- Home
- Real Estate
- Phase-1 of the TCS Olympus Centre in Thane has been completed in a record 18 months as against the initial estimated 24 months. Here's how!

Phase-1 of the TCS Olympus Centre in Thane has been completed in a record 18 months as against the initial estimated 24 months. Here's how!
Heard of the single largest IT facility owned by a single company in the country? <br /> <br /> Tata Consultancy Services (TCS) is making headlines for its recently operational building Olympus Centre in Thane. And, remarkably, the Hiranandani Group completed Phase-1 of the project - which was inaugurated by Maharashtra Chief Minister Devendra Fadnavis - in a record 18 months as against the initial estimated 24 months! <br /> <br /> As <span style="font-weight: bold;">Dr Niranjan Hiranandani, Co-Founder and Managing Director, Hiranandani Group, </span>says, "What we have done is extraordinarily fantastic, setting a precedent in making speedy fast, good-quality buildings." <br /> <br /> With Hiranandani Group leasing out the space for 15 years, TCS can now boast of the single largest IT facility owned by a single company in the country. The TCS Olympus Centre is being developed in two phases spanning 2.3 million sq ft (18.5 lakh building + 5 lakh non-tower area), with the potential to accommodate 30,000 employees once fully operational. Construction of the project began in January 2016 and was completed in an astounding 18 months - the facility is now operational across 2 million sq ft of commercial space, housing 25,000 employees.<br /> <br /> <span style="font-weight: bold;">The USP</span><br /> TCS currently employs around 75,000 people in Maharashtra across Mumbai, Pune, Nagpur and Nashik. The TCS Olympus Centre is the latest addition to the company's unique global network of software development and delivery centres. Platinum rated by the Indian Green Building Council (IGBC), this new, state-of-the-art facility has been developed as a green campus and features rainwater harvesting, a sewage treatment plant (STP), and eco-friendly, low-emission systems and fixtures. It includes a training block, club house and gymnasium, thus providing a contemporary and holistic work culture. <br /> <br /> In terms of corporate relocation and workforce enlargement, this ambitious commercial project is a key driver for residential demand within the township on outright as well as rental housing. Consolidating operations across Mumbai into this new facility will also create more indirect employment opportunities in the Greater Mumbai area.<br /> <br /> <span style="font-weight: bold;">Challenges and solutions</span><br /> A major concern involved the one-of-its-kind consolidation plan to relocate over 25,000 employees spread over 20+ offices to one unified campus. "The campus definition was that of a millennial's workplace, of which Phase-1 was to initially house 14,000+ employees," says <span style="font-weight: bold;">Cyrus K Pithawalla, Director, Engineering, Hiranandani Constructions. </span><br /> <br /> "To successfully complete construction in a record 18 months, pioneering technologies were used and global best construction materials leveraged."<br /> Pithawalla highlights other major challenges faced and the efficient solutions offered by Hiranandani Constructions: <br /> <br /> <ul> <li>Challenge 1: In this project, the spans are large, loading is heavy and the floor height requirement was a challenge. The solution: To solve these technical issues, high-strength concrete was chosen for columns and PT slabs, making the structure more efficient.