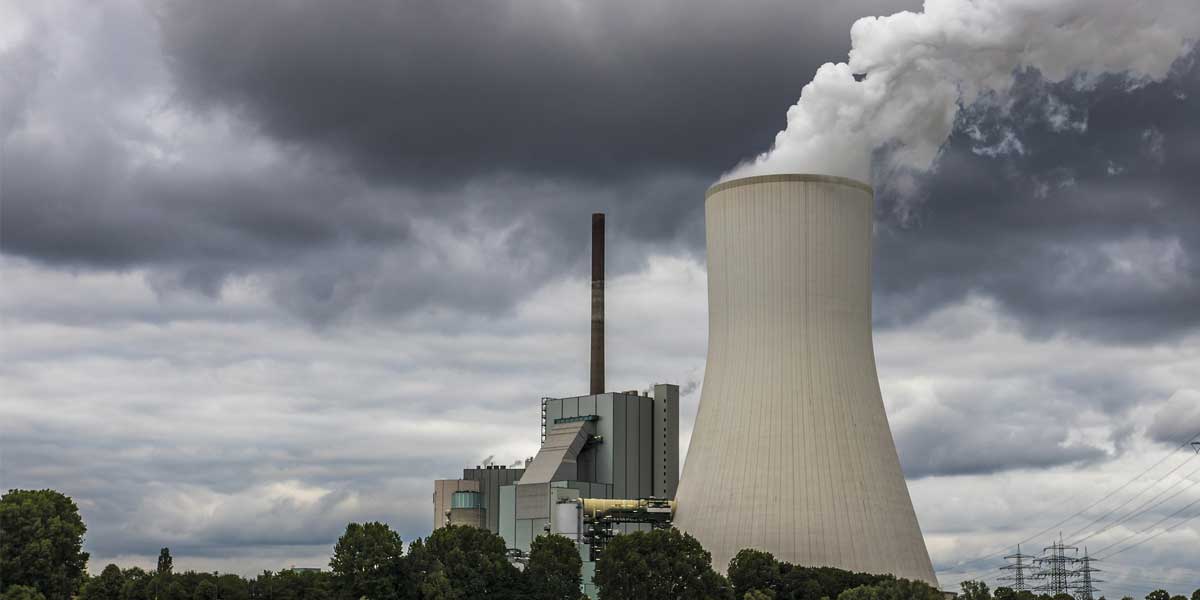
"Successful Strategies to Improve Communication in Teams"
Read full article
CW Gold Benefits
- Weekly Industry Updates
- Industry Feature Stories
- Premium Newsletter Access
- Building Material Prices (weekly) + trends/analysis
- Best Stories from our sister publications - Indian Cement Review, Equipment India, Infrastructure Today
- Sector focused Research Reports
- Sector Wise Updates (infrastructure, cement, equipment & construction) + trend analysis
- Exclusive text & video interviews
- Digital Delivery
- Financial Data for publically listed companies + Analysis
- Preconceptual Projects in the pipeline PAN India
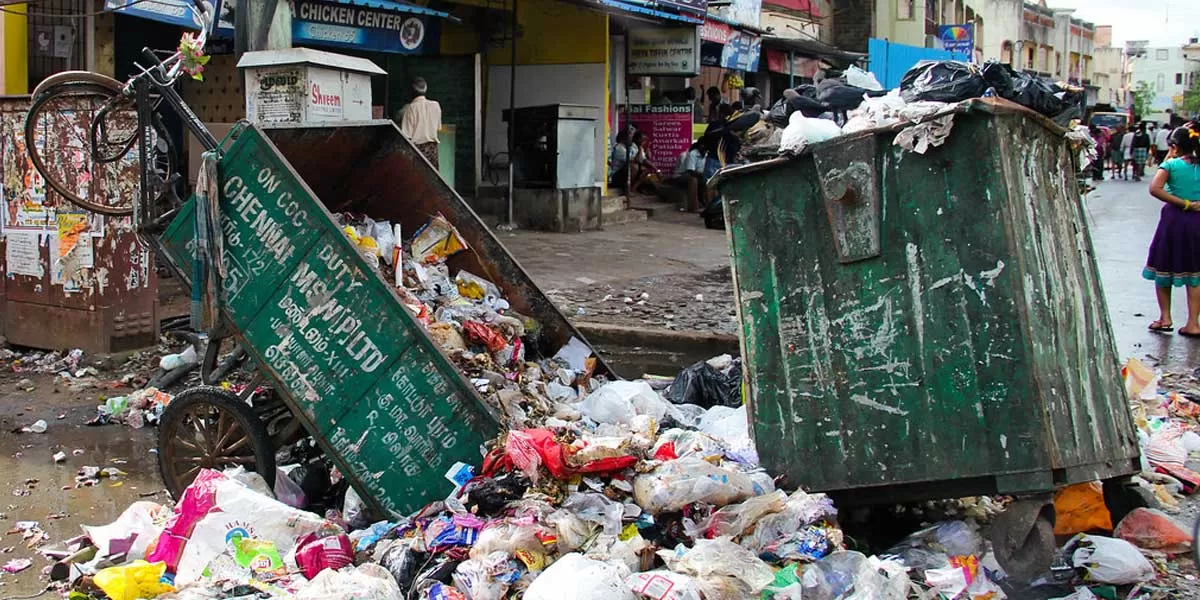
India Advances in Sustainable Solid Waste Management Technologies
In a significant step towards environmental sustainability, Indian scientists and research institutions have pioneered advanced technologies for the management of solid and plastic waste. These innovations span across various sectors, offering decentralised, eco-friendly