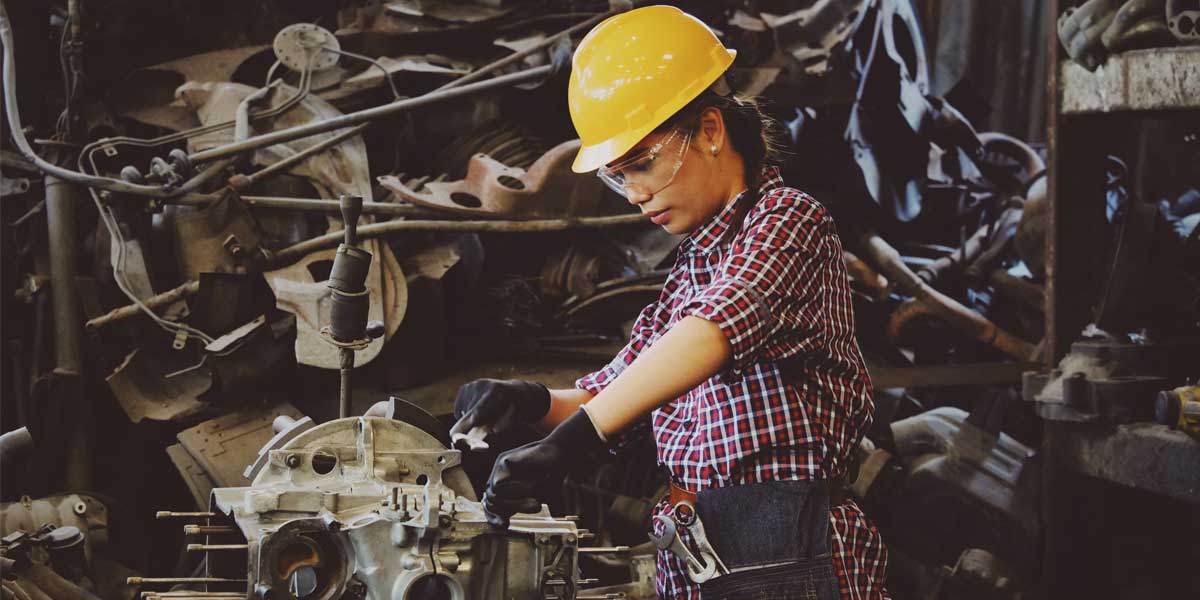
"Optimizing Diversity for Effective Team Collaboration"
Read full article
CW Gold Benefits
- Weekly Industry Updates
- Industry Feature Stories
- Premium Newsletter Access
- Building Material Prices (weekly) + trends/analysis
- Best Stories from our sister publications - Indian Cement Review, Equipment India, Infrastructure Today
- Sector focused Research Reports
- Sector Wise Updates (infrastructure, cement, equipment & construction) + trend analysis
- Exclusive text & video interviews
- Digital Delivery
- Financial Data for publically listed companies + Analysis
- Preconceptual Projects in the pipeline PAN India
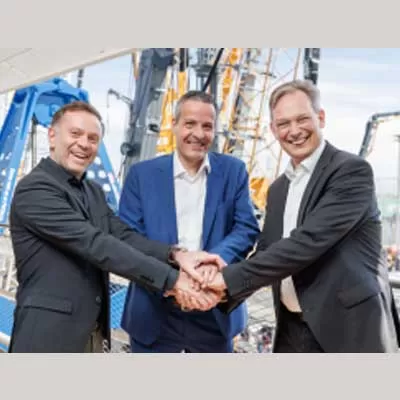
Liebherr, Reycom and Qualcomm Partner on Edge AI Gateway
Liebherr and Reycom have partnered with Qualcomm Technologies to launch LiRISE®—a next-generation edge AI gateway designed for autonomous and AI-powered industrial applications. The platform combines rugged hardware and scalable software with Qualcomm’s high-performance processors to bring advanced intelligence to machines operating in harsh environments.“By delivering security-rich, high-performance, and future-ready solutions, we help our customers navigate an increasingly complex world,” said Claus von Reibnitz, Head of Control Systems & Connectivity, Liebherr.LiRISE® integrat..