</li> <li>Challenge 2: The sizes and spacing of heavily loaded columns and shear walls were restricted, thus demanding a high grade of concrete. The solution: Considering the heavy loads, a high grade of concrete was chosen. After extensive in-house R&D and trials with locally available raw materials, M70 was successfully developed and used, ensuring the required strength and durability by using mineral admixtures and high PC-based super plasticisers, thus helping the architect to get more working floor space.</li> <li>Challenge 3: The biggest challenge in the construction industry is shortage of skilled manpower. Construction is a labour-oriented industry and thus a project's timeline is affected if skilled manpower in sufficient number is not ensured. The solution: Continuous training and proper organisational set-up of contractors and vendors to ensure minimum turnover of labour were ensured.</li> <li>Challenge 4: Coordination and synchronisation of various activities and vendors. The solution: Regular on-site meetings and site visits were organised to ensure smooth progress of work without any major holdups.</li> <li>Matching up to every challenge, this project is not only an example of fast-track completion but engineering best practices.</li></ul><br /> <span style="font-weight: bold;">Green concrete </span><br /> The utilisation of mineral admixtures such as fly-ash and ground-granulated blast-furnace slag (GGBFS) is one of the most important features of the construction of this project, making high-performance concrete green and more durable for coastal environments like Mumbai and Thane. "The use of about 200 metric tonne (mt) of mineral admixtures has definitely helped protect our environment, too, apart from improving the durability of the structure," avers Pithawalla. <br /> <br /> The large quantity of concrete and rebar (reinforcing bar) used in this project offers an idea of the magnitude of the project size - concrete of about 115,380 cu m and rebar of about 7,864 mt has been used for the building and non-tower area in this project.<br /> <br /> <span style="font-weight: bold;">Energy-efficient façade</span><br /> The selection of the façade is vital from the energy-efficiency perspective. And so, high-performance glass, sourced from Saint Gobain, has been selected for the windows and façade. "The high performance helps reduce heat ingress from outside, thus reducing the load on air-conditioning," says Pithawalla.<br /> <br /> <span style="font-weight: bold;">Landscape and STP</span><br /> The landscape area at the TCS Olympus Centre-1 includes a podium area of 1,520 sq m and ground area of 4,000 sq m with 620 trees planted in the campus. "We have spruced up our construction area with landscape area to create a lively environment," avers Pithawalla. "Further, we are among the pioneers in developing and introducing an STP in our projects. Today, it has become necessary from the point of view of helping the environment and reducing the load on important natural resources like water." The total sewage generated from the building will be 740,000 litre per day; this will be reused for flushing, gardening and the cooling tower. Moreover, the project has constructed an elevated water storage reservoir (ESR). <br /> <br /> <span style="font-weight: bold;">The unique syphonic system</span><br /> The drainage of large roof areas is becoming an even more important task in modern residential, industrial, commercial and high-rise construction. The use of a syphonic system on the terrace is something unique to this project. It helps the discharge of rainwater from large areas in the most efficient manner. Frequent and heavy rainfall necessitates efficient waste and drainage systems so that even large quantities of water can be drained off safely. "The systems are hydraulically optimised, such that the discharge rate is practically double than that of conventional systems with the same pipe dimension," says Pithawalla. He lists the advantages of the syphonic system: Fewer roof outlets owing to high discharge rate; increased flexibility when planning owing to fewer stacks; and maximum use of the space, thanks to horizontal pipelines without slopes.