solutions that bridge scientific advancement with practical implementation. A range of cutting-edge technologies have been developed for efficient solid waste management: Bio-Methanation for Organic Waste: The CSIR–Indian Institute of Chemical Technology (CSIR-IICT) has developed a high-rate bio-methanation technology tail..
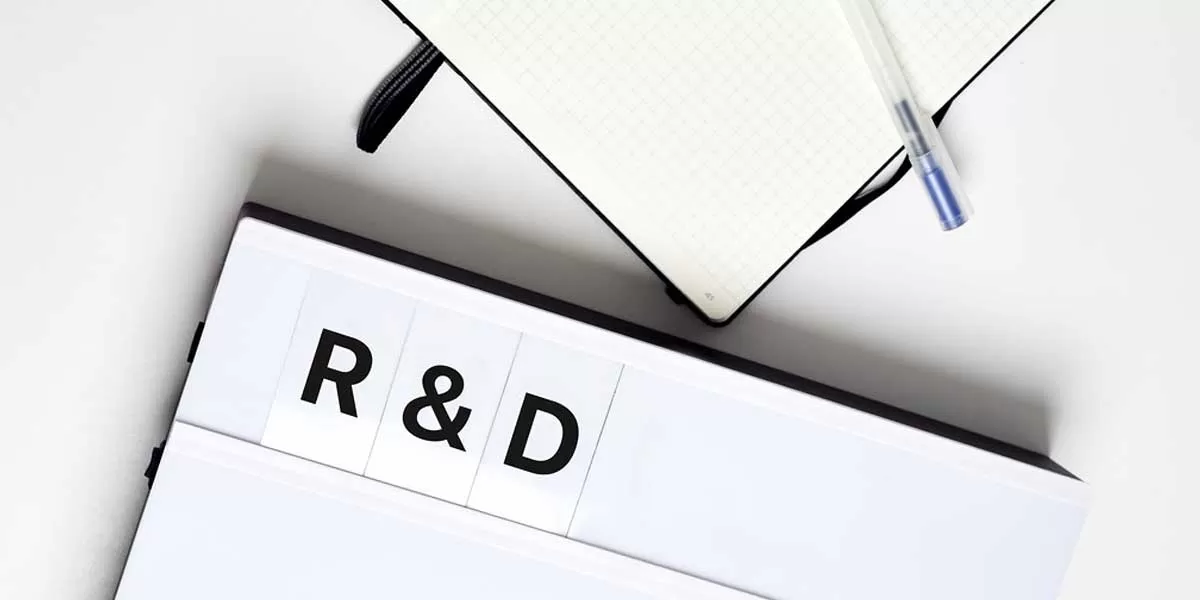
India Sets Up Anusandhan Foundation to Boost National Research
In a landmark move to strengthen India’s scientific research and innovation ecosystem, the Government has established the Anusandhan National Research Foundation (ANRF) under the ANRF Act, 2023, which was officially notified in February 2024. The foundation is designed to mobilise and manage significant funding across multiple streams for research and development activities across the country. The ANRF will receive financial support through various dedicated streams—the ANRF Fund, Innovation Fund, Science and Engineering Research Fund, and Special Purpose Funds. A budgetary provision of R..
