- Home
- Infrastructure Energy
- COAL & MINING
- Environmentally sustainable mining practices in India
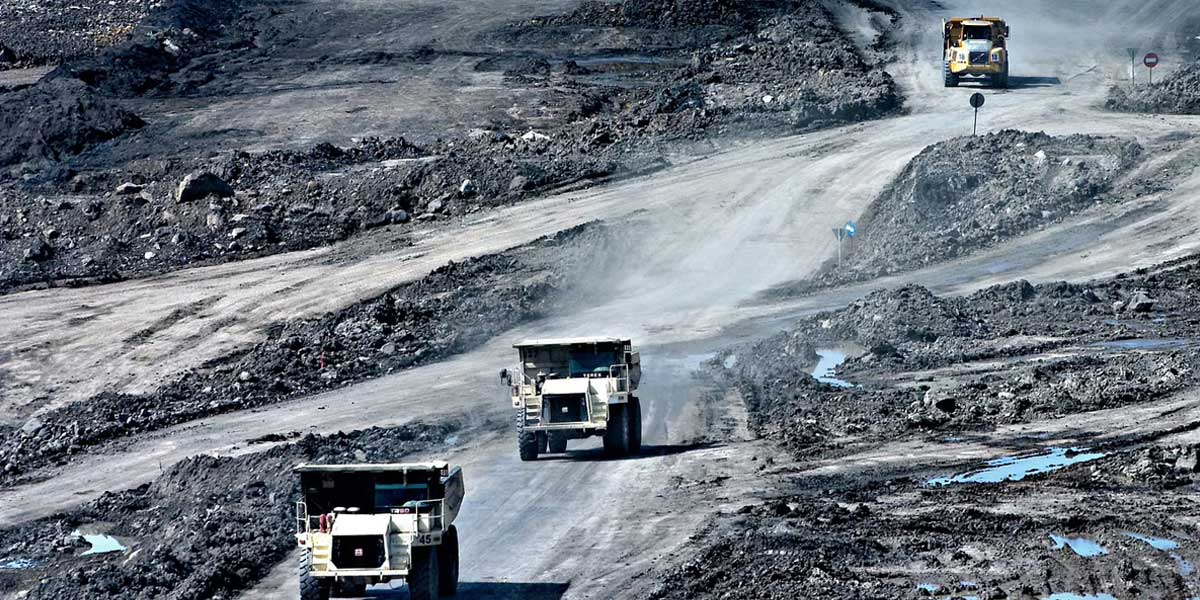
Environmentally sustainable mining practices in India
For original, visit Indian Cement Review
Bhanu Prakash Bhatnagar takes a closer view of mining practices around the world and reviews the New Mineral Policy 2019.
Come up with better regulations and legislation: As observed by the Honourable Supreme Court in its judgement on mining in 2017, the present mining legislation that we have today is far from being effective or productive. Mining continues to affect the environment because companies never cease to take advantage and continue polluting environment by waste discharges. Regulation obviously differs from country to country, with some countries more advanced in terms of their legislation than others. However, the need for improvement is always there in this industry, which inevitably causes some environmental damage.
We have to learn a lot from other countries like, for example Canada, where mines like the Island Copper Mine on Vancouver Island stands as a highly regulated mine site that is operational from 1971 to 1995 when it was closed for resource depletion. It was forced by regulatory agencies and control of the government that a detailed mine closure plan was developed to comfortably close the mine in order to protect the few resources which remained, and the Mine enacted the contaminated sites regulation process which was awarded the Certificate of Conditional Compliance.
This step involves the effective framing of the mineral policy and as we found that the new Mineral Policy 2019 advocates for the stringent laws for environmentally sustainable mining practices.
Effective implementation of this policy will not only protect environmental and public health, but also improve the lifespan of the mining industry and provide sustainable mining. The new Mineral Policy elaborates that extraction of mineral impacts other natural resources like land, water, air and forest. It is necessary to take a comprehensive view to facilitate the choice or order of land use keeping in view of the needs of development as well as needs of protecting the forests, environment and ecology and to conserve biodiversity of areas to be mined.
The New Mineral Policy has also emphasised on the effective mine closure where once the resources in mine are completely exhausted there is need for scientific mine closure which will not only restore ecology and regenerate bio-diversity but also take into account the socio-economic aspects of such closure. Government has a role in ensuring that post production mine decommissioning and land reclamation are an integral part of mine development process. Consistent approaches are adopted for efficient and effective mine reclamation and rehabilitation. Investing in R&D of environmentally sustainable mining technology: Mining industry is always in need of proper research and development in order to make sure the industry is ready for today’s ever-changing commitment to sustainability and turning the world into a more “environmentally sustainable’ place.
New Mineral Policy has emphasised on “scientific methods of mining” which state that the mine development and mineral conservation, as governed by the rules and regulations, will be on sound scientific basis, with the regulatory agencies like IBM and state directorates, closely interacting with R&D organisation and scientific and professional bodies. This is to ensure the proper mining practices being followed by mining companies. Policy advocates for R&D effort shall be made to improve efficiency in process, operation and also the recovery of by-products and reduction in specification and consumption norms. R&D efforts shall be directed to find new and alternative uses for minerals whose traditional demand is on the wane.
In this regard, as per the latest News published by NCCBM (NCB News, Sept 2019), the NCCBM has achieved great success with recent research and development with Investigation of standardisation of new clinker for blended cement. The objective of the study was to investigate effects of high MgO clinker on performance characteristics of resultant OPC, PPC and PSC. The project was undertaken on accelerated mode and the report to be submitted to BIS is under preparation. The main agenda was to promote utilisation of low-grade limestone containing higher MgO with good result. This will certainly result in increase of mine life.
Reduce resources inputs for effective mining practices: The mining industry consumes large amount of water and land in their operations. One solution to becoming more environmentally sustainable is to reduce the input of the mine. By diverting surface water and pumping groundwater, mines can reduce both the quantity and quality of water available downstream for aquatic ecosystems and other use.
