Progress on Structural Technologies for Affordable Housing
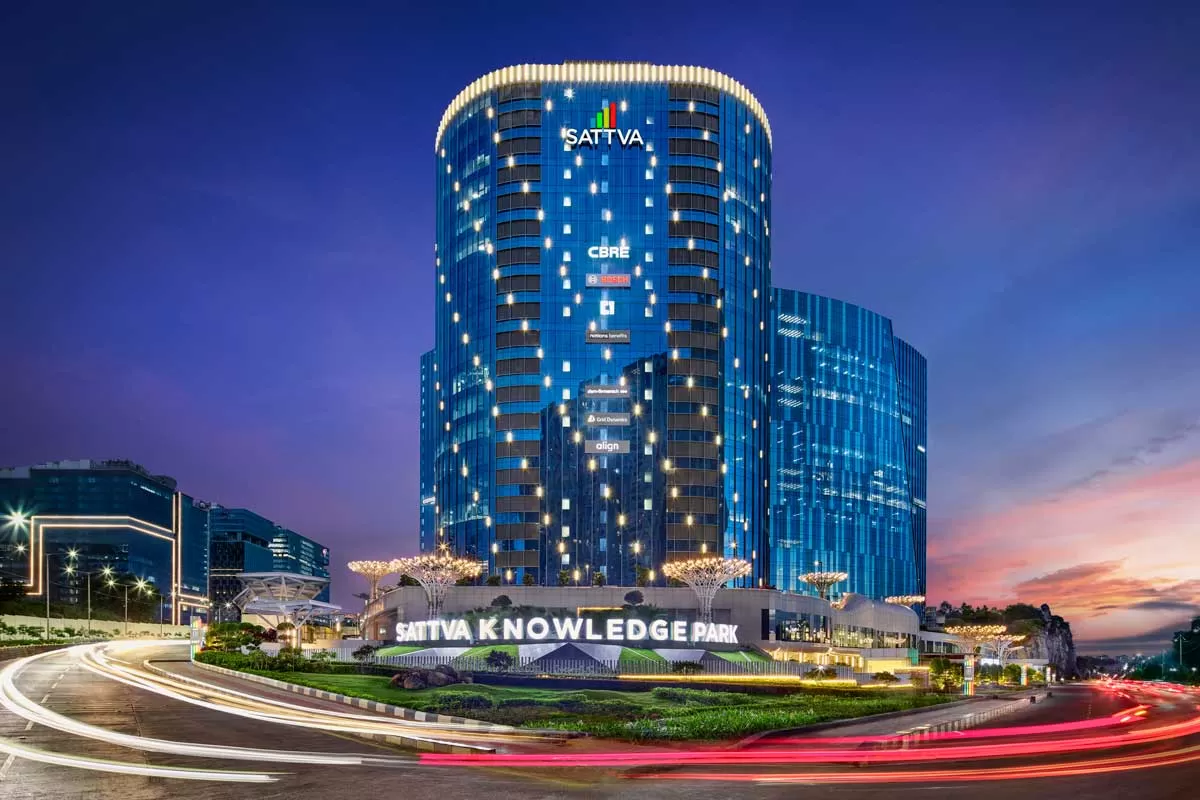
The Only Way is Up!
In 2025, India’s real-estate market will be driven by a confluence of economic, demographic and policy-driven factors. Among these, Boman Irani, President, CREDAI National, counts rapid urbanisation, the rise of the middle class, policy reforms like RERA and GST rationalisation, and the Government’s decision to allow 100 per cent FDI in construction development projects (including townships, housing, built-up infrastructure, and real-estate broking services).In the top metros, especially Bengaluru, followed by Hyderabad and Pune, the key drivers will continue to be job creation a..
