- Sector Wise Updates (infrastructure, cement, equipment & construction) + trend analysis
- Exclusive text & video interviews
- Digital Delivery
- Financial Data for publically listed companies + Analysis
- Preconceptual Projects in the pipeline PAN India
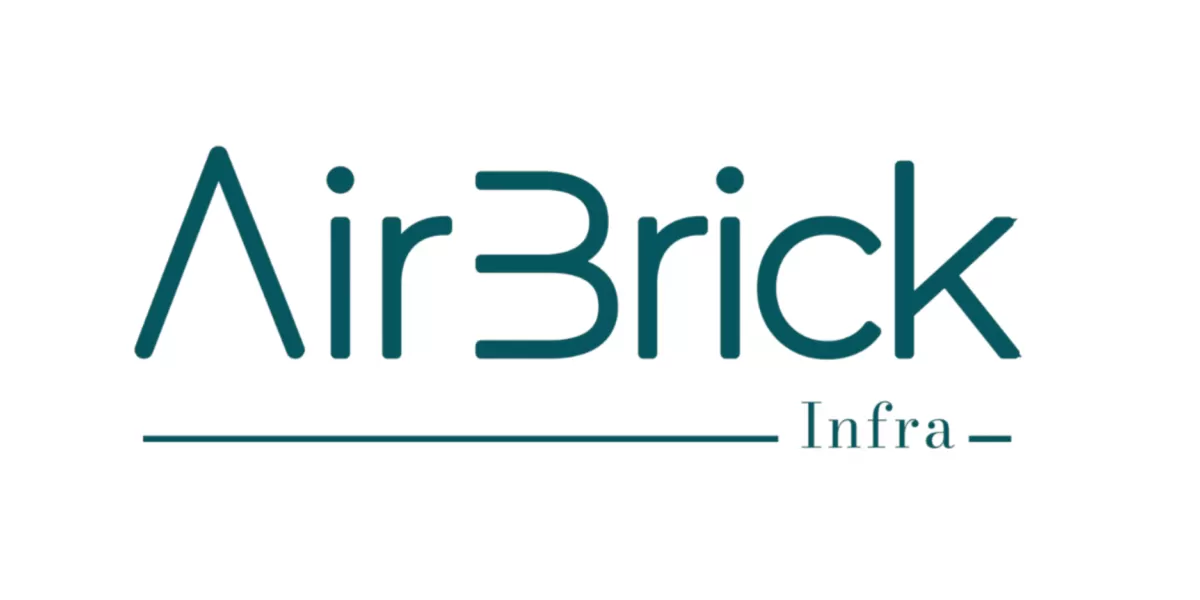
AirBrick Infra Sets Rs 1 billion Target, Expands to Dubai and Tier-II Cities
AirBrick Infra, one of India’s fastest-growing AI-led commercial interior design and build firms, has announced a sales order target of Rs 1 billion for FY 2025–26. The projection represents a 50 per cent growth over the previous fiscal year and reflects rising demand, increased repeat business, and the company's robust tech-first delivery model. Now in its third year of operations, AirBrick continues its rapid scale-up, having successfully delivered over 70 projects spanning 3 lakh sq ft in FY 2023–24. FY 2024–25 witnessed the onboarding of several Fortune 500 clients, sett..
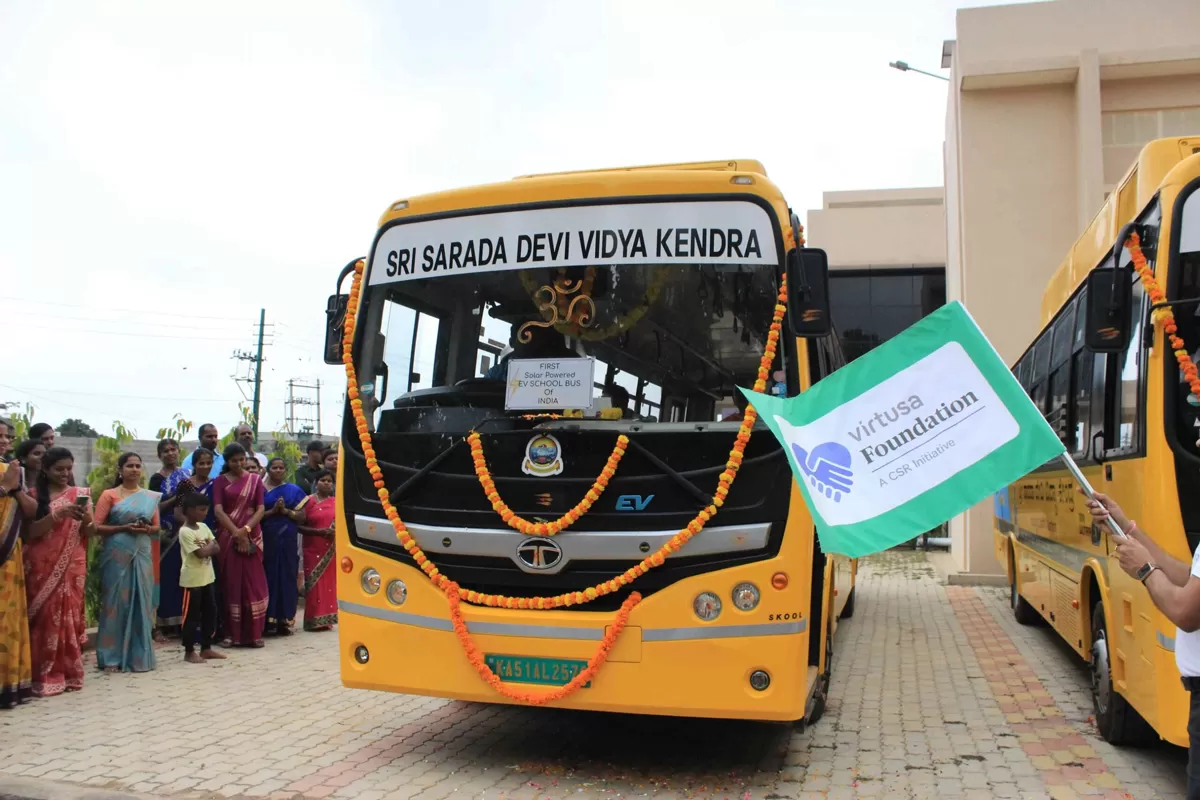
Virtusa Foundation Powers Green Education Drive in Bengaluru
