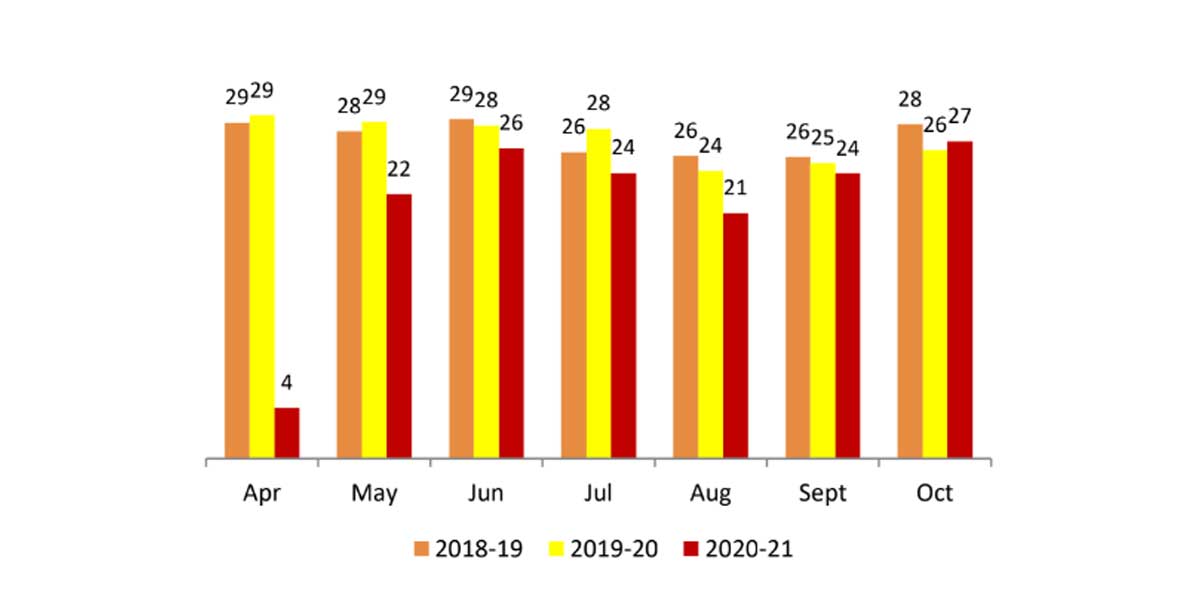
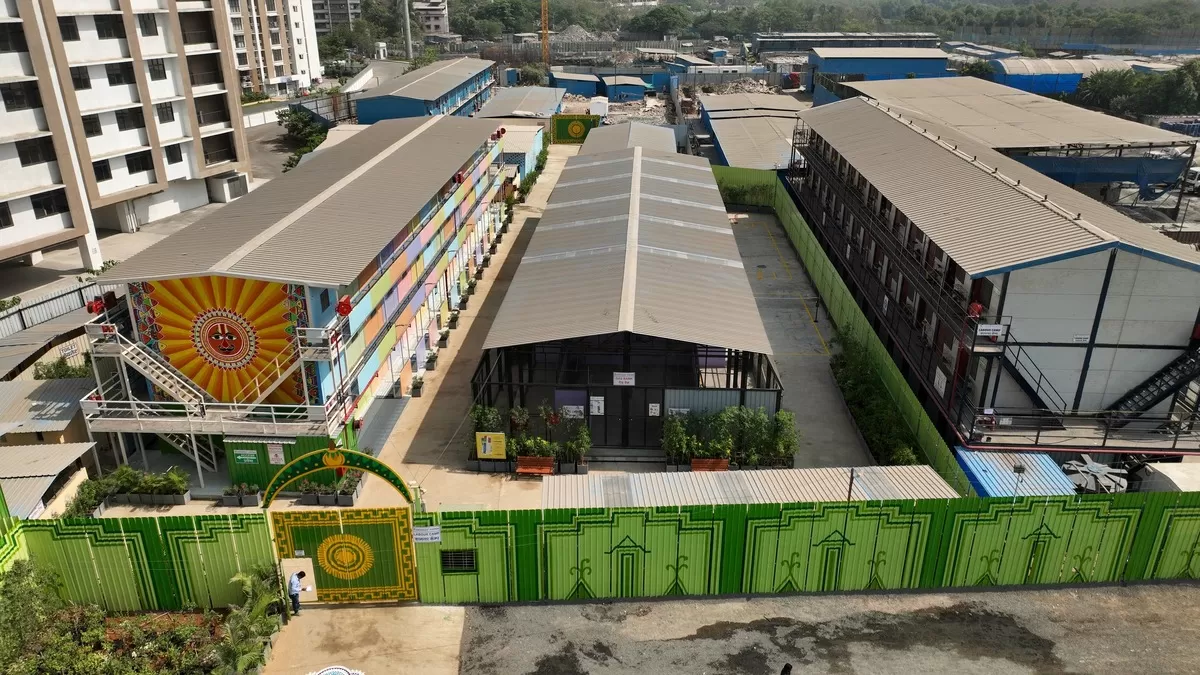
Rustomjee Unveils 35,000 Sq. Ft. Industry-First Labour Housing for 500 Workers
Rustomjee Group has launched a 35,000 sq. ft. labour housing facility at its Urbania site in Thane, marking a first-of-its-kind initiative in Indian real estate. Inaugurated on April 13, the accommodation can house 500 workers across 84 well-ventilated rooms, each 10 ft by 10 ft, with up to six individuals per room.Rooted in Rustomjee’s ethos of care and community, the facility is designed not just for shelter, but as a holistic, nurturing ecosystem. “At Rustomjee, we believe that the people who build our cities deserve to be at the heart of them. Our newly developed labour accommodation a..
