
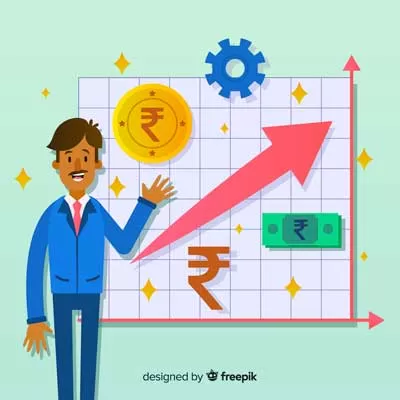
What Industry Wants!
The construction industry is gearing up for Budget 2025 with high expectations. As one of India’s key economic drivers, the sector is eagerly anticipating reforms and policies to address pressing challenges such as high input costs, funding gaps, and sustainability demands. Industry leaders across real estate, infrastructure, construction materials, and logistics have shared their wishlists, urging the government to focus on GST rationalization, increased CAPEX, and green initiatives.This year’s budget presents an opportunity for the government to not only tackle existing bottlenecks but a..
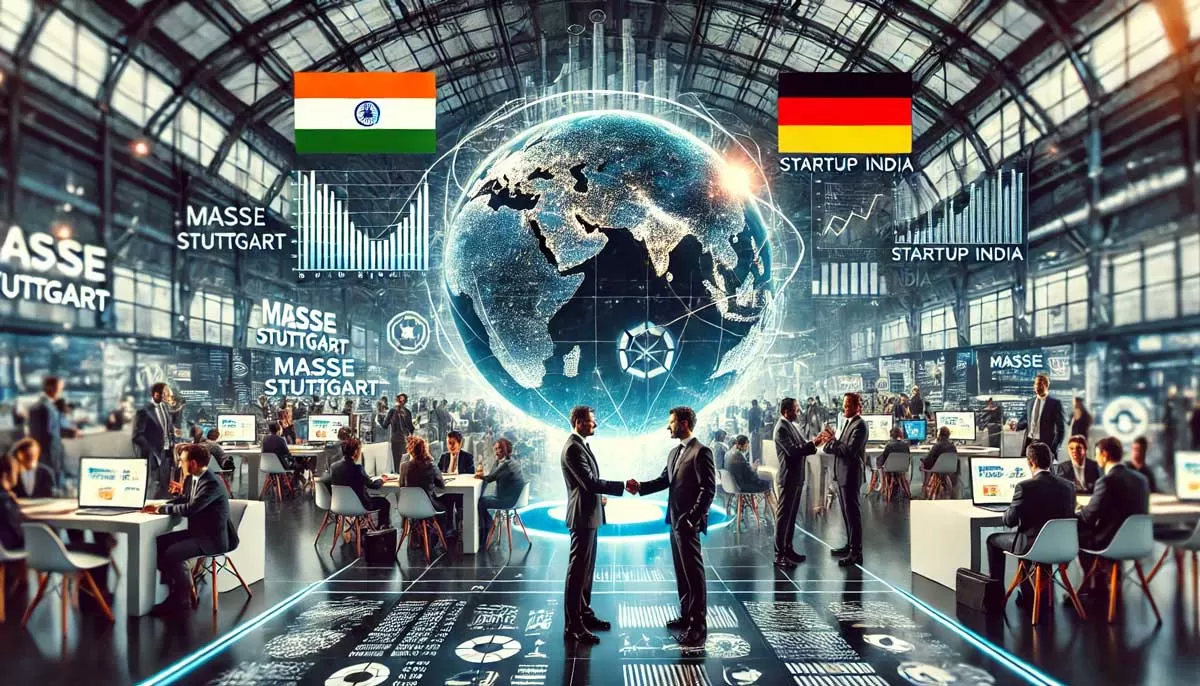
Messe Stuttgart, Startup India Tie-Up to Boost Funding
The logistics market in India is poised for significant growth, with a projected revenue of $357.3 billion by 2030. Despite this huge potential, a recent McKinsey & Company report highlights the decline in logistics funding following the pandemic that remains a significant concern. After receiving unprecedented funding of $25.6 billion in 2021, venture capital investment in logistics startups fell sharply to $2.9 billion in 2023—a nearly 90 per cent decrease, marking the lowest since 2015. This pullback from investors is attributed to several factors, including high interest rates, a glo..
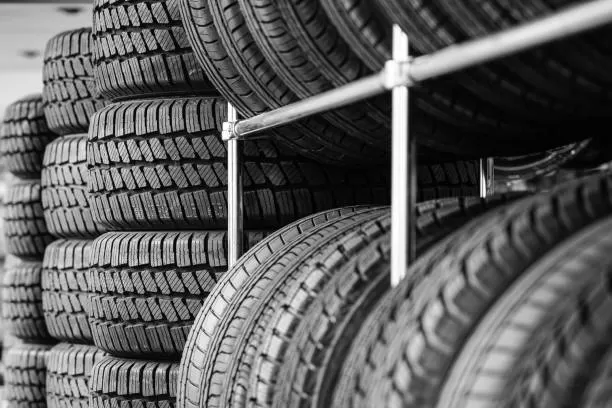
JK Tyre Strengthens Road Safety Commitment
Reinforcing its unwavering commitment to road safety, JK Tyre & Industries, a leader in the tyre manufacturing industry, partnered with the Delhi Traffic Police to organise a comprehensive Road Safety Awareness Week. This initiative, held as part of National Road Safety Month (January 1–31, 2025) spearheaded by the Ministry of Road Transport and Highways (MoRTH), aimed to foster responsible driving habits and reduce road accidents. Under the theme ‘Sadak Suraksha Jeevan Raksha,’ the initiative commenced on January 16, 2025, at the Delhi Police Traffic Training Park, BKS. The program feat..