With regard to energy, a mining company can look into alternative energy sources such as solar or wind power. By reducing the energy usage, a mine can reduce greenhouse gases and extend the life of fossil fuel reserves. Mining companies will also be able to reduce the cost to produce the product and thus reduce the cost of the commodity itself. The New Mineral policy advocates for minimising the inputs for mining processes.
Improving the efficiency of mining processes: This step is very much in discussion globally for closely monitoring the standard mining supply chain, mining industry/companies will be forced to confront ways in which a company can improve its efficiency where its lacking in terms of sustainability and green mining initiatives, improving the efficiency of this process can help trim down environmental impact. This also allows companies to regulate processes which may be inadequate in terms of environmental friendliness.
This needs a proper supervision of the mining and ancillary process that will allow mining companies to change elements/activities that are inefficient or that use too many natural resources. Conducting a material flows analysis will effectively track the physical flows of natural resources through extraction, production, fabrication, use, recycling and final disposal. This will develop new ways of thinking, new metrics, business process re-engineering and new management/supervisory tools that will help cushion the transition into more efficient and less environmental toxic patterns of resource used in modern societies. This process change will allow supervisors to develop new processes that are more efficient and sustainable than previous ones.
Across the world, organisations like the World Resources Institute (WRI) are currently conducting research on most frequently used resources and materials, in order to better understand how the industry can conserve its non-renewable materials. The WRI has been working towards developing a database, and can now indicate the flow of materials through industrial economies. Material flows analyses, as mentioned above, will track the physical flows of natural resources in every step of mining process, accounting for both the gains and losses occurring throughout the supply chain.
The New Mineral Policy mentions that the use of equipment and machinery, which will improve the efficiency, productivity and economics of mining operations as well as mineral beneficiation process, safety, health of persons working in mines/beneficiation plant and surrounding area shall be encouraged.
Re-evaluating cut-off grades: A raw mill cut-off grade is the level set that is considered to be the lowest quality of already mined ore which is economically feasible to continue processing. Different materials have different properties that determine a feasible cut-off grade. Often these grades are set at over-conservative levels. The easiest way to improve efficiency in mining and to reduce waste products is to decrease the mill cut-off grade of the mine. Re-evaluating these grades at each mine will significantly reduce waste. A lower mill cut-off grade may decrease the quality of the material, but certain final uses of the material do not need a very pure compound. Cut-off grades will be determined on a mine-by-mine basis by looking at the precedents for the material in question and taking the future use of the material into consideration.
For example, the above mentioned recent R&D study done by NCCBM, has very encouraging results in terms of re-evaluating the MgO (Magnesia) content in Limestone for Clinker manufacturing, which earlier assumed to be less than 3.5 per cent. Three types of high MgO clinker samples were obtained and designated as Clinker-1 (MgO~6.2 per cent), Clinker-2 (MgO~6.8 per cent) and Clinker-3 (MgO~7.5 per cent).
PPC & PSC got succeeded in Clinker-1 & Clinker-2 in all respect, while testing with OPC autoclave expansion was observed. The performance results obtained so far are quite encouraging which will pave the way for utilization of low grade limestone containing high MgO, increased mine life (approximately 15 years) besides improved sustainability during cement manufacture. This will also add to the utilisation of waste material of mine, thus leading to sustainable mining practices.
Replenishing the environment: A seemingly simple step, but it is rarely prioritized, replenishing mine sites and mine environment is one of the key factors to not only earning respect and cooperation of those living surrounding the mine site, but it will also ultimately protect the mine’s impact on the environment. Mining companies sometimes overlook the importance of replenishing the environment. This simple act can go a long way towards increasing the environmental sustainability of mining.
It has simple solutions like replenishing native soils and grasses, cleaning excess waste, proper waste removal, site inspections, replanting trees and natural forestry. By restoring the environment around the mine, the mining companies are contributing to positive environmental change, rather than making the environment more difficult to live in. The entire mine reclamation process should combine removal of hazardous materials, reshaping land, restoring topsoil, and planting native grasses, trees or ground cover natural to the site.
The New Mineral Policy emphasized that all mining shall be undertaken within the parameters of a comprehensive Sustainable Development Framework which will ensure that environmental, economic and social considerations are integrated effectively in all decisions of mines and mineral issues. The Guiding principal shall be that a miner shall leave the mining area in an ecological shape which is as good as it was before the commencement of mining or better with least impact on flora and fauna of the area.
Improving environmental performance: It is well known fact that mining activity impacts the environment in unnatural ways, which not only disrupts its natural decaying process, but also does more damage long-term than natural erosion processes. With exorbitant numbers of materials excavated and used daily, it is important to see that this destruction is actually going towards productive use.
This step is basically emphasised on adopting new measures useful in mitigating these environmental impacts. Let’s push for a systematic framework that will help us monitor the environmental performance.
We have to adopt practice of systematically examining environmental impacts and adopting measures to mitigate these impacts, it is possible to make mining less destructive to the environment. Incremental efficiency gains will not do the job. Instead, an imaginative remaking of the industrial world-one that aligns economies with the natural environment that supports them is the sustainable way forward.
The New Mineral Policy has given thrust on the sustainable development in mining sector by way of advising Government to set a benchmark against which all mining operations may be evaluated in terms of their comparative performance on Sustainable development framework and enforce commitment on part of mining companies to adopt sustainable development practices for achieving environmental and social goals.
Proper waste disposal: Correct waste disposal is vital to curbing the environmental impact of mines, as some mining companies do not dispose of their waste according to the guidelines. Companies can invest in equipment that helps in turning waste into reusable material, as well as adopting policies that allow for a more eco-friendly waste disposal routine.
Water can be reused on mining sites as grey water for washing equipment or flushing staff toilets. Mining companies should aim to reuse and recycle water as much as possible, and be sure that all unusable water is disposed of safely and responsibly. Scrap materials can be recycled or sold to companies who can reuse them in order to reduce the amount of waste produced on site. Recent study of NCCBM for increasing MgO content in clinker will substantially reduce the waste material in limestone mine, which contains high MgO% in it. Similarly, more emphasis has been given by Government of India for increasing use of AFR in Cement industries to touch a target of 25 per cent TSR basis.
