- Home
- Building Material
- Cement
- Interview: Nilesh Narwekar, CEO, JSW Cement
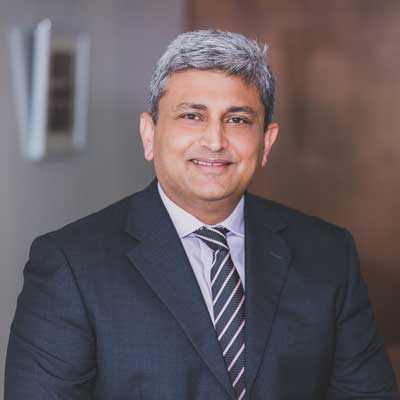
Interview: Nilesh Narwekar, CEO, JSW Cement
Speaking on the company’s key growth strategies, he adds, “At present, we have multiple brownfield projects underway across our plant locations, augmenting our production capacity for both clinkerisation and grinding sections. Additionally, we are implementing advanced WHRS (waste heat recovery system) and AFR (alternative fuel and raw materials) system to optimise operational efficiencies and minimise environmental impact. To fortify our presence in the eastern market, we successfully acquired Shiva Cement in Odisha and revamped its clinkerisation unit to 1.36 mtpa, which will play a pivotal role in supplying clinker to our Salboni and Jajpur grinding plants. We intend to make it an integrated plant.”
What are the key growth strategies or expansion plans that JSW Cement has for the future?
We have set our sights on becoming a formidable player & force to reckon with in the cement industry, driving growth and innovation that will propel us to new heights in the near future. We are already the World’s #1 eco-friendly cement company and our low-carbon products are setting new benchmarks in sustainable construction in India and across the globe. We cater to more than 12 states and 3 union territories of India from our 5800+ pan India strong dealer network served through two integrated and five grinding units. With our current production capacity nearing 19 million tons, we have set an audacious goal to reach 50 million tons by 2030. This ambitious growth shall be fuelled by a strategic combination of organic and inorganic approaches, ensuring a robust and sustainable trajectory. Our unwavering dedication has already established us as a significant market force in the southern, western, and eastern regions and now we have set our sights on capturing the highly lucrative northern market to close on our pan India presence.
At present, we have multiple brownfield projects underway across our plant locations, meticulously augmenting our production capacity for both clinkerisation and grinding sections. Additionally, we are implementing Waste Heat Recovery System (WHRS) and Alternative Fuel and Raw Materials (AFR) systems to optimise operational efficiencies and minimise environmental impact.
To fortify our presence in the eastern market, we successfully acquired Shiva Cement in Odisha, astutely revamped its clinkerisation unit to 1.36 million tons which would play a pivotal role in supplying clinker to our Salboni and Jajpur grinding plants. We intend to make it an integrated plant in near future.
Meanwhile, the brownfield capacity expansion projects at our Dolvi (enhanced grinding capacity by ~2 million tons) and Nandyal units (enhanced clinkerisation from 6500 tpd to 8500 tpd) are complete, and we eagerly anticipate commissioning of the additional 2 million tons grinding unit at Vijaynagar within the next 2-3 months. We further intend to add another 4 million tons grinding capacity to our Vijaynagar plant which would take its overall grinding capacity to 10 million tons per annum. Additionally, our joint venture unit in Fujairah is ramping up its clinkerisation capacity from 1 MTPA to 2.36 MTPA, further solidifying our growth trajectory.
As part of our strategic expansion into northern India, we have tactically acquired limestone mines in Nagaur, Rajasthan and Damoh, Madhya Pradesh. We have meticulously planned the establishment of clinkerisation and grinding units, alongside WHRS systems in these areas leading to a capacity addition of 10 million tons per annum. Currently, we are in advanced stages of land acquisition and obtaining statutory approvals for these Greenfield projects and expect the plants to come up in the next few years.
Apart from cement production pursuits, we are resolutely focused on expanding and scaling up our Ready-Mix Concrete (RMC) and construction chemical businesses. Our aim is to achieve a pan-India presence in these segments in the near future, capitalising on the vast array of opportunities they offer.
In addition to the above and in our quest for growth, we are actively exploring numerous other opportunities in the realm of inorganic expansion to consolidate and strengthen our position in the Indian cement market.
Can you provide insights into JSW Cement's research and development efforts and any innovations in the cement industry that the company has introduced?
We strongly believe in embracing a green environment, adopting circular economy principles, and pursuing decarbonisation. We have incorporated the same as a basic guiding force in whatever business pursuit we undertake and feel that our efforts would help create a more resilient and environmentally conscious society. As a part of our concerted action towards decarbonisation, we have established a dedicated research & development wing with the sole purpose of creating products that contribute to minimalistic carbon emission. We are already the world’s #1 eco-friendly cement company and our low-carbon products are setting new benchmarks in sustainable construction in India and across the globe. With an emission intensity of 220 Kg/ton that is 36 per cent of the global average (~600 Kg/ton) and 40 per cent of the national average (~540 Kg/ton), we have already positioned ourselves as a leader in the decarbonisation journey.