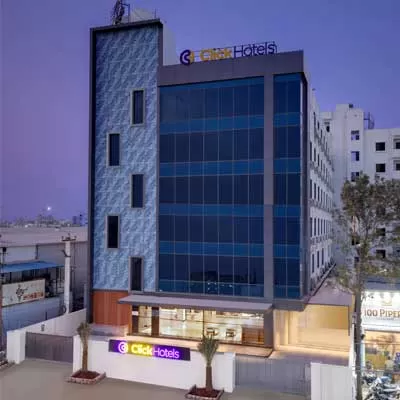
Suba Group Launches Third Hotel in Hyderabad
Suba Group of Hotels has launched Click Hotel Hyderabad, its third property in the city, expanding its presence in South India. Strategically located just 10 minutes from Rajiv Gandhi International Airport, the hotel caters to both business and leisure travellers. It is the group’s fourth major opening in two months.“We are delighted to launch our third hotel in Hyderabad,” said Mansur Mehta, Managing Director, and Mubeen Mehta, CEO, in a joint statement. “This reflects our vision of being the hospitality group of choice across South and the rest of India. Sustainability is central to ..
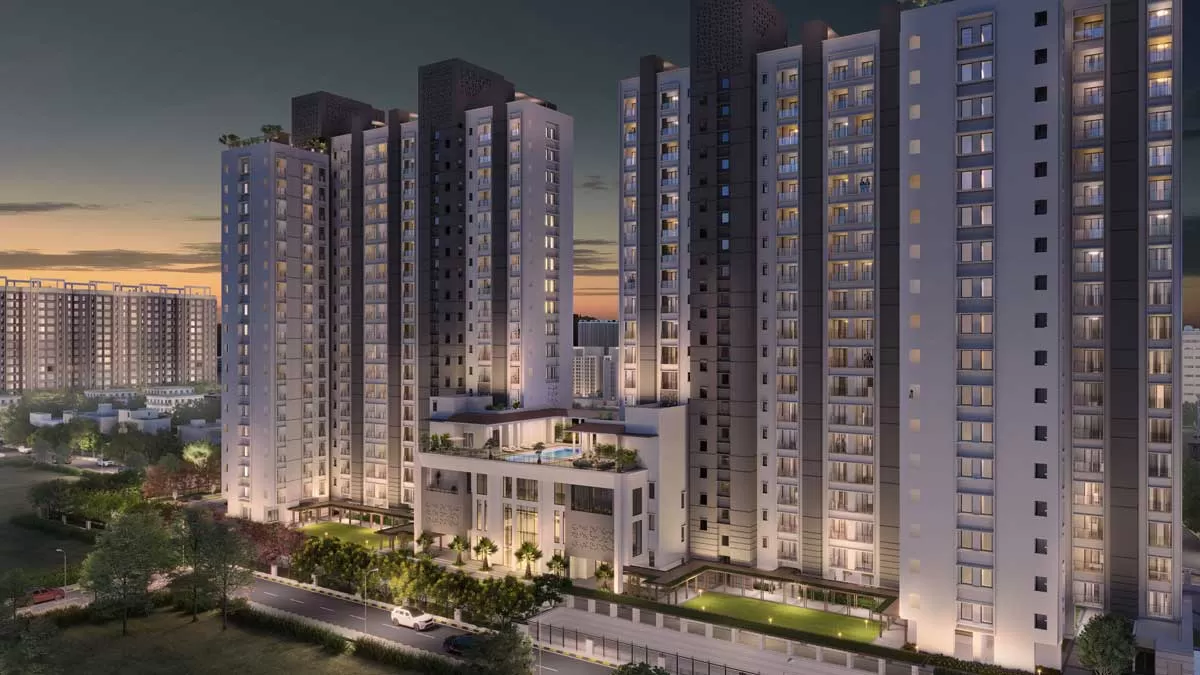
PioneerUrban launches Rs 3 billion senior living project ‘Advait’
PioneerUrban Land and Infrastructure has announced its entry into luxury senior living with a Rs 3 billion investment in ‘Advait’, a JV with J K Organisation. Located in Sector 50, Nirvana Country, Gurugram, the 2.6-acre project is scheduled for occupancy by early 2027.‘Advait’ is the first IGBC platinum-certified senior living project in Haryana licensed under the State’s Retirement Policy. It features two-bedroom apartments with caretaker’s rooms across 18-storey towers. The complex includes a 35,000 sq ft clubhouse, wellness facilities, and round-the-clock medical support by For..