Acquisition of Parador was the biggest contributor to our topline growth
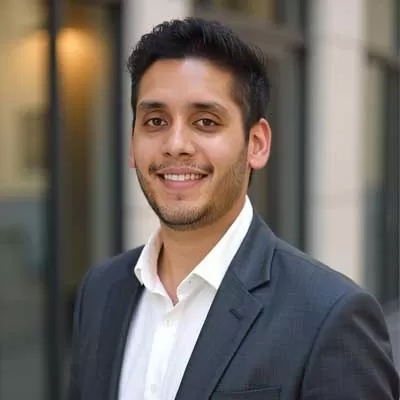
Gini & Jony Appoints Harsh Agarwal as New CEO
Suditi Industries Ltd. announced the official appointment of Harsh Agarwal as the Chief Executive Officer of their renowned kidswear brand, Gini & Jony. This internal decision received Board approval, and formal notification has been submitted to the Bombay Stock Exchange (BSE). The appointment marks a pivotal moment for the 45-year-old brand as it embarks on a new phase focused on innovation, expanded reach, and enhanced consumer engagement.Harsh Agarwal succeeds Prakash Lakhani, the visionary founder and former CEO who has led the brand since its inception. Lakhani will now transition in..
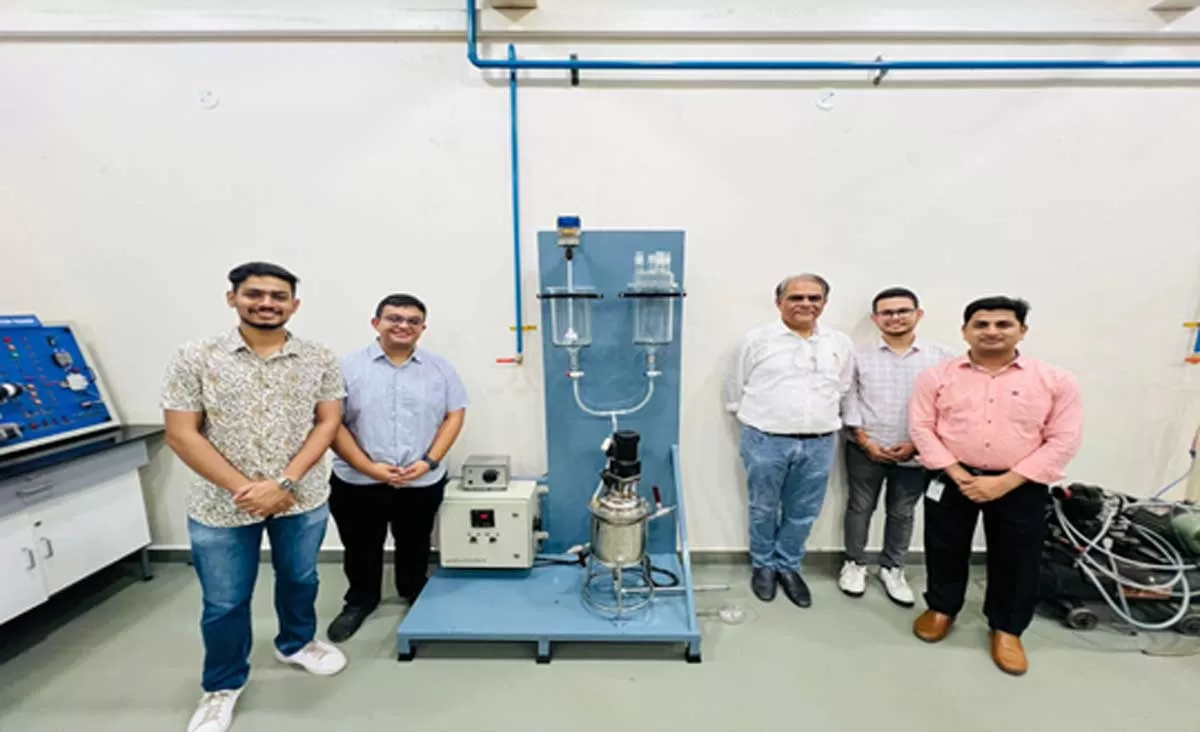
MITWPU Announces Novel Hydrogen Production From Sugarcane Juice
MIT World Peace University (MITWPU) has made significant advancements in sustainable energy research, with two pioneering projects: a novel process for generating green hydrogen directly from sugarcane juice and an innovative batch reactor system for biodiesel production using agro waste based heterogeneous catalysts. These developments underscore MITWPU’s commitment to India's green energy transition and sustainable future. The university has developed a unique process to generate hydrogen from sugarcane juice using microorganisms, which also converts carbon dioxide into ac..
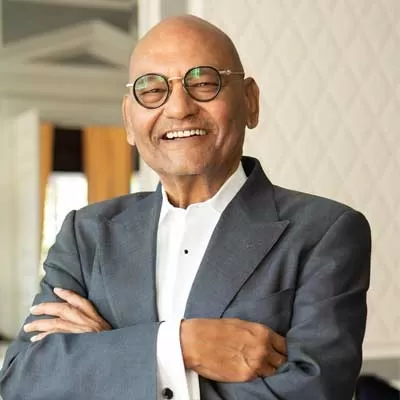
Vedanta Chairman Hails Rajasthan as India's Next Industrial Powerhouse
In a compelling message posted on social media, Vedanta Chairman Anil Agarwal highlighted the vast untapped mineral wealth of Rajasthan and the need for accelerating industrial development to further unlock the state’s economic potential. Drawing attention to GDP data, he noted that Rajasthan despite being richly endowed with natural resources, trails behind states like Gujarat, Karnataka, and Tamil Nadu, all of which have GDPs exceeding $300 billion. This comes at a time when Rajasthan is charting its path towards a $ 350 billion economy by 2030. With a GDP of $196 billion, Rajas..