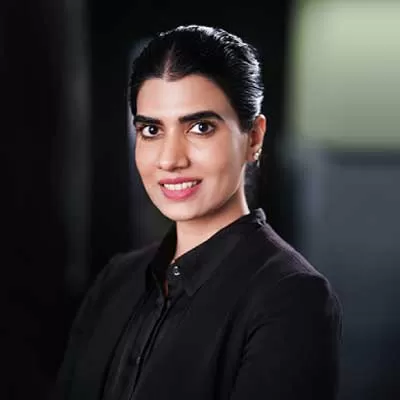
Organisations valuing gender diversity achieve higher profitability
The building materials industry is projected to grow by 8-12 per cent over the next five years. How is Aparna Enterprises positioning itself to leverage this momentum and solidify its market presence?The Indian construction and building materials industry is projected to witness significant expansion, with estimates suggesting an 8-12 per cent compound annual growth rate (CAGR) over the next five years. This growth is fuelled by rapid urbanisation, increased infrastructure investments and sustainability-focused policies. With India's real-estate market expected to reach $ 1 trillion by 2030, t..
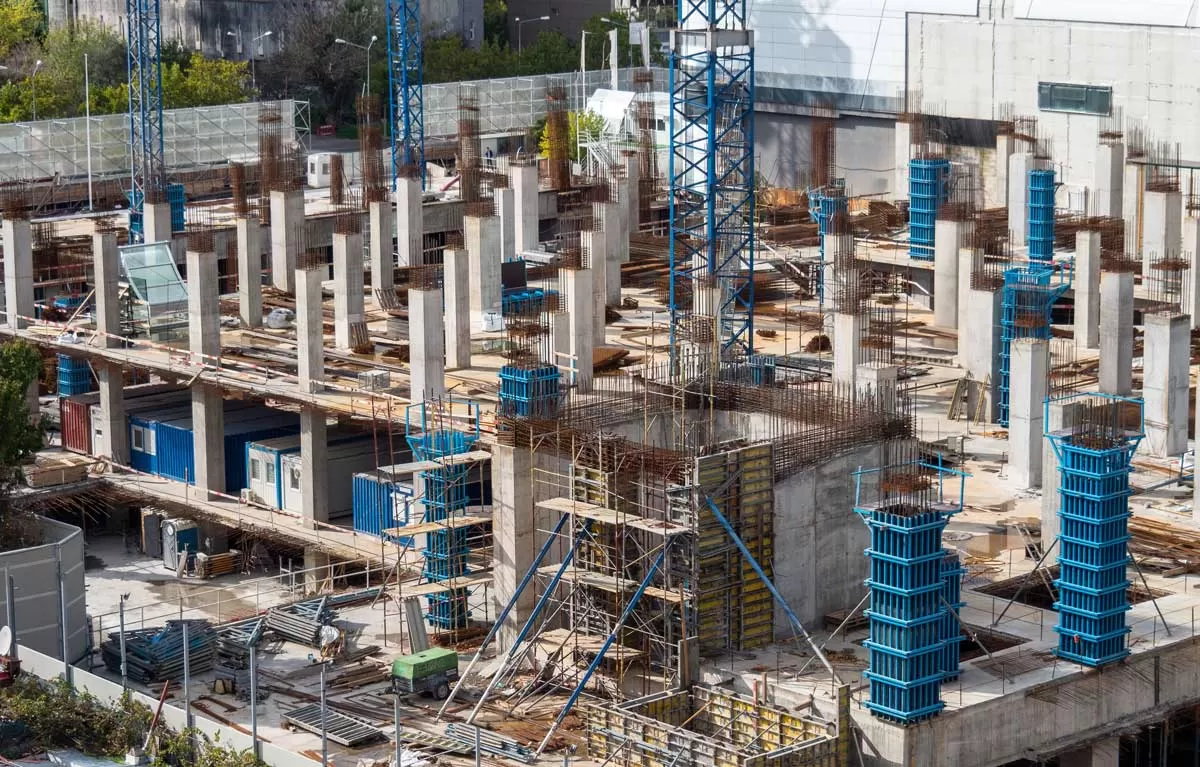
Dealing with Delays
Delays have beleaguered many a construction project in India, hampering the country from building to its ability and potential, and leading to additional costs incurred by the contractor. The reasons for delayIn India, delays mainly occur owing to obtaining statutory approvals, non-provisioning of right of way, utility diversion and approval of drawings and design. Delays are broadly classified based on responsibility and effect. Excusable delays arise from factors beyond the contractor’s control, such as force majeure events or employer-induced delays. These delays generally entitle th..