Our R&D team has been diligently researching different types of hazardous slag to develop building products that possess superior strength, have enhanced durability, are resistant to corrosive environments, are complaint and most importantly, contribute significantly less to carbon emissions. Our environment friendly brands such as Concreel HD, Power Pro, Portland Slag Cement, and Compcem (Composite cement), have widely been embraced in the market. We are actively working on LC3 cement, Super Sulphated Cement, and innovative methods to maximise utilisation of various slags such as AOD, EAF, and LD slag. A notable achievement in circularity and sustainability is the substitution of Al-laterite mineral with ladle furnace slag, a by-product of steel plants. This substitution not only reduces CO2 emissions through pre-calcined CaO but also provides a valuable source of Alumina, which serves as a mineral additive during clinkerisation.
We have also established partnerships with esteemed institutions to support our research and development centre. These include the FEhS Building Materials Institute in Duisburg, Europe and Eco Mister in Canada, who provide us with technological support. Additionally, we have been closely collaborating with renowned indigenous institutes such as IIT Delhi, IIT Bombay, IIT Guwahati, IIT Chennai, and IISc Bangalore. Through these collaborations, we are actively engaged in developing eco-friendly products and exploring innovative interventions that promote sustainability.
Over the past few years, our R&D team has made significant progress in patenting slag-based cementitious products. With more than six patents already filed and several more in the pipeline, we are committed to driving innovation in the field. Notably, we have recently collaborated with IIT Roorkee to develop a patent for manufacturing eco-friendly and biodegradable cement bags, demonstrating our commitment to sustainable practices.
In line with our commitment to eco-friendly practices, even our construction chemicals portfolio is developed using industrial wastes, ensuring that our products align with sustainable principles. One notable addition to our product line up is Slag Sand, a revolutionary substitute for conventional natural river sand, which is extensively used in concrete production. This innovative solution not only offers superior performance but also serves as a proven eco-friendly alternative. Further, by conserving river sand, we are also contributing to reduce ecological impacts which are caused by river sand mining.
Our efforts in promoting a clean and green environment have not gone unnoticed. We have been honoured with numerous awards and accolades, recognising our contribution towards environmental preservation. In a recent achievement on June 23, we were awarded by the Ministry of Steel for our significant role in decarbonisation within the steel and cement industry. These recognitions inspire us to continue our mission of making the world a cleaner and healthier place to live.
Through ongoing research, development, and collaborations, we remain steadfast in our pursuit of creating sustainable solutions and fostering a more environmentally conscious society.
How does JSW Cement prioritise sustainability and environmental responsibility in its operations?
JSW Cement, a part of the $23 billion JSW Group, is a leading global eco-friendly building materials company with a production capacity of 19 million tonnes per annum. Our business model is based on the philosophy of the circular economy. Despite cement production being energy-intensive and contributing to GHG emissions, we have achieved an impressive emissions intensity of only 220 kg/ton in FY22 (and bettered to 175 kg/ton in FY23), earning us the recognition as the "Greenest company" in terms of climate impact.
As a member of the Global Cement and Concrete Association (GCCA), we are committed to the GCCA's roadmap for achieving net-zero concrete by 2050. Over the past eight years, we have quadrupled our production while halving our emissions by utilising high clinker substitution, particularly with slag. Currently, 90 per cent of our product portfolio is slag-based, with two-thirds of our raw materials sourced from by-products and waste materials.
To achieve net-zero emissions, we are implementing strategies such as clinker substitution, using alternative fuels and raw materials, and increasing our clean and green energy portfolio. We blend clinker with supplementary materials like blast-furnace slag to produce blended cement, reducing carbon emissions. We aim to increase our use of alternative fuels and raw materials to over 30 per cent by 2030. Additionally, we are progressively incorporating solar power plants, Waste Heat Recovery Systems (WHRS), and renewable energy sources, targeting 50 per cent renewable power by 2030.
Our grinding plants utilise advanced technologies, prioritise energy productivity and produce high-quality blended cement products with superior properties. We also focus on water sustainability, aiming to reduce freshwater withdrawal intensity by 15 per cent and become 5 times water positive by 2030 through increased use of recycled and harvested water and implementing water stewardship programmes.
We are committed to preserving biodiversity and minimising our environmental impact. Our biodiversity management policy ensures minimal disturbance and we strive to achieve "No Net Loss" on biodiversity by 2030. We closely monitor and manage emissions to maintain air quality, exceeding regulatory limits. Our waste management follows the reduce-reuse-recycle approach, handling hazardous and non-hazardous waste appropriately. We prevent wastewater discharge outside our facilities to protect water bodies.
Finally, we prioritise social sustainability by empowering local communities, upholding human rights, promoting fair labour practices, improving living conditions, and prioritising health, safety, wellness, and diversity within our workforce.