Reduce outputs: Mining produces materials such as solid waste, mine water and air particles, all of which vary in their makeup and potential for environmental contamination. Waste management plans are required in order to prevent soil, air and water pollution. These plans are also in place to appropriately store the large volumes of waste produced at mine sites.
To reduce waste output, mines can look at using sustainable equipment. Much of the modern equipment used today is intended towards being environmentally friendly. Using cleaner production techniques, environmental control technologies, waste as raw material and process re-engineering are other ways to reduce the waste output of mines.
Few small steps during mining operations to achieve sustainable mining: These steps suggests below that mining companies shall consider during planning the mine development and production, for achieving environmentally sustainable mining process:
Dust suppression processes: It is known fact that the mining process, generates large amounts of dust into the atmosphere. This mineral dust be minimized by pre-wetting the areas to be blasted with high volume sprinklers. Once the dust is air-borne, it can be subsided by mist cannons. Current mines using open pit mining techniques can reduce dust through by purchasing high volume sprinklers and wet earth fog cannons. (Dust Suppression Solutions, 2003). The material, which was a pollution, can be added to the production and thereby reduces waste also.
Mining from tailings: Mill tailings contains metal contents, which can be mined, thus reducing waste and increasing productivity also. Reprocessing these wastes can result in more usable material.
Improved diesel engines for mining machinery: We know that the fuel cost is a major element in total cost of mine. Improving upon the latest technology diesel engines, which are highly efficient in fuel consumption, will not only save the cost but also reduces pollution level to maximize efficiency. (Green Mining Initiative, 2012).
Liquid membrane emulsion technology: This is a separation technique that can be used to extract usable metal from highly toxic or acidic waste water produced by a mine. This technology can even deal with dilute solutions (Venezuela, Araneda, Vargas, Basualto, and Sapag, 2009).
Impermeable tailings storage: Tailings are often stored in some form of tailings pond. Radioactive elements in this pond can pollute the water and if leaks occur, the surrounding area. Tailings will be required to be stored in impermeable tailing ponds. These ponds become impermeable by adding a layer to the boundaries that does not let liquid through. Alternatively, the tailings can be dehydrated into a paste, as done by Molycorp, China. Molycorp’s tailing process was reported to cost approximately $10 million (Molycorp Annual Report, 2011).
It is not possible for all mines to adopt above processes, however, every mine owner and company will be encouraged to do so. This will effectively reduce the pollution and thereby environmentally sustainable mining possible. New mines to be opened up will be required to fulfil a commitment towards reduction in pollution as well as the minimising effect to nearby areas.
The Mineral Policy suggest that to reduce the pollution, carbon footprint and operational costs, use of renewable sources of energy at mining sites will be encouraged through appropriate incentives. Appropriate sensitisation training about environmental issues will be provided to all workers involved in mining operations.
Say no to mining: This is harsh step suggested that we have to find alternative to mining activities, which a very difficult step. Since mining activities affects every part of our life by way of providing natural resources used in all material around us.
Every mining company is well aware of the devastating effects mining has on the environment. That is the reason why today they are trying so hard to safeguard the environment by providing the same goods and services to consumers using less metal, wood, plastic, stone and other materials. The goal is to reduce the mining impact on an international scale by encouraging the production of durable products that can be recycled, reused, or re-manufactured.
Precedents of effective environmental sustainability with a case study
The New Mineral Policy has mentioned the effective measures can be adopted to improve environmental sustainability of mining operations and also to improve the health and environment of surrounding areas of mining. This calls for “out of the box approach”, which includes above mentioned steps, which have been implemented around the world in various countries and positive results are achieved. Case study of China is elaborated below, where few steps adopted and results can be seen.In China, till 2010, mining facilities in China, especially for Rare earth minerals mining, were almost completely unregulated in terms of environmental consciousness and efficiency. After years of relax regulation and undisciplined treatment of illegal, unpermitted mines, China’s government responded to a wave of public protest and “partly in its own self-interest” enacted new policy measures set by the Ministry of Industry and Information Technology for environmentally sustainable mining. These were codified in the Rare Earth Industrial Development Policy (Schuler, Buchert, Liu, Dittrich&Merz, 2011).
The following regulations are the most important out of those now in practice. They are being enforced to discourage illegal and environmentally careless mining. These are cited from the Oko Institute’s Study on Rare Earths and Recycling.
From 2009 to 2015, China will not issue any new mining licences for rare earths.
Efforts to shut down illegal mines and inefficient separating and smelting enterprises will continue.
Increased monitoring of the industry will be done by the Ministry of Industry and Information Technology.
Requirements for an efficient electricity supply and specifications concerning the maximum energy demand per ton of rare earths produced are also indicated.
Minimum recycling rate for ore dressing waste water of mixed rare earth minerals (85 per cent) and Bastnae site and ion adsorption deposits (90 per cent) are set, as well as yield rates (92 per cent).
Pure monazite (one of the main sources of REEs) mining has been banned because of its high concentration of radioactivity.v Bastnae site, one of the two main minerals used for rare earth extraction, should be extracted with a treatment system that can completely treat wastewater and solid wastes for toxic and radioactive elements.
In-situ leaching mining has been introduced as the required mining method for those new mines that can physically implement this technology.
Saponification, a step of the refining process that leaves the wastewater highly toxic, can be improved through a newly discovered method that eliminates the need for ammonia. All mines will transfer to this process to minimise the toxicity of the wastewater.
Fluorine containing solid wastes should not be mixed with other waste products during disposal so as to reduce the contamination of the other, potentially reusable waste products.
Vegetation surrounding the mined areas must be rehabilitated to minimise the change in the surroundings caused by the mine. This will also make the community around the mine more habitable. (Schuler, Buchert, Liu, Dittrich & Merz, 2011).