The Virtusa Foundation, CSR arm of digital engineering and technology leader Virtusa Corporation, has announced key infrastructure and mobility initiatives at the Ramakrishna Mission, Shivanahalli, Bengaluru. The launch marks the inauguration of a 16-room residential facility for lady teachers and the deployment of two solar-powered electric buses, underscoring Virtusa’s commitment to its core pillars of Education, Environment and Empowerment (3Es). Located on the forest fringe near Bannerghatta National Park, the initiative supports tribal and underserved communities, complementi..
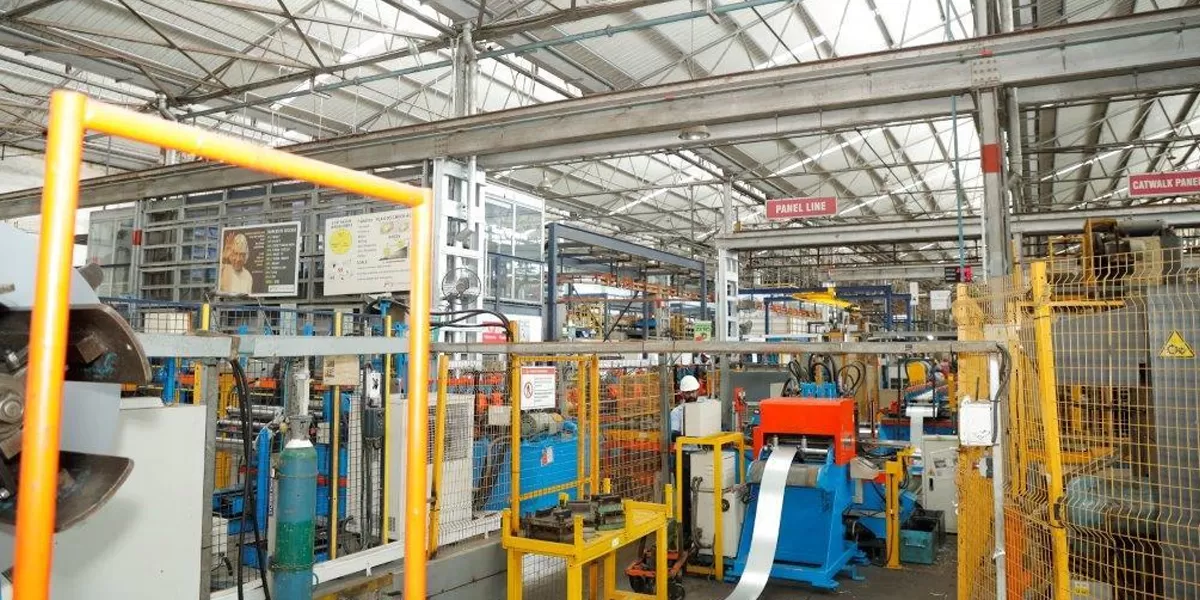
Godrej Enterprises Drives India’s Smart Green Logistics Shift
As India accelerates its transformation into a global manufacturing and logistics hub, Godrej Enterprises Group (GEG) is taking the lead with its smart, sustainable intralogistics solutions. Through its Material Handling Equipment (MHE) and Storage Solutions businesses, GEG is redefining operational efficiency in modern warehouses and factories using IoT, automation, and AI. GEG has consistently maintained a 20–25 per cent market share in the intralogistics sector over the past three years. Today, over 37 per cent of GEG’s revenues come from its Good & Green portfolio, and its net..