What steps does JSW Cement take to ensure the quality and consistency of its cement products?
Our Research and Development (R&D) centre in Vijayanagar maintains the highest standards of quality and consistency. Both the R&D centre and our individual plant quality control laboratories are equipped with cutting-edge facilities, including the Robo Lab, X-Ray fluorescence and diffraction machines, Optical Microscope, Compressive strength testing machine, Isothermal calorimetry, On-Line control systems, and other advanced Wet Classical chemistry instruments. These state-of-the-art instruments play a crucial role in monitoring and controlling the entire process value chain, from the sourcing of raw materials to the production of the finished product.
To ensure the desired quality and consistency in our end products, we have meticulously developed specifications for various input raw materials such as Limestone, Laterite, Red mud, Steel slag, Flue dust, BF slag, Fly ash, Gypsum, and more. We employ regular sampling and chemistry determination techniques to effectively control the quality of these raw materials. Furthermore, we conduct meticulous assessments, including the determination of glass content in slag to ensure compliance with BIS standards, and microscopic analysis of different phases in the clinker to assess its quality and quantity.
In addition to mineralogical and chemical characterisation, we thoroughly evaluate the final clinker-based OPC and slag cement products for their physical properties, including setting time, normal consistency, expansion, Blaine fineness, and compressive strength. These evaluations are carried out to ensure that the finished product aligns with the specifications outlined by the BIS codes for the respective grades of cement.
To guarantee that both the raw materials and the finished product meet the acceptable specifications, we have developed standard operating procedures (SOPs) for various stages of quality assurance. These SOPs encompass crucial aspects such as sampling points, sampling frequency, identification of production batches, sample retention time, sample traceability, sample analysis time, and calibration of measuring and monitoring instruments. By adhering to these procedures, we maintain the consistency and reliability of our quality control processes.
To further strengthen our commitment to quality, we subject the clinker and finished products to periodic checks conducted by third-party organisations, as well as by regulatory body BIS. These external assessments are essential in ensuring that our products consistently meet the established standards.
Through the establishment of our advanced R&D centre, the implementation of stringent quality control measures, and the engagement of external verification, we demonstrate our unwavering dedication to delivering products of the highest quality. These initiatives enable us to meet the evolving demands of our customers while upholding the utmost standards of excellence in our industry.
How does JSW Cement ensure supply chain efficiency?
We have embarked on a ground-breaking digital revolution within our logistics operations, fuelled by a steadfast commitment to elevating service levels and mastering cost management. Our triumphant approach encompasses three formidable pillars: Process Monitoring, Movement Control, and Cost Optimisation, converging to deliver unparalleled outcomes.
To oversee the entire operation, from the moment an order is received until the materials are delivered to the customer, we employ a digital brain called the logistics control tower (LCT). The LCT utilises cutting-edge technologies such as RFID and GPS, and extensively leverages analytics to analyse the data and information collected.
Our Yard Management System (YMS) assists in aligning sales orders with available trucks in the parking yard and organizes their sequencing through various stages, from gate-in to invoicing.
For movement within our manufacturing plant, both inbound and outbound, we employ RFID tags and sensors. The Plant Logistics Management System (PLMS) enables us to monitor the internal movement of trucks within the plant, ensuring efficient control and avoiding congestion, thereby facilitating timely truck loading.
External movement occurs outside the plant, from the manufacturing plant to the customer and vice versa. This external movement is tracked using GPS, which monitors the truck's movement and stoppages. Whenever an abnormal stoppage occurs during outbound movement, the Logistics Control Tower is immediately alerted. This way, the LCT plays a crucial role in our Track N Trace system, acting as a monitoring mechanism for external movement. It escalates any issues to relevant internal and external stakeholders, minimising truck stoppages.
Cost optimisation, our ultimate objective, is achieved through tracking various logistics Key Performance Indicators (KPIs) using an analytics layer. Data from the PLMS, Track N Trace system, and ERP are integrated into a business intelligence platform, which then provides feedback to the LCT team round the clock. This continuous flow of information enables us to make necessary course corrections. By reducing the order-to-delivery time and order-execution time, we can increase the number of trips per truck, a crucial factor in negotiating favourable rates with transporters. We constantly refine our routes to determine the most optimal paths, resulting in scientifically accurate freight rates. Furthermore, we optimise our truck fleet size, matching it appropriately to each route at the right time, thereby achieving economies of scale.
Overall, our digitisation efforts have revolutionised our logistics operations, enhancing service levels, managing costs, and driving efficiency throughout the entire supply chain.
Can you share some insights into JSW Cement's approach to digital transformation and utilisation of technology in its processes?
Embracing the winds of change, we have embarked on a profound digitalisation voyage, permeating every aspect of our value chain. From raw material sourcing to production, logistics to customer engagement, and even beyond to our internal operations, we have harnessed the power of technology to reshape our company and redefine excellence. All of the above has been done with an objective of empowering our workforce to make smarter, quicker decisions by transforming data into an accessible and reusable asset.