These measures have not all been fully implemented, but China has set a ten-year timeline so that by 2020 they are fully enforced. Already, one third of China’s 23 mines have been identified as mines to be shut down (Volgt, 2012). China has also increased funding for research of different leaching-extraction processes, new uses for stockpiled cerium, recycling of wastewater, and more effective ways to recover fluorine and thorium. Although China’s past environmental regulation was severely lacking, its proposal protocol for reducing harm to the environment, if followed, would reduce waste at many mine sites, as it addresses some of the most common causes of mining-related waste.
Conclusion
It is conclusive that by adopting sustainable mining practices, new and current mining projects are expected to incorporate the lessons from past mining activities and thus solve their detrimental collateral effects on environment and public health, and bad name associated with mining can be removed. It needs sufficient efforts are to be taken toward changing legislation to ensure that the mining companies who are damaging the environment are punished appropriately, to make a significant impact. Examples of steps taken by China (case study) and have shown the results to world mining companies.EIA of mining projects should encompass the entire life cycle of the mine, should incorporate the assessment of negative impacts and societal benefits also, and must incorporate the liability and the cost and thus make funding provisions timely for post mining environmental rehabilitation.
New Mineral Policy 2019 included the impact statement as the success of the same will be critical in propelling India on to a loftier development trajectory. Successful implementation of this policy and shall be ensured by achieving a national consensus among various key stakeholders and their commitment to fulfil its underlying principles and objectives.
Mining laws and legal and technical capacity still need to be enhanced in order to include new internationally recommended good mining practices. The good signs about this are that responsible mining companies tend to adopt sustainable development goals (SDGs) and ensure that present and future generations will have resources or alternative means to satisfy their basic needs of food, water, and energy, every mining companies should look into using sustainable equipment and waste disposal procedures. They should also consider replenishing the local environment as often as possible, which will make the surrounding area habitable and able to return to a natural state once the mine has closed.
Reducing both input and output of the mining process can also help to reduce the negative impact that mines have on the environment. This implies that metal recycling must increase and alternative sources of energy must be tapped in order to decrease environmental impacts and depletion of conventional energy resources.
This article has been reproduced from CEMENT, ENERGY AND ENVIRONMENT, a Bi-Annual journal of Cement Manufacturers Association of India in its July-December 2019 Issue. Part II of the same will be published in the next month.
This is part 2 of the article, part 1 was published in the last edition.
Also read: Global mining outlook “stable”
Also read: We are in the final stages of mining reforms: Pralhad Joshi
For original, visit Indian Cement ReviewBhanu Prakash Bhatnagar takes a closer view of mining practices around the world and reviews the New Mineral Policy 2019. Come up with better regulations and legislation: As observed by the Honourable Supreme Court in its judgement on mining in 2017, the present mining legislation that we have today is far from being effective or productive. Mining continues to affect the environment because companies never cease to take advantage and continue polluting environment by waste discharges. Regulation obviously differs from country to country, with some countries more advanced in terms of their legislation than others. However, the need for improvement is always there in this industry, which inevitably causes some environmental damage. We have to learn a lot from other countries like, for example Canada, where mines like the Island Copper Mine on Vancouver Island stands as a highly regulated mine site that is operational from 1971 to 1995 when it was closed for resource depletion. It was forced by regulatory agencies and control of the government that a detailed mine closure plan was developed to comfortably close the mine in order to protect the few resources which remained, and the Mine enacted the contaminated sites regulation process which was awarded the Certificate of Conditional Compliance. This step involves the effective framing of the mineral policy and as we found that the new Mineral Policy 2019 advocates for the stringent laws for environmentally sustainable mining practices. Effective implementation of this policy will not only protect environmental and public health, but also improve the lifespan of the mining industry and provide sustainable mining. The new Mineral Policy elaborates that extraction of mineral impacts other natural resources like land, water, air and forest. It is necessary to take a comprehensive view to facilitate the choice or order of land use keeping in view of the needs of development as well as needs of protecting the forests, environment and ecology and to conserve biodiversity of areas to be mined. The New Mineral Policy has also emphasised on the effective mine closure where once the resources in mine are completely exhausted there is need for scientific mine closure which will not only restore ecology and regenerate bio-diversity but also take into account the socio-economic aspects of such closure. Government has a role in ensuring that post production mine decommissioning and land reclamation are an integral part of mine development process. Consistent approaches are adopted for efficient and effective mine reclamation and rehabilitation. Investing in R&D of environmentally sustainable mining technology: Mining industry is always in need of proper research and development in order to make sure the industry is ready for today’s ever-changing commitment to sustainability and turning the world into a more “environmentally sustainable’ place. New Mineral Policy has emphasised on “scientific methods of mining” which state that the mine development and mineral conservation, as governed by the rules and regulations, will be on sound scientific basis, with the regulatory agencies like IBM and state directorates, closely interacting with R&D organisation and scientific and professional bodies. This is to ensure the proper mining practices being followed by mining companies. Policy advocates for R&D effort shall be made to improve efficiency in process, operation and also the recovery of by-products and reduction in specification and consumption norms. R&D efforts shall be directed to find new and alternative uses for minerals whose traditional demand is on the wane. In this regard, as per the latest News published by NCCBM (NCB