<br /> <br /> <span style="font-weight: bold;">Electrical systems</span><br /> It is imperative that such a prestigious project has sufficient power supply considering its functional use. "The demand-supply situation was studied and the power requirement and available options of fulfilling the requirement were worked out accordingly," says Pithawalla. Also, a first state-of-the-art 220 kV GIS (gas-insulated switchgears) substation in the MSEDCL Thane Circle was constructed and commissioned by Hiranandani. <br /> <br /> It has a capacity of 40 MVA and is built with the latest technology in EHV switchgears. All controls and monitoring are undertaken through the SCADA (supervisory control and data acquisition) system. The project was completed in all respects, from the start to power release with required approvals. <br /> <br /> <span style="font-weight: bold;">QA systems</span><br /> Stringent third-party testing was undertaken for important materials such as rebar, fly-ash, etc. Further, detailed method statements, procedures, standard operating procedure (SOP), manuals in the form of handbooks, guides and PPTs were well-defined for every important activity. Also, according to Pithawalla, "All ductility detailing has been followed with total precision to ensure earthquake-resistance. Regular and frequent internal technical audits were carried out to check and correct processes and any deviations." Dowel anchors took care of uplifting pressure on the basement raft slab. And lightweight concrete has been used in a few areas to reduce the total dead weight of the structure.<br /> <br /> <span style="font-weight: bold;">Multipurpose hall</span><br /> Having a multipurpose hall (MPH) on the terrace is another standout feature in this project. With a capacity for 800 people, this MPH has a unique roof detailing. <br /> "The roofing consists of two layers of 50-mm thick glass wool of 32 kg per sq m density, vapour barrier and 12.5-mm gyproc sheet sandwiched between colour-coated galvalume sheets," elaborates Pithawalla, adding that the top sheet is white in colour, which further reduces heat ingress, thus reducing the air-conditioning load. Even the walls are made acoustic-efficient by introducing insulation between cavities of double-wall masonry.<br /> <br /> <span style="font-weight: bold;">Committed and concerted effort</span><br /> A project of this scale requires a huge team working in concert and with complete commitment. TCS Olympus Centre had 110 engineers working on it, including 100 contractors. <br /> <br /> Further, it involved about 900 labourers (400 skilled + 500 unskilled) per day. <br /> This magnificent building stands testament to their efforts!<br /> <br /> <span style="font-weight: bold;">Quick Glimpse<br /> Area: </span>14.5 acre <br /> <span style="font-weight: bold;">Tower 1:</span> G + 15 storeys with two basements <br /> <span style="font-weight: bold;">Floor plate:</span> 3 acre per floor approximately<br /> <span style="font-weight: bold;">Grid structure:</span> 12 m x 12 m<br /> <span style="font-weight: bold;">Slab:</span> Post tension<br /> <span style="font-weight: bold;">Floor load:</span> 600 kg per sq m<br /> <span style="font-weight: bold;">Construction area:</span> 2.3 million sq ft<br /> <span style="font-weight: bold;">Application for building permission:</span> August 31, 2015<br /> <span style="font-weight: bold;">Commencement certificate issued:</span> November 19, 2015<br /> <span style="font-weight: bold;">Ground breaking and excavation:</span> November 19, 2015<br /> <span style="font-weight: bold;">Commencement of foundation work of building:</span> January 28, 2016<br /> <span style="font-weight: bold;">World-class IT building of 16 storey + 2 basements:</span> Completion by June 6, 2017<br /> <span style="font-weight: bold;">Application for occupation certificate (OC):</span> June 6, 2017<br /> <span style="font-weight: bold;">Occupation certificate issued:</span>July 5, 2017<br /> <br /> <br /> <span style="font-weight: bold;">Speaking at the inauguration of the TCS Olympus Centre..</span><br /> Maharashtra Chief Minister Devendra Fadnavis, said, "This is a real example of how fast Indian developers can work. We have often heard of buildings in China being built in 12 to 18 months. We used to wonder how. But in the case of the TCS Olympus Centre, all approvals were sought in less than 60 days. Also, such a huge facility has been built in just 18 months with state-of-the-art workplaces supported by new technologies and one-of-its-kind innovation. Such facilities are important considering the demographic power of India, with 50 per cent of the population being below 25 years of age and embracing technology that innovates. The state government and TCS have come together for more investments in innovation and all that is required. We have formed a committee to finalise the Fintech quality to have a formal Fintech ecosystem being developed in Mumbai." <br /> <br /> <span style="font-weight: bold;">Rajesh Gopinathan, CEO and Managing Director, Tata Consultancy Services (TCS), </span>said, "TCS has played a pioneering role to make Maharashtra an attractive IT destination for global companies. We have helped drive technology-led growth by investing in the talented youth of the state and building long-term partnerships with state institutions. We are delighted to launch our new next-gen workplace, which provides collaborative agile workspaces, a software-defined network, security operations centre and cloud-enabled infrastructure. The facility will help TCS further drive the next phase of its growth."<br /> <br /> <span style="font-weight: bold;">Unmatched Amenities<br /> <br /> HIGH DENSITY<br /> <br /> Arrivals</span><br /> <ul> <li>Security check at security block</li> <li>Separate arrival zone for pedestrian traffic through a specially designed tunnel </li> <li>Company buses drop-off zone: Rear side of the ground floor entrance hall </li> <li>Own vehicles: Screening at entrance gate to the basement through the ramps.</li></ul><br /> <span style="font-weight: bold;">Vertical transportation</span><br /> <ul> <li>6 + 12 (high-speed) elevators earmarked for two zones</li> <li>2 VIP elevators + 2 service elevators</li> <li>2 car parking elevators.</li></ul><br /> <span style="font-weight: bold;">Escalators</span><br /> <ul> <li>Security block; entrance hall; cafeteria.</li></ul><br /> <span style="font-weight: bold;">UTILITIES<br /> Utility block</span><br /> <ul> <li>G + 2 storey structure to house </li> <li>Chillers, DG, transformers </li> <li>Underground diesel tanks.</li></ul><br /> <span style="font-weight: bold;">EHV substation</span><br /> <ul> <li>220 kv substation to provide 20-MW power established in 12 months.</li></ul><br /> <span style="font-weight: bold;">AMENITIES</span><br /> <ul> <li>2 squash courts; 2 badminton courts; indoor board games; gymnasium; library; open green areas; podium greens; pargolas, features, water fountains, vertical gardens. </li></ul><br /> <span style="font-weight: bold;">CAFETERIA/KITCHEN</span><br /> <ul> <li>Mega kitchen capacity to meet 4,000 covers in one sitting</li> <li>Cafeteria spread over two floors, interconnected with escalators and internal staircase</li> <li>Multipurpose hall on rooftop for 800 seats</li> <li>Executive dining on rooftop.