Today, customers are digitally engaged and are more data conscious. They expect us to offer customised solutions that can be accessed on demand and can be seamlessly integrated into their lives. Digitalisation is helping us create new platforms to drive better engagement with our customers and other stakeholders, enhance our agility and creating greater efficiencies in our operations. In last couple of years, we have launched more than 12 apps and have carried out 20+ business process engineering initiatives which itself is a great testament of our focus towards digitalisation.
We are making great strides in digitalisation with JSW Aikyam, Saathi App, DGO App and NonTrade App along with state-of-the-art logistics control tower, which has helped us digitally track and control logistics movement across our value chain and enhance our overall efficiency.
The Smart JSW Saathi app has already proven to be a powerful catalyst for JSW sales promoter’s preferences and for deepening engagement. The platform helps sales promoters with placing orders, view order status, real-time tracking of their dispatches, online payment, real-time settlement and update of their outstanding, checking their financial books, collaborating with JSW departments through service requests, and downloading documents required in their day-to-day operations.
Through comprehensive digitisation, we have transformed our logistics operations across all manufacturing units, attaining a holistic view of the supply chain. RFID technology empowers us with complete visibility of trucks within our yards, allowing us to efficiently schedule loading and unloading processes, thus meeting targeted turnaround times. By optimising costs and planning truck routes, we navigate traffic seamlessly, while continuous tracking ensures driver safety and enables timely communication with transporters. Our logistics control tower, a state-of-the-art facility, operates round the clock, employing cutting-edge technologies like RFID, GPS, ERP, ticketing, and business intelligence tools. It serves as a centralised hub, monitoring operations from order booking to delivery, proactively addressing bottlenecks, optimising logistics expenditure and ensuring on-time deliveries. The data collected is leveraged to provide tailored solutions, delivering a seamless customer experience and propelling our logistics operations into the digital era.
We have implemented flexible and scalable digital solutions across our manufacturing units to enhance responsiveness. These initiatives span multiple years and leverage cutting-edge technologies like artificial intelligence, predictive analytics, and collaborative robotics. Through digitalisation, we achieved remarkable advancements in factory automation and end-of-line customisation, revolutionising critical areas such as pre-heater performance, kiln efficiency, clinker cooker operations, moisture content control, raw material planning, product quality prediction, power cost forecasting, and augmented reality-based equipment inspection. These digital endeavours have not only streamlined our operations but also positioned us as leaders in the digital transformation of the cement industry, driving efficiency and redefining excellence.
JSW Cement was established in 2009 and has grown to become one of the leading eco-friendly building materials companies globally with 19 million tonne per annum (mtpa) production capacity. “Our dedication has already established us as a significant market force in the southern, western and eastern regions and we have now set our sights on capturing the northern market,” says Nilesh Narwekar, CEO, JSW Cement, as he shares more on the company’s processes, prospects and plans. Speaking on the company’s key growth strategies, he adds, “At present, we have multiple brownfield projects underway across our plant locations, augmenting our production capacity for both clinkerisation and grinding sections. Additionally, we are implementing advanced WHRS (waste heat recovery system) and AFR (alternative fuel and raw materials) system to optimise operational efficiencies and minimise environmental impact. To fortify our presence in the eastern market, we successfully acquired Shiva Cement in Odisha and revamped its clinkerisation unit to 1.36 mtpa, which will play a pivotal role in supplying clinker to our Salboni and Jajpur grinding plants. We intend to make it an integrated plant.”What are the key growth strategies or expansion plans that JSW Cement has for the future?We have set our sights on becoming a formidable player & force to reckon with in the cement industry, driving growth and innovation that will propel us to new heights in the near future. We are already the World’s #1 eco-friendly cement company and our low-carbon products are setting new benchmarks in sustainable construction in India and across the globe. We cater to more than 12 states and 3 union territories of India from our 5800+ pan India strong dealer network served through two integrated and five grinding units. With our current production capacity nearing 19 million tons, we have set an audacious goal to reach 50 million tons by 2030. This ambitious growth shall be fuelled by a strategic combination of organic and inorganic approaches, ensuring a robust and sustainable trajectory. Our unwavering dedication has already established us as a significant market force in the southern, western, and eastern regions and now we have set our sights on capturing the highly lucrative northern market to close on our pan India presence.At present, we have multiple brownfield projects underway across our plant locations, meticulously augmenting our production capacity for both clinkerisation and grinding sections. Additionally, we are implementing Waste Heat Recovery System (WHRS) and Alternative Fuel and Raw Materials (AFR) systems to optimise operational efficiencies and minimise environmental impact.To fortify our presence in the eastern market, we successfully acquired Shiva Cement in Odisha, astutely revamped its clinkerisation unit to 1.36 million tons which would play a pivotal role in supplying clinker to our Salboni and Jajpur