News, Sept 2019), the NCCBM has achieved great success with recent research and development with Investigation of standardisation of new clinker for blended cement. The objective of the study was to investigate effects of high MgO clinker on performance characteristics of resultant OPC, PPC and PSC. The project was undertaken on accelerated mode and the report to be submitted to BIS is under preparation. The main agenda was to promote utilisation of low-grade limestone containing higher MgO with good result. This will certainly result in increase of mine life. Reduce resources inputs for effective mining practices: The mining industry consumes large amount of water and land in their operations. One solution to becoming more environmentally sustainable is to reduce the input of the mine. By diverting surface water and pumping groundwater, mines can reduce both the quantity and quality of water available downstream for aquatic ecosystems and other use. With regard to energy, a mining company can look into alternative energy sources such as solar or wind power. By reducing the energy usage, a mine can reduce greenhouse gases and extend the life of fossil fuel reserves. Mining companies will also be able to reduce the cost to produce the product and thus reduce the cost of the commodity itself. The New Mineral policy advocates for minimising the inputs for mining processes. Improving the efficiency of mining processes: This step is very much in discussion globally for closely monitoring the standard mining supply chain, mining industry/companies will be forced to confront ways in which a company can improve its efficiency where its lacking in terms of sustainability and green mining initiatives, improving the efficiency of this process can help trim down environmental impact. This also allows companies to regulate processes which may be inadequate in terms of environmental friendliness. This needs a proper supervision of the mining and ancillary process that will allow mining companies to change elements/activities that are inefficient or that use too many natural resources. Conducting a material flows analysis will effectively track the physical flows of natural resources through extraction, production, fabrication, use, recycling and final disposal. This will develop new ways of thinking, new metrics, business process re-engineering and new management/supervisory tools that will help cushion the transition into more efficient and less environmental toxic patterns of resource used in modern societies. This process change will allow supervisors to develop new processes that are more efficient and sustainable than previous ones. Across the world, organisations like the World Resources Institute (WRI) are currently conducting research on most frequently used resources and materials, in order to better understand how the industry can conserve its non-renewable materials. The WRI has been working towards developing a database, and can now indicate the flow of materials through industrial economies. Material flows analyses, as mentioned above, will track the physical flows of natural resources in every step of mining process, accounting for both the gains and losses occurring throughout the supply chain. The New Mineral Policy mentions that the use of equipment and machinery, which will improve the efficiency, productivity and economics of mining operations as well as mineral beneficiation process, safety, health of persons working in mines/beneficiation plant and surrounding area shall be encouraged. Re-evaluating cut-off grades: A raw mill cut-off grade is the level set that is considered to be the lowest quality of already mined ore which is economically feasible to continue processing. Different materials have different properties that determine a feasible cut-off grade. Often these grades are set at over-conservative levels. The easiest way to improve efficiency in mining and to reduce waste products is to decrease the mill cut-off grade of the mine. Re-evaluating these grades at each mine will significantly reduce waste. A lower mill cut-off grade may decrease the quality of the material, but certain final uses of the material do not need a very pure compound. Cut-off grades will be determined on a mine-by-mine basis by looking at the precedents for the material in question and taking the future use of the material into consideration. For example, the above mentioned recent R&D study done by NCCBM, has very encouraging results in terms of re-evaluating the MgO (Magnesia) content in Limestone for Clinker manufacturing, which earlier assumed to be less than 3.5 per cent. Three types of high MgO clinker samples were obtained and designated as Clinker-1 (MgO~6.2 per cent), Clinker-2 (MgO~6.8 per cent) and Clinker-3 (MgO~7.5 per cent). PPC & PSC got succeeded in Clinker-1 & Clinker-2 in all respect, while testing with OPC autoclave expansion was observed. The performance results obtained so far are quite encouraging which will pave the way for utilization of low grade limestone containing high MgO, increased mine life (approximately 15 years) besides improved sustainability during cement manufacture. This will also add to the utilisation of waste material of mine, thus leading to sustainable mining practices. Replenishing the environment: A seemingly simple step, but it is rarely prioritized, replenishing mine sites and mine environment is one of the key factors to not only earning respect and cooperation of those living surrounding the mine site, but it will also ultimately protect the mine’s impact on the environment. Mining companies sometimes overlook the importance of replenishing the environment. This simple act can go a long way towards increasing the environmental sustainability of mining. It has simple solutions like replenishing native soils and grasses, cleaning excess waste, proper waste removal, site inspections, replanting trees and natural forestry. By restoring the environment around the mine, the mining companies are contributing to positive environmental change, rather than making the environment more difficult to live in. The entire mine reclamation process should combine removal of hazardous materials, reshaping land, restoring topsoil, and planting native grasses, trees or ground cover natural to the site. The New Mineral Policy emphasized that all mining shall be undertaken within the parameters of a comprehensive Sustainable Development Framework which will ensure that environmental, economic and social considerations are integrated effectively in all decisions of mines and mineral issues. The Guiding principal shall be that a miner shall leave the mining area in an ecological shape which is as good as it was before the commencement of mining or better with least impact on flora and fauna of the area. Improving environmental performance: It is well known fact that mining activity impacts the environment in unnatural ways, which not only disrupts its natural decaying process, but also does more damage long-term than natural erosion processes. With exorbitant numbers of materials excavated and