</li></ul><br /> <span style="font-weight: bold; font-family: arial,helvetica,sans-serif arial,helvetica,sans-serif; font-size: 12pt;">"Our aim was to go beyond what the contract envisaged."</span><br /> <br /> Evidently, this project for TCS is another jewel in the Hiranandani crown. Beaming with pride, <span style="font-weight: bold;">Dr Niranjan Hiranandani, Co-Founder and Managing Director, Hiranandani Group, shares...</span><br /> <br /> "Having occupied about 3-4 lakh sq ft space in Hiranandani Powai, TCS had approached us, citing its requirement of setting up another centre in Mumbai. The contract envisaged that we would complete this building of 2 million sq ft with car parks within 24 months. TCS is an IT giant and wanted a building that would suit its requirements. <br /> <br /> It also wanted the project to be completed at the earliest - this is probably one of the fastest buildings of its size - 16 storeys with two basements - done by our company. We took on the challenge, got the approvals of the buildings as per the design and took up the architectural work in-house. Our proposed design was happily approved by TCS and we got going. I feel extremely proud as I say that this is the 56th building we have completed in three years' time together in Thane. Now, the question was whether we could complete this building faster than what TCS expected, and that is exactly what we did! Our aim was to go beyond what the contract envisaged and go beyond targets and expectations. We achieved all of this and more. So, we have built this building against the most competitive bid; we have done a quality job with no compromises whatsoever with speed, efficiency and efficacy; and the entire turnout has been a service provision to the satisfaction of the client. Over the years, the unemployment ratio has increased in Thane, especially with the shutting down of several factories. But today, with projects of this nature coming up in Thane, we are confident of bringing back employment opportunities."<br /> <br /> <span style="font-weight: bold;">-Shriyal Sethumadhavan & Seraphina D'souza</span><br />
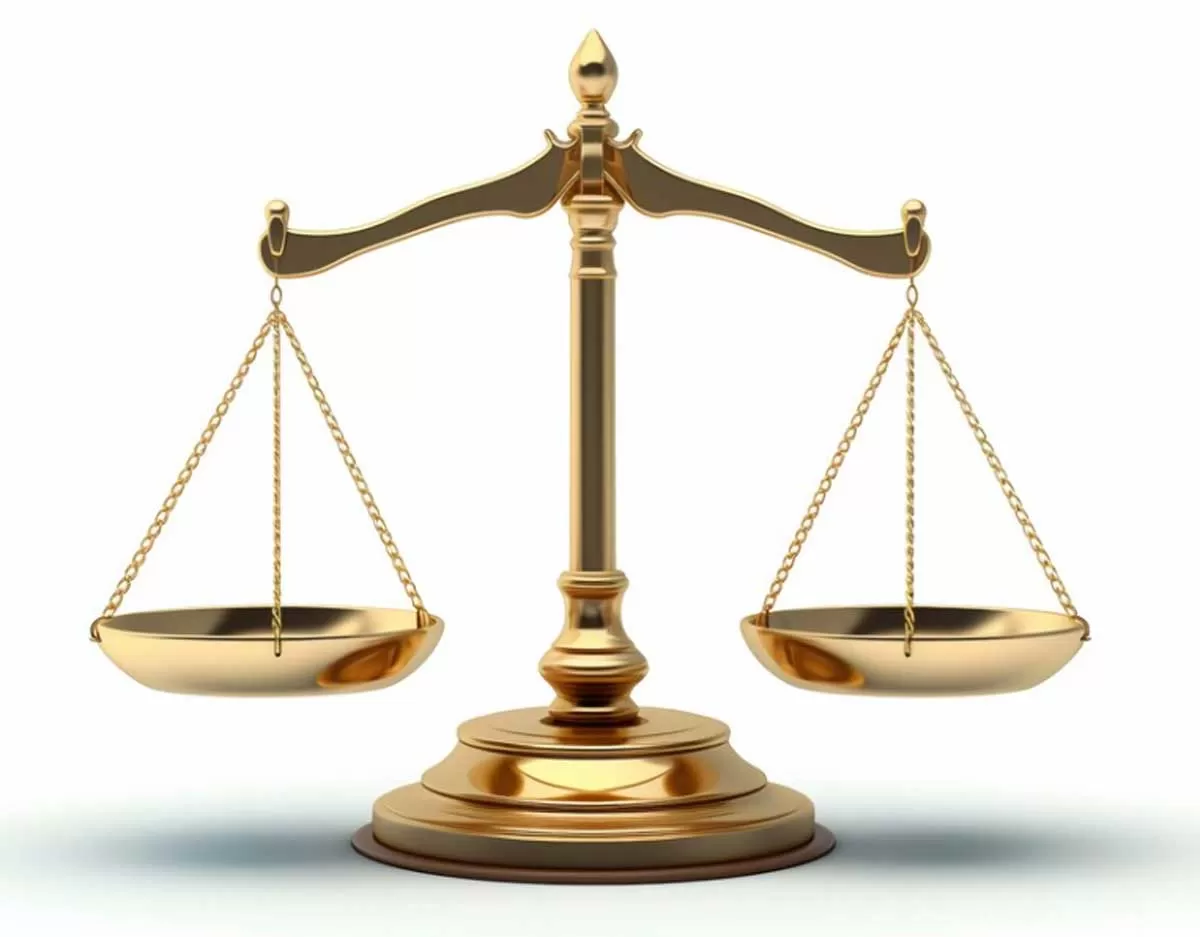
Development of ICT in Indian Judiciary through e-Courts Phases
The eCourts project, launched under the National eGovernance Plan in 2007, is a Mission Mode Project aimed at modernisng the Indian judiciary through the adoption of Information and Communication Technology (ICT). The initiative is grounded in the "National Policy and Action Plan for Implementation of ICT in the Indian Judiciary" and has been implemented in multiple phases. Phase I (2011–2015) focused on the computerization of judicial infrastructure and ensuring connectivity across courts. During this phase, 14,249 district and subordinate courts were computerised, and Local Area Networks ..
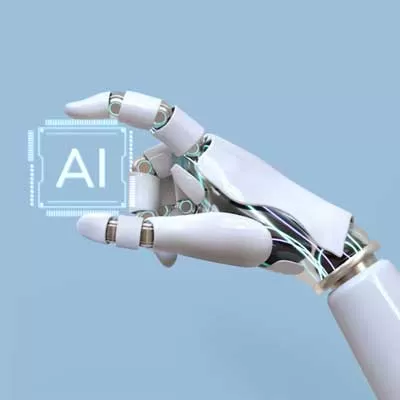
Minority Affairs Minister to Launch PM VIKAS Project via DGSMC
On 29th March 2025, the Ministry of Minority Affairs will launch a new program under the Pradhan Mantri Virasat Ka Samvardhan (PM VIKAS) scheme, aimed at enhancing skill development and educational support for minority communities. The initiative, which will be implemented by the Delhi Sikh Gurdwara Management Committee (DSGMC), will benefit a total of 31,600 candidates across the country. Out of the total beneficiaries, 29,600 individuals will receive skill training in industry-relevant fields, while 2,000 candidates will receive educational support. The training will focus on job roles ali..