grinding plants. We intend to make it an integrated plant in near future.Meanwhile, the brownfield capacity expansion projects at our Dolvi (enhanced grinding capacity by ~2 million tons) and Nandyal units (enhanced clinkerisation from 6500 tpd to 8500 tpd) are complete, and we eagerly anticipate commissioning of the additional 2 million tons grinding unit at Vijaynagar within the next 2-3 months. We further intend to add another 4 million tons grinding capacity to our Vijaynagar plant which would take its overall grinding capacity to 10 million tons per annum. Additionally, our joint venture unit in Fujairah is ramping up its clinkerisation capacity from 1 MTPA to 2.36 MTPA, further solidifying our growth trajectory.As part of our strategic expansion into northern India, we have tactically acquired limestone mines in Nagaur, Rajasthan and Damoh, Madhya Pradesh. We have meticulously planned the establishment of clinkerisation and grinding units, alongside WHRS systems in these areas leading to a capacity addition of 10 million tons per annum. Currently, we are in advanced stages of land acquisition and obtaining statutory approvals for these Greenfield projects and expect the plants to come up in the next few years.Apart from cement production pursuits, we are resolutely focused on expanding and scaling up our Ready-Mix Concrete (RMC) and construction chemical businesses. Our aim is to achieve a pan-India presence in these segments in the near future, capitalising on the vast array of opportunities they offer.In addition to the above and in our quest for growth, we are actively exploring numerous other opportunities in the realm of inorganic expansion to consolidate and strengthen our position in the Indian cement market.Can you provide insights into JSW Cement's research and development efforts and any innovations in the cement industry that the company has introduced?We strongly believe in embracing a green environment, adopting circular economy principles, and pursuing decarbonisation. We have incorporated the same as a basic guiding force in whatever business pursuit we undertake and feel that our efforts would help create a more resilient and environmentally conscious society. As a part of our concerted action towards decarbonisation, we have established a dedicated research & development wing with the sole purpose of creating products that contribute to minimalistic carbon emission. We are already the world’s #1 eco-friendly cement company and our low-carbon products are setting new benchmarks in sustainable construction in India and across the globe. With an emission intensity of 220 Kg/ton that is 36 per cent of the global average (~600 Kg/ton) and 40 per cent of the national average (~540 Kg/ton), we have already positioned ourselves as a leader in the decarbonisation journey.Our R&D team has been diligently researching different types of hazardous slag to develop building products that possess superior strength, have enhanced durability, are resistant to corrosive environments, are complaint and most importantly, contribute significantly less to carbon emissions. Our environment friendly brands such as Concreel HD, Power Pro, Portland Slag Cement, and Compcem (Composite cement), have widely been embraced in the market. We are actively working on LC3 cement, Super Sulphated Cement, and innovative methods to maximise utilisation of various slags such as AOD, EAF, and LD slag. A notable achievement in circularity and sustainability is the substitution of Al-laterite mineral with ladle furnace slag, a by-product of steel plants. This substitution not only reduces CO2 emissions through pre-calcined CaO but also provides a valuable source of Alumina, which serves as a mineral additive during clinkerisation.We have also established partnerships with esteemed institutions to support our research and development centre. These include the FEhS Building Materials Institute in Duisburg, Europe and Eco Mister in Canada, who provide us with technological support. Additionally, we have been closely collaborating with renowned indigenous institutes such as IIT Delhi, IIT Bombay, IIT Guwahati, IIT Chennai, and IISc Bangalore. Through these collaborations, we are actively engaged in developing eco-friendly products and exploring innovative interventions that promote sustainability.Over the past few years, our R&D team has made significant progress in patenting slag-based cementitious products. With more than six patents already filed and several more in the pipeline, we are committed to driving innovation in the field. Notably, we have recently collaborated with IIT Roorkee to develop a patent for manufacturing eco-friendly and biodegradable cement bags, demonstrating our commitment to sustainable practices.In line with our commitment to eco-friendly practices, even our construction chemicals portfolio is developed using industrial wastes, ensuring that our products align with sustainable principles. One notable addition to our product line up is Slag Sand, a revolutionary substitute for conventional natural river sand, which is extensively used in concrete production. This innovative solution not only offers superior performance but also serves as a proven eco-friendly alternative. Further, by conserving river sand, we are also contributing to reduce ecological impacts which are caused by river sand mining.Our efforts in promoting a clean and green environment have not gone unnoticed. We have been honoured with numerous awards and accolades, recognising our contribution towards environmental preservation. In a recent achievement on June 23, we were awarded by the Ministry of Steel for our significant role in decarbonisation within the steel and cement industry. These recognitions inspire us to continue our mission of making the world a cleaner and healthier place to live.Through ongoing research, development, and collaborations, we remain steadfast in our pursuit of creating sustainable solutions and fostering a more environmentally conscious society.How does JSW Cement prioritise sustainability and environmental responsibility in its operations?JSW Cement, a part of the $23 billion