used daily, it is important to see that this destruction is actually going towards productive use. This step is basically emphasised on adopting new measures useful in mitigating these environmental impacts. Let’s push for a systematic framework that will help us monitor the environmental performance. We have to adopt practice of systematically examining environmental impacts and adopting measures to mitigate these impacts, it is possible to make mining less destructive to the environment. Incremental efficiency gains will not do the job. Instead, an imaginative remaking of the industrial world-one that aligns economies with the natural environment that supports them is the sustainable way forward. The New Mineral Policy has given thrust on the sustainable development in mining sector by way of advising Government to set a benchmark against which all mining operations may be evaluated in terms of their comparative performance on Sustainable development framework and enforce commitment on part of mining companies to adopt sustainable development practices for achieving environmental and social goals. Proper waste disposal: Correct waste disposal is vital to curbing the environmental impact of mines, as some mining companies do not dispose of their waste according to the guidelines. Companies can invest in equipment that helps in turning waste into reusable material, as well as adopting policies that allow for a more eco-friendly waste disposal routine. Water can be reused on mining sites as grey water for washing equipment or flushing staff toilets. Mining companies should aim to reuse and recycle water as much as possible, and be sure that all unusable water is disposed of safely and responsibly. Scrap materials can be recycled or sold to companies who can reuse them in order to reduce the amount of waste produced on site. Recent study of NCCBM for increasing MgO content in clinker will substantially reduce the waste material in limestone mine, which contains high MgO% in it. Similarly, more emphasis has been given by Government of India for increasing use of AFR in Cement industries to touch a target of 25 per cent TSR basis. Reduce outputs: Mining produces materials such as solid waste, mine water and air particles, all of which vary in their makeup and potential for environmental contamination. Waste management plans are required in order to prevent soil, air and water pollution. These plans are also in place to appropriately store the large volumes of waste produced at mine sites. To reduce waste output, mines can look at using sustainable equipment. Much of the modern equipment used today is intended towards being environmentally friendly. Using cleaner production techniques, environmental control technologies, waste as raw material and process re-engineering are other ways to reduce the waste output of mines. Few small steps during mining operations to achieve sustainable mining: These steps suggests below that mining companies shall consider during planning the mine development and production, for achieving environmentally sustainable mining process: Dust suppression processes: It is known fact that the mining process, generates large amounts of dust into the atmosphere. This mineral dust be minimized by pre-wetting the areas to be blasted with high volume sprinklers. Once the dust is air-borne, it can be subsided by mist cannons. Current mines using open pit mining techniques can reduce dust through by purchasing high volume sprinklers and wet earth fog cannons. (Dust Suppression Solutions, 2003). The material, which was a pollution, can be added to the production and thereby reduces waste also. Mining from tailings: Mill tailings contains metal contents, which can be mined, thus reducing waste and increasing productivity also. Reprocessing these wastes can result in more usable material. Improved diesel engines for mining machinery: We know that the fuel cost is a major element in total cost of mine. Improving upon the latest technology diesel engines, which are highly efficient in fuel consumption, will not only save the cost but also reduces pollution level to maximize efficiency. (Green Mining Initiative, 2012). Liquid membrane emulsion technology: This is a separation technique that can be used to extract usable metal from highly toxic or acidic waste water produced by a mine. This technology can even deal with dilute solutions (Venezuela, Araneda, Vargas, Basualto, and Sapag, 2009). Impermeable tailings storage: Tailings are often stored in some form of tailings pond. Radioactive elements in this pond can pollute the water and if leaks occur, the surrounding area. Tailings will be required to be stored in impermeable tailing ponds. These ponds become impermeable by adding a layer to the boundaries that does not let liquid through. Alternatively, the tailings can be dehydrated into a paste, as done by Molycorp, China. Molycorp’s tailing process was reported to cost approximately $10 million (Molycorp Annual Report, 2011). It is not possible for all mines to adopt above processes, however, every mine owner and company will be encouraged to do so. This will effectively reduce the pollution and thereby environmentally sustainable mining possible. New mines to be opened up will be required to fulfil a commitment towards reduction in pollution as well as the minimising effect to nearby areas. The Mineral Policy suggest that to reduce the pollution, carbon footprint and operational costs, use of renewable sources of energy at mining sites will be encouraged through appropriate incentives. Appropriate sensitisation training about environmental issues will be provided to all workers involved in mining operations. Say no to mining: This is harsh step suggested that we have to find alternative to mining activities, which a very difficult step. Since mining activities affects every part of our life by way of providing natural resources used in all material around us. Every mining company is well aware of the devastating effects mining has on the environment. That is the reason why today they are trying so hard to safeguard the environment by providing the same goods and services to consumers using less metal, wood, plastic, stone and other materials. The goal is to reduce the mining impact on an international scale by encouraging the production of durable products that can be recycled, reused, or re-manufactured. Precedents of effective environmental sustainability with a case study The New Mineral Policy has mentioned the effective measures can be adopted to improve environmental sustainability of mining operations and also to improve the health and environment of surrounding areas of mining. This calls for “out of the box approach”, which includes above mentioned steps, which have been implemented around the world in various countries and positive results are achieved. Case study of China is elaborated below, where few steps adopted and results can be seen. In China, till 2010, mining facilities in China, especially for Rare earth minerals mining, were almost completely unregulated in terms of environmental