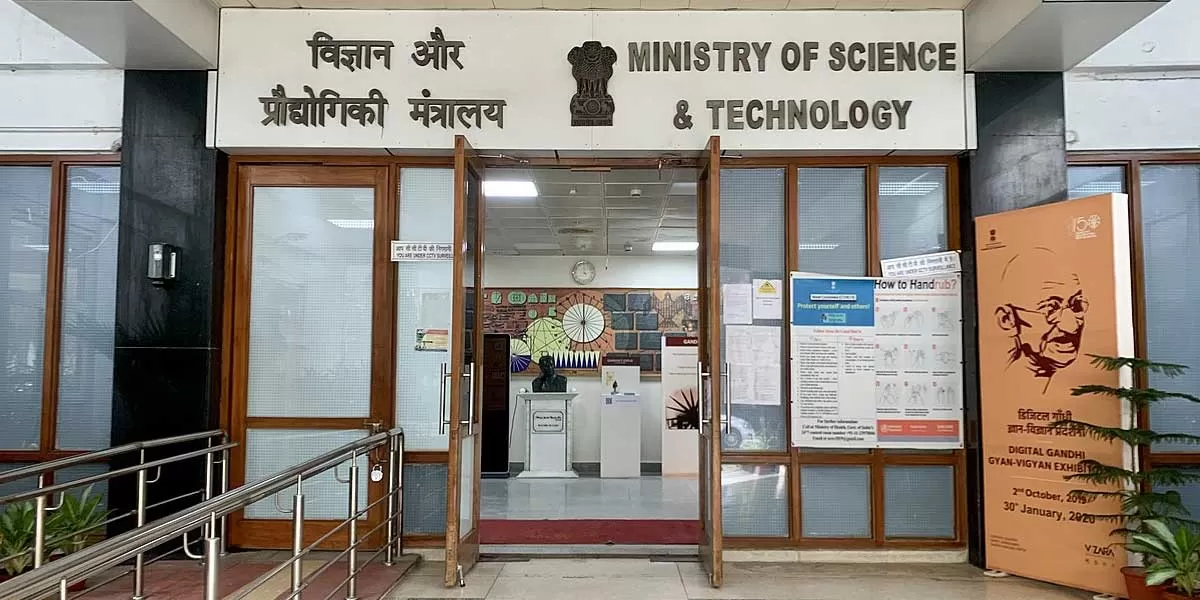
DST Clarifies Media Reports on State Science Policy Responses
The Department of Science and Technology (DST) has issued a clarification concerning recent media reports alleging a contradiction in its responses to Parliamentary questions regarding the first Indian state to implement a science policy. The department emphasised that the two queries raised in 2022 and 2025 differed in both scope and intent, and that the replies provided were accurate and aligned with the specific questions posed. In response to a Parliamentary Question dated 21 July 2022, which sought to ascertain whether any state government had ever initiated a science policy since Indiaâ..