JSW Group, is a leading global eco-friendly building materials company with a production capacity of 19 million tonnes per annum. Our business model is based on the philosophy of the circular economy. Despite cement production being energy-intensive and contributing to GHG emissions, we have achieved an impressive emissions intensity of only 220 kg/ton in FY22 (and bettered to 175 kg/ton in FY23), earning us the recognition as the Greenest company in terms of climate impact.As a member of the Global Cement and Concrete Association (GCCA), we are committed to the GCCA's roadmap for achieving net-zero concrete by 2050. Over the past eight years, we have quadrupled our production while halving our emissions by utilising high clinker substitution, particularly with slag. Currently, 90 per cent of our product portfolio is slag-based, with two-thirds of our raw materials sourced from by-products and waste materials.To achieve net-zero emissions, we are implementing strategies such as clinker substitution, using alternative fuels and raw materials, and increasing our clean and green energy portfolio. We blend clinker with supplementary materials like blast-furnace slag to produce blended cement, reducing carbon emissions. We aim to increase our use of alternative fuels and raw materials to over 30 per cent by 2030. Additionally, we are progressively incorporating solar power plants, Waste Heat Recovery Systems (WHRS), and renewable energy sources, targeting 50 per cent renewable power by 2030.Our grinding plants utilise advanced technologies, prioritise energy productivity and produce high-quality blended cement products with superior properties. We also focus on water sustainability, aiming to reduce freshwater withdrawal intensity by 15 per cent and become 5 times water positive by 2030 through increased use of recycled and harvested water and implementing water stewardship programmes.We are committed to preserving biodiversity and minimising our environmental impact. Our biodiversity management policy ensures minimal disturbance and we strive to achieve No Net Loss on biodiversity by 2030. We closely monitor and manage emissions to maintain air quality, exceeding regulatory limits. Our waste management follows the reduce-reuse-recycle approach, handling hazardous and non-hazardous waste appropriately. We prevent wastewater discharge outside our facilities to protect water bodies.Finally, we prioritise social sustainability by empowering local communities, upholding human rights, promoting fair labour practices, improving living conditions, and prioritising health, safety, wellness, and diversity within our workforce.What steps does JSW Cement take to ensure the quality and consistency of its cement products?Our Research and Development (R&D) centre in Vijayanagar maintains the highest standards of quality and consistency. Both the R&D centre and our individual plant quality control laboratories are equipped with cutting-edge facilities, including the Robo Lab, X-Ray fluorescence and diffraction machines, Optical Microscope, Compressive strength testing machine, Isothermal calorimetry, On-Line control systems, and other advanced Wet Classical chemistry instruments. These state-of-the-art instruments play a crucial role in monitoring and controlling the entire process value chain, from the sourcing of raw materials to the production of the finished product.To ensure the desired quality and consistency in our end products, we have meticulously developed specifications for various input raw materials such as Limestone, Laterite, Red mud, Steel slag, Flue dust, BF slag, Fly ash, Gypsum, and more. We employ regular sampling and chemistry determination techniques to effectively control the quality of these raw materials. Furthermore, we conduct meticulous assessments, including the determination of glass content in slag to ensure compliance with BIS standards, and microscopic analysis of different phases in the clinker to assess its quality and quantity.In addition to mineralogical and chemical characterisation, we thoroughly evaluate the final clinker-based OPC and slag cement products for their physical properties, including setting time, normal consistency, expansion, Blaine fineness, and compressive strength. These evaluations are carried out to ensure that the finished product aligns with the specifications outlined by the BIS codes for the respective grades of cement.To guarantee that both the raw materials and the finished product meet the acceptable specifications, we have developed standard operating procedures (SOPs) for various stages of quality assurance. These SOPs encompass crucial aspects such as sampling points, sampling frequency, identification of production batches, sample retention time, sample traceability, sample analysis time, and calibration of measuring and monitoring instruments. By adhering to these procedures, we maintain the consistency and reliability of our quality control processes.To further strengthen our commitment to quality, we subject the clinker and finished products to periodic checks conducted by third-party organisations, as well as by regulatory body BIS. These external assessments are essential in ensuring that our products consistently meet the established standards.Through the establishment of our advanced R&D centre, the implementation of stringent quality control measures, and the engagement of external verification, we demonstrate our unwavering dedication to delivering products of the highest quality. These initiatives enable us to meet the evolving demands of our customers while upholding the utmost standards of excellence in our industry.How does JSW Cement ensure supply chain efficiency?We have embarked on a ground-breaking digital revolution within our logistics operations, fuelled by a steadfast commitment to elevating service levels and mastering cost management. Our triumphant approach encompasses three formidable pillars: Process Monitoring, Movement Control, and Cost Optimisation, converging to deliver unparalleled outcomes.To oversee the entire operation, from the moment an order is received until the materials are delivered to