consciousness and efficiency. After years of relax regulation and undisciplined treatment of illegal, unpermitted mines, China’s government responded to a wave of public protest and “partly in its own self-interest” enacted new policy measures set by the Ministry of Industry and Information Technology for environmentally sustainable mining. These were codified in the Rare Earth Industrial Development Policy (Schuler, Buchert, Liu, Dittrich&Merz, 2011). The following regulations are the most important out of those now in practice. They are being enforced to discourage illegal and environmentally careless mining. These are cited from the Oko Institute’s Study on Rare Earths and Recycling. From 2009 to 2015, China will not issue any new mining licences for rare earths. Efforts to shut down illegal mines and inefficient separating and smelting enterprises will continue. Increased monitoring of the industry will be done by the Ministry of Industry and Information Technology. Requirements for an efficient electricity supply and specifications concerning the maximum energy demand per ton of rare earths produced are also indicated. Minimum recycling rate for ore dressing waste water of mixed rare earth minerals (85 per cent) and Bastnae site and ion adsorption deposits (90 per cent) are set, as well as yield rates (92 per cent). Pure monazite (one of the main sources of REEs) mining has been banned because of its high concentration of radioactivity.v Bastnae site, one of the two main minerals used for rare earth extraction, should be extracted with a treatment system that can completely treat wastewater and solid wastes for toxic and radioactive elements. In-situ leaching mining has been introduced as the required mining method for those new mines that can physically implement this technology. Saponification, a step of the refining process that leaves the wastewater highly toxic, can be improved through a newly discovered method that eliminates the need for ammonia. All mines will transfer to this process to minimise the toxicity of the wastewater. Fluorine containing solid wastes should not be mixed with other waste products during disposal so as to reduce the contamination of the other, potentially reusable waste products. Vegetation surrounding the mined areas must be rehabilitated to minimise the change in the surroundings caused by the mine. This will also make the community around the mine more habitable. (Schuler, Buchert, Liu, Dittrich & Merz, 2011). These measures have not all been fully implemented, but China has set a ten-year timeline so that by 2020 they are fully enforced. Already, one third of China’s 23 mines have been identified as mines to be shut down (Volgt, 2012). China has also increased funding for research of different leaching-extraction processes, new uses for stockpiled cerium, recycling of wastewater, and more effective ways to recover fluorine and thorium. Although China’s past environmental regulation was severely lacking, its proposal protocol for reducing harm to the environment, if followed, would reduce waste at many mine sites, as it addresses some of the most common causes of mining-related waste. Conclusion It is conclusive that by adopting sustainable mining practices, new and current mining projects are expected to incorporate the lessons from past mining activities and thus solve their detrimental collateral effects on environment and public health, and bad name associated with mining can be removed. It needs sufficient efforts are to be taken toward changing legislation to ensure that the mining companies who are damaging the environment are punished appropriately, to make a significant impact. Examples of steps taken by China (case study) and have shown the results to world mining companies. EIA of mining projects should encompass the entire life cycle of the mine, should incorporate the assessment of negative impacts and societal benefits also, and must incorporate the liability and the cost and thus make funding provisions timely for post mining environmental rehabilitation. New Mineral Policy 2019 included the impact statement as the success of the same will be critical in propelling India on to a loftier development trajectory. Successful implementation of this policy and shall be ensured by achieving a national consensus among various key stakeholders and their commitment to fulfil its underlying principles and objectives. Mining laws and legal and technical capacity still need to be enhanced in order to include new internationally recommended good mining practices. The good signs about this are that responsible mining companies tend to adopt sustainable development goals (SDGs) and ensure that present and future generations will have resources or alternative means to satisfy their basic needs of food, water, and energy, every mining companies should look into using sustainable equipment and waste disposal procedures. They should also consider replenishing the local environment as often as possible, which will make the surrounding area habitable and able to return to a natural state once the mine has closed. Reducing both input and output of the mining process can also help to reduce the negative impact that mines have on the environment. This implies that metal recycling must increase and alternative sources of energy must be tapped in order to decrease environmental impacts and depletion of conventional energy resources.ABOUT THE AUTHOR:The article is authored by Bhanu Prakash Bhatnagar. He has completed B.E. Mining Engg. (Gold Medal), FCC, MBA, and has been working as Head Mining, Adani Cementation, Ahmedabad. He is having more than 27 years’ experience in overall mine management including acquisition of mineral resources through auction process, new mine development, production planning, mine operations and quality management for large opencast limestone mines. He had previously worked with cement companies like ACC-Holcim, Reliance Cement and has overseas mining experience. This article has been reproduced from CEMENT, ENERGY AND ENVIRONMENT, a Bi-Annual journal of Cement Manufacturers Association of India in its July-December 2019 Issue. Part II of the same will be published in the next month. This is part 2 of the article, part 1 was published in the last edition. Also read: Global mining outlook “stable” Also read: We are in the final stages of mining reforms: Pralhad Joshi
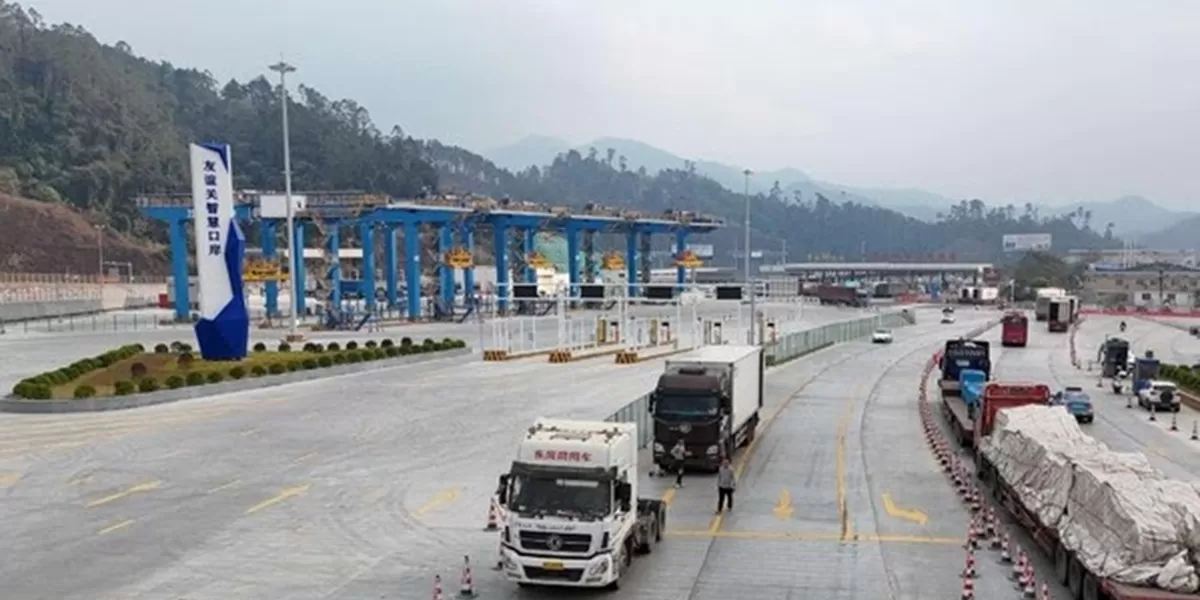
Smart Border Port Keeps Nonstop China-Vietnam Trade Flowing
On a recent spring morning at Youyiguan Port, known as Friendship Pass, on the China-Vietnam border in Pingxiang city, south China's Guangxi Zhuang autonomous region, a steady stream of trucks lined up at the border crossing, ferrying tropical fruits into China and hauling machinery and electronics to Vietnam. The scene is brisk, efficient - and increasingly automated. Friendship Pass, one of the largest and most efficient land border crossings between China and Vietnam, is undergoing a high-tech overhaul. The site is being transformed into China's first cross-border smart port, with the Chi..