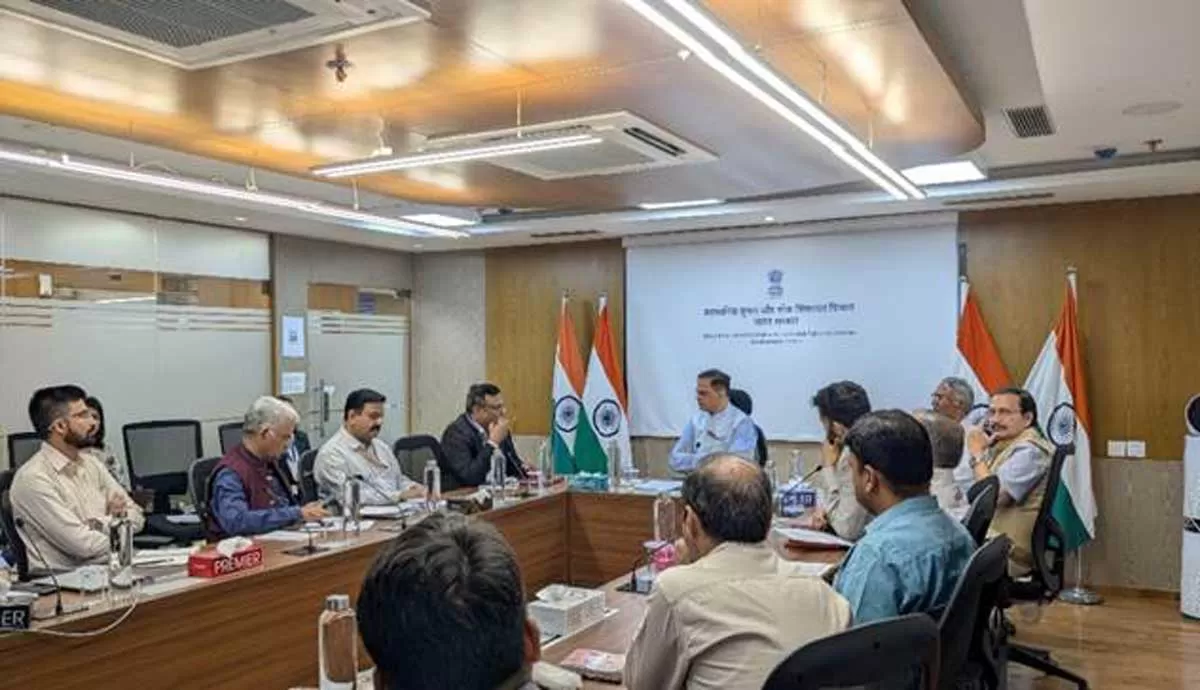
DARPG and Bhashini Launch Multilingual Tool for Citizen Grievances
To enhance the effectiveness, accessibility, and responsiveness of the grievance redressal system, the Department of Administrative Reforms and Public Grievances (DARPG) has signed a Master Service Agreement with Digital India Bhashini on March 28, 2025. This agreement marks the implementation of a multimodal, multilingual e-Governance solution for the Centralised Public Grievance Redress and Monitoring System (CPGRAMS), in line with the directive of the Prime Minister of India to bring qualitative improvements to citizen service delivery. The new solution aims to empower citizens from diver..
Latest Updates
Recommended for you
Subscribe to Our Newsletter
Get daily newsletters around different themes from Construction world.
Advertisement
Advertisement
subscribe to the newsletter
Don't miss out on valuable insights and opportunities
to connect with like minded professionals