the customer, we employ a digital brain called the logistics control tower (LCT). The LCT utilises cutting-edge technologies such as RFID and GPS, and extensively leverages analytics to analyse the data and information collected.Our Yard Management System (YMS) assists in aligning sales orders with available trucks in the parking yard and organizes their sequencing through various stages, from gate-in to invoicing.For movement within our manufacturing plant, both inbound and outbound, we employ RFID tags and sensors. The Plant Logistics Management System (PLMS) enables us to monitor the internal movement of trucks within the plant, ensuring efficient control and avoiding congestion, thereby facilitating timely truck loading.External movement occurs outside the plant, from the manufacturing plant to the customer and vice versa. This external movement is tracked using GPS, which monitors the truck's movement and stoppages. Whenever an abnormal stoppage occurs during outbound movement, the Logistics Control Tower is immediately alerted. This way, the LCT plays a crucial role in our Track N Trace system, acting as a monitoring mechanism for external movement. It escalates any issues to relevant internal and external stakeholders, minimising truck stoppages.Cost optimisation, our ultimate objective, is achieved through tracking various logistics Key Performance Indicators (KPIs) using an analytics layer. Data from the PLMS, Track N Trace system, and ERP are integrated into a business intelligence platform, which then provides feedback to the LCT team round the clock. This continuous flow of information enables us to make necessary course corrections. By reducing the order-to-delivery time and order-execution time, we can increase the number of trips per truck, a crucial factor in negotiating favourable rates with transporters. We constantly refine our routes to determine the most optimal paths, resulting in scientifically accurate freight rates. Furthermore, we optimise our truck fleet size, matching it appropriately to each route at the right time, thereby achieving economies of scale.Overall, our digitisation efforts have revolutionised our logistics operations, enhancing service levels, managing costs, and driving efficiency throughout the entire supply chain.Can you share some insights into JSW Cement's approach to digital transformation and utilisation of technology in its processes?Embracing the winds of change, we have embarked on a profound digitalisation voyage, permeating every aspect of our value chain. From raw material sourcing to production, logistics to customer engagement, and even beyond to our internal operations, we have harnessed the power of technology to reshape our company and redefine excellence. All of the above has been done with an objective of empowering our workforce to make smarter, quicker decisions by transforming data into an accessible and reusable asset.Today, customers are digitally engaged and are more data conscious. They expect us to offer customised solutions that can be accessed on demand and can be seamlessly integrated into their lives. Digitalisation is helping us create new platforms to drive better engagement with our customers and other stakeholders, enhance our agility and creating greater efficiencies in our operations. In last couple of years, we have launched more than 12 apps and have carried out 20+ business process engineering initiatives which itself is a great testament of our focus towards digitalisation.We are making great strides in digitalisation with JSW Aikyam, Saathi App, DGO App and NonTrade App along with state-of-the-art logistics control tower, which has helped us digitally track and control logistics movement across our value chain and enhance our overall efficiency.The Smart JSW Saathi app has already proven to be a powerful catalyst for JSW sales promoter’s preferences and for deepening engagement. The platform helps sales promoters with placing orders, view order status, real-time tracking of their dispatches, online payment, real-time settlement and update of their outstanding, checking their financial books, collaborating with JSW departments through service requests, and downloading documents required in their day-to-day operations.Through comprehensive digitisation, we have transformed our logistics operations across all manufacturing units, attaining a holistic view of the supply chain. RFID technology empowers us with complete visibility of trucks within our yards, allowing us to efficiently schedule loading and unloading processes, thus meeting targeted turnaround times. By optimising costs and planning truck routes, we navigate traffic seamlessly, while continuous tracking ensures driver safety and enables timely communication with transporters. Our logistics control tower, a state-of-the-art facility, operates round the clock, employing cutting-edge technologies like RFID, GPS, ERP, ticketing, and business intelligence tools. It serves as a centralised hub, monitoring operations from order booking to delivery, proactively addressing bottlenecks, optimising logistics expenditure and ensuring on-time deliveries. The data collected is leveraged to provide tailored solutions, delivering a seamless customer experience and propelling our logistics operations into the digital era.We have implemented flexible and scalable digital solutions across our manufacturing units to enhance responsiveness. These initiatives span multiple years and leverage cutting-edge technologies like artificial intelligence, predictive analytics, and collaborative robotics. Through digitalisation, we achieved remarkable advancements in factory automation and end-of-line customisation, revolutionising critical areas such as pre-heater performance, kiln efficiency, clinker cooker operations, moisture content control, raw material planning, product quality prediction, power cost forecasting, and augmented reality-based equipment inspection. These digital endeavours have not only streamlined our operations but also positioned us as leaders in the digital transformation of the cement industry, driving efficiency and redefining excellence.