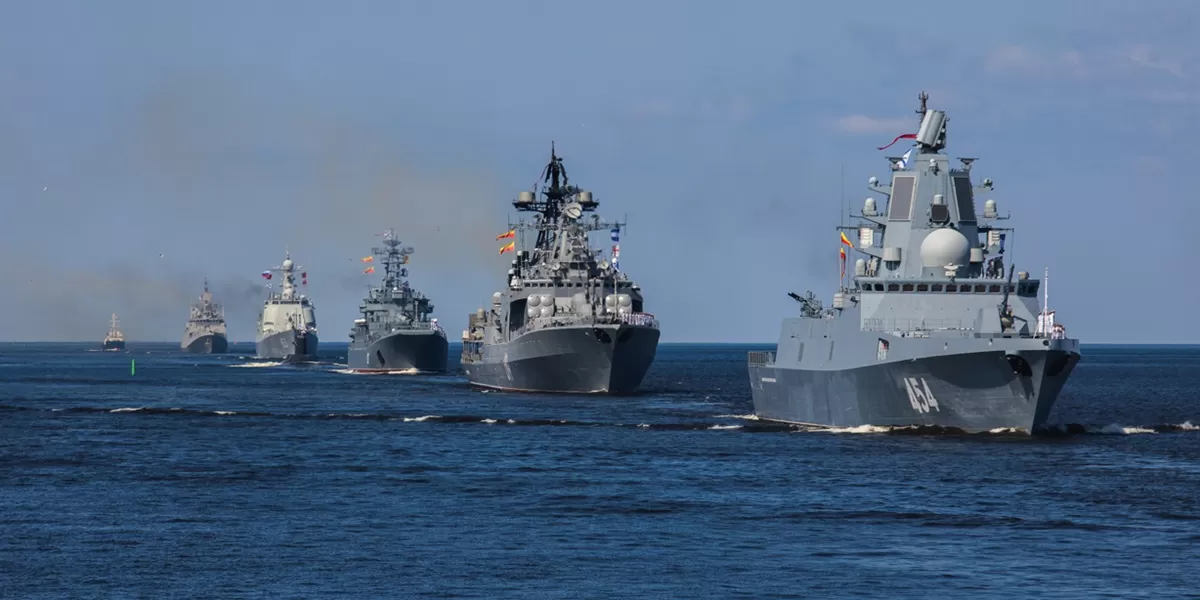
Cortec Delivers Corrosion Protection for Military Equipment and Infra
As modern military operations demand equipment that’s ready for immediate deployment, corrosion prevention has become more critical than ever. Addressing these challenges, Cortec® Corporation—an industry leader in environmentally responsible corrosion solutions—offers its proven VpCI® (Vapor phase Corrosion Inhibitor) technology to safeguard military equipment during production, transit, and long-term storage. Corrosion poses serious risks to o perational readiness, safety, and budgets. It can lead to critical equipment failures, costly repairs, and safety hazards. Studies indicate t..
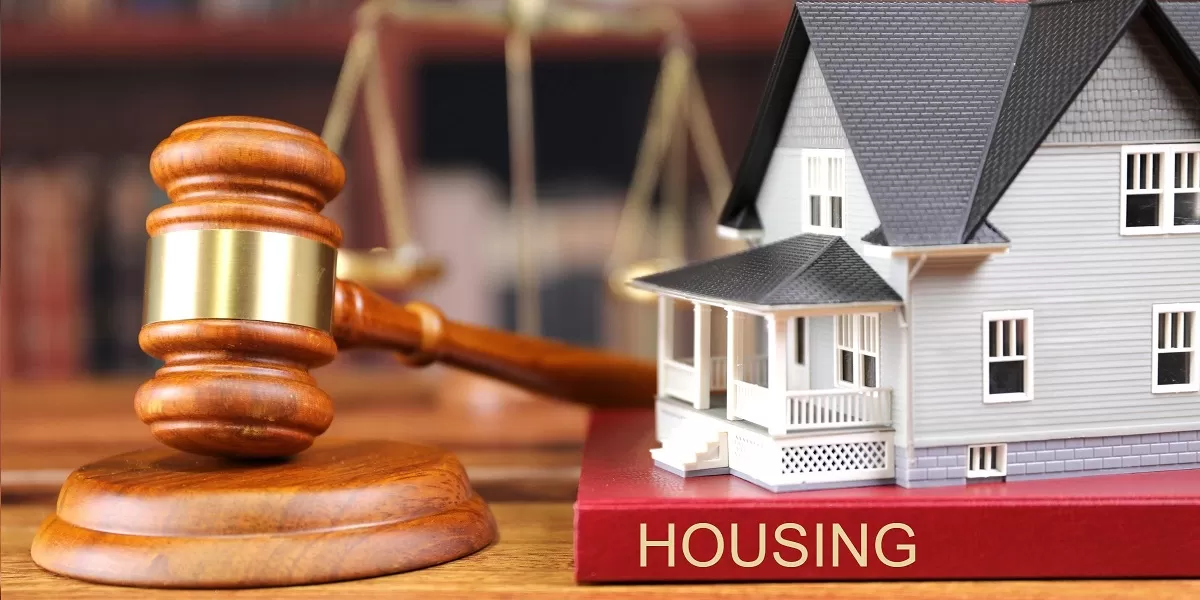
Unsold Affordable Housing Drops 19% in Q1 2025: ANAROCK
India’s housing market is showing contrasting trends across budget segments. According to the latest data from ANAROCK Research, unsold affordable housing units (priced below Rs 4 million) across the top seven cities dropped by 19% year-on-year in Q1 2025, falling from approximately 140,000 units to 113,000 units. This decline is attributed to restricted new supply and sustained demand from end-users. Conversely, unsold stock in the luxury housing segment (priced above Rs 15 million) surged 24% in the same period, growing from 91,125 units to over 1.13 lakh units. The spike comes on the bac..
Latest Updates
Recommended for you
Subscribe to Our Newsletter
Get daily newsletters around different themes from Construction world.
Advertisement
Advertisement
subscribe to the newsletter
Don't miss out on valuable insights and opportunities
to connect with like minded professionals