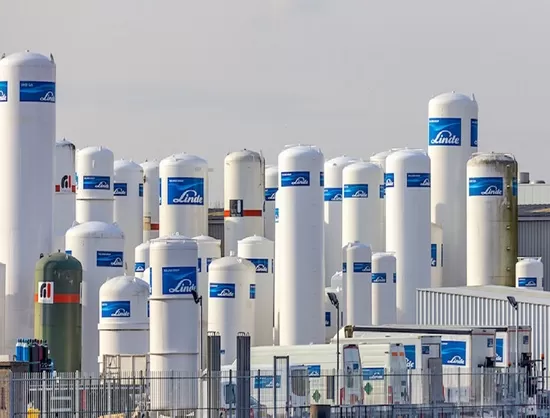
Cyient wins key green hydrogen contract for project in Norway
Cyient, the Indian multinational technology company, has secured a strategic contract to support GreenH Bodø in the development and execution of a pioneering green hydrogen production and distribution facility at Langstranda in Bodø, Norway. This flagship initiative is part of a joint venture between GreenH, a Norwegian green hydrogen infrastructure firm, and Luxcara, a Hamburg-based independent asset manager specialising in renewable energy projects across Europe. The project represents a major step towards fulfilling Norway’s ambitious renewable energy goals, particularly within the ma..
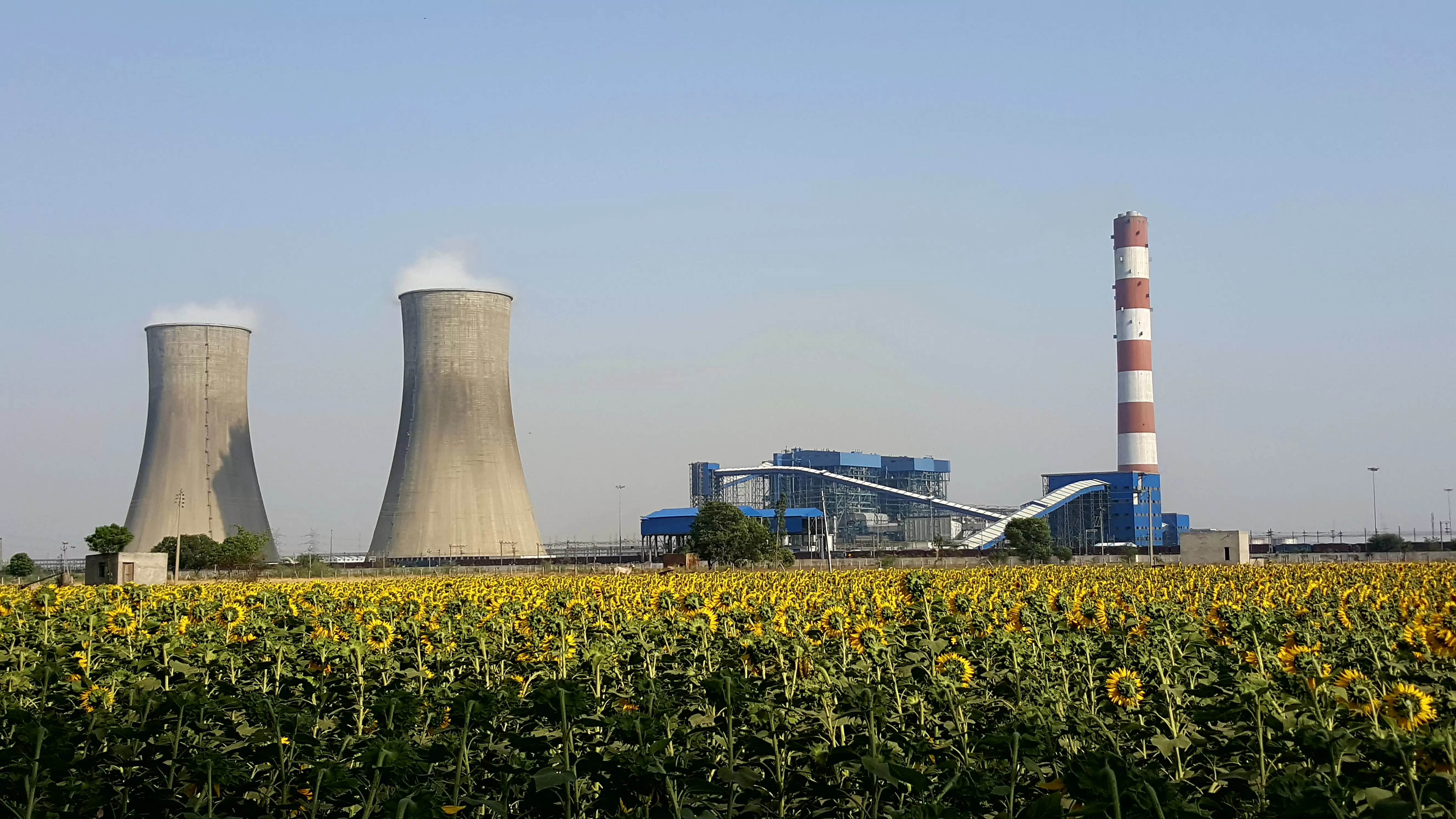
Thermal power capacity addition slows 32% amid project delays
India's thermal power generation capacity expansion has decelerated significantly in the first 11 months of FY25, witnessing a 32% drop compared to the same period last year. Provisional data from the Central Electricity Authority (CEA) indicates that only 3.9 GW of thermal capacity was added up to February 2025, down from 5.7 GW in the same period of FY24. Thermal power plants—predominantly coal-fired, with some based on gas and diesel—remain the backbone of India’s energy mix. The decline in capacity additions has been largely attributed to delays in project commissioning, land acqui..