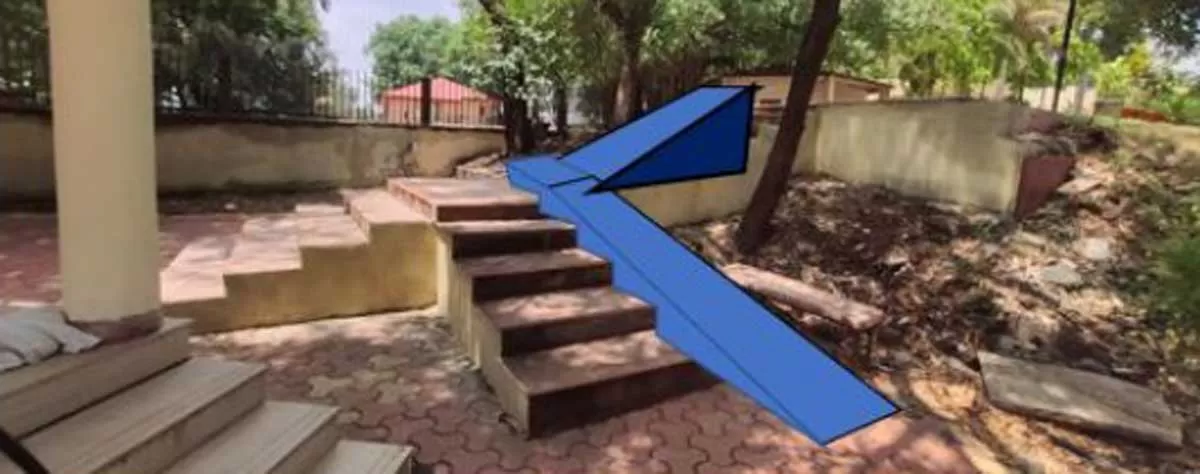
Madhya Pradesh Champions Inclusive Tourism at Heritage Sites
On the occasion of World Heritage Day, Madhya Pradesh is taking a significant step toward inclusive tourism by making its historical sites accessible to all — especially persons with disabilities. The state is rolling out its ‘Accessibility Infrastructure and Development’ project at Maheshwar, Mandu, Dhar, and Orchha, aiming to create a more welcoming experience at these iconic cultural destinations.The initiative, under the leadership of Chief Minister Dr Mohan Yadav and Tourism Minister Shri Dharmendra Bhav Singh Lodhi, includes infrastructure upgrades such as ramps, Braille signage, w..
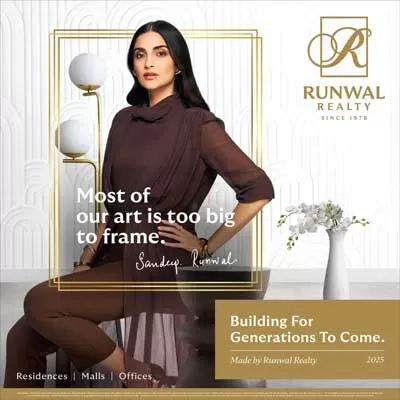
Runwal Realty Onboards Sonam Kapoor as Brand Ambassador
Real estate major Runwal has unveiled a refreshed identity as Runwal Realty, signalling a renewed commitment to crafting spaces that stand the test of time. With this refresh, the brand unveils its new philosophy: “Building for Generations to Come” and welcomes Bollywood star and global fashion icon Sonam Kapoor as its brand ambassador. This evolved identity reflects Runwal Realty’s commitment to creating not just homes, but heirlooms—crafted through visionary design, meticulous planning, global design expertise and an unwavering focus on quality. With the customer at its core, each de..
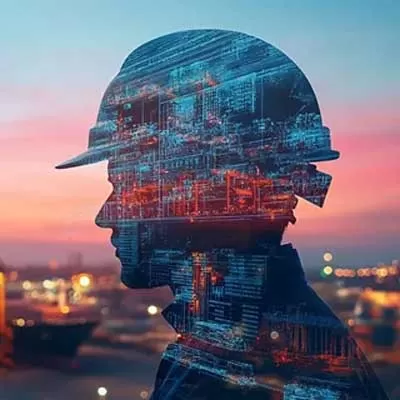
Emerging Trends in Infrastructure and Transport 2025: KPMG
KPMG’s latest report, The Great Reset: Emerging Trends in Infrastructure and Transport 2025 edition, sheds light on the profound changes transforming the global infrastructure landscape. As industries adapt to the challenges posed by climate change, economic pressures, and technological advancements, the report identifies key trends and provides actionable insights for leaders in infrastructure and transport sectors. “In today’s interconnected world, the lack of standardized supply chain practices is not just an operational challenge—it’s an environmental and economic one. We’..
Latest Updates
Recommended for you
Subscribe to Our Newsletter
Get daily newsletters around different themes from Construction world.
Advertisement
Advertisement
subscribe to the newsletter
Don't miss out on valuable insights